Tin melting temperature is a key parameter in the soldering process and has a direct impact on the quality of the solder. Understanding the melting temperature of tin and its application is the basis for ensuring the reliability of soldered connections.
Tin is a low melting point metal,solid at room temperature, need to be heated to a certain temperature to become liquid.The melting point of tin is based on the purity of tin and whether the impurities vary, generally between 183 ℃ – 215 ℃. In the electronics industry, the electronic grade tin commonly used in the higher purity requirements, melting temperature of about 231 ℃. The tin commonly used in the general industry has a lower purity, and the melting temperature is usually 183℃-215℃.
Tin melting methods mainly include hot melt tin welding, manual welding and other auxiliary welding technology
1.Hot pressure tin welding
The principle of hot melt soldering is to first print the solder paste on the PCB circuit board, and then use the heat to melt the solder and connect the electronic components that need to be connected.This method ensures an efficient and stable soldering process and is suitable for mass production. Due to its precise temperature control capability,it can effectively avoid soldering defects caused by overheating.
2.Manual soldering
Manual soldering is a common soldering method,usually using a soldering iron to melt the solder and solder.The temperature regulation of the soldering iron is extremely important to ensure that the temperature of the tin in the appropriate range to avoid too high or too low temperature affect the soldering effect. This method is particularly effective in the case of small and complex assemblies,allowing the operator to have more direct control over the solder joint.
3.Auxiliary Welding Techniques
In addition to the above two main methods,auxiliary soldering techniques such as hot air soldering and soldering ovens are also widely used.Hot air guns can be used to melt tin over large areas,while tin ovens offer the possibility of high volume,uniform soldering.The use of these methods better meets the different process requirements and soldering needs of electronic products.
Influence of tin melting temperature on solder quality
Effect of too high temperature
Setting the temperature too high can lead to degradation of soldering quality,and problems such as tin bridging and component damage may occur. For example,when the temperature in the reflow zone is too high,the solder and flux will evaporate prematurely,which reduces the wetting effect,and this can lead to the occurrence of false or raw soldering.In addition,electronic components such as resistors,transistors,and other sensitive components may lose function due to high temperatures, causing product failure.
Effects of too low a temperature
Conversely,if the reflow temperature is set too low,the solder paste may not melt sufficiently,resulting in poor solder joint quality.The solder balls formed on the solder joints may not only affect circuit conduction,but also cause potential hazards such as short circuits.Therefore,it is very important to ensure that the solder paste reaches its melting temperature within the specified time.
How to control the tin melting temperature on circuit boards
Controlling the tin melting temperature of tin on a circuit board is critical to the quality and efficiency of soldering. Here are some ways to control the melting temperature of tin:
- Control the heating time and temperature. The longer the heating time and the higher the heating temperature, the higher the melting temperature of tin. When heating the board, it should be controlled according to different soldering points.
- Choose the right solder.Different types of solder contain different metal compositions and have different melting temperatures.The solder that meets the requirements should be selected for welding.
- Enhance the preheating. Circuit boards and welding instruments need to be preheated to reduce the impact of temperature changes during welding.
- Control the welding speed.Soldering speed is too fast will lead to the solder joints are not completely melted,and the soldering speed is too slow will allow other components on the circuit board to overheat.
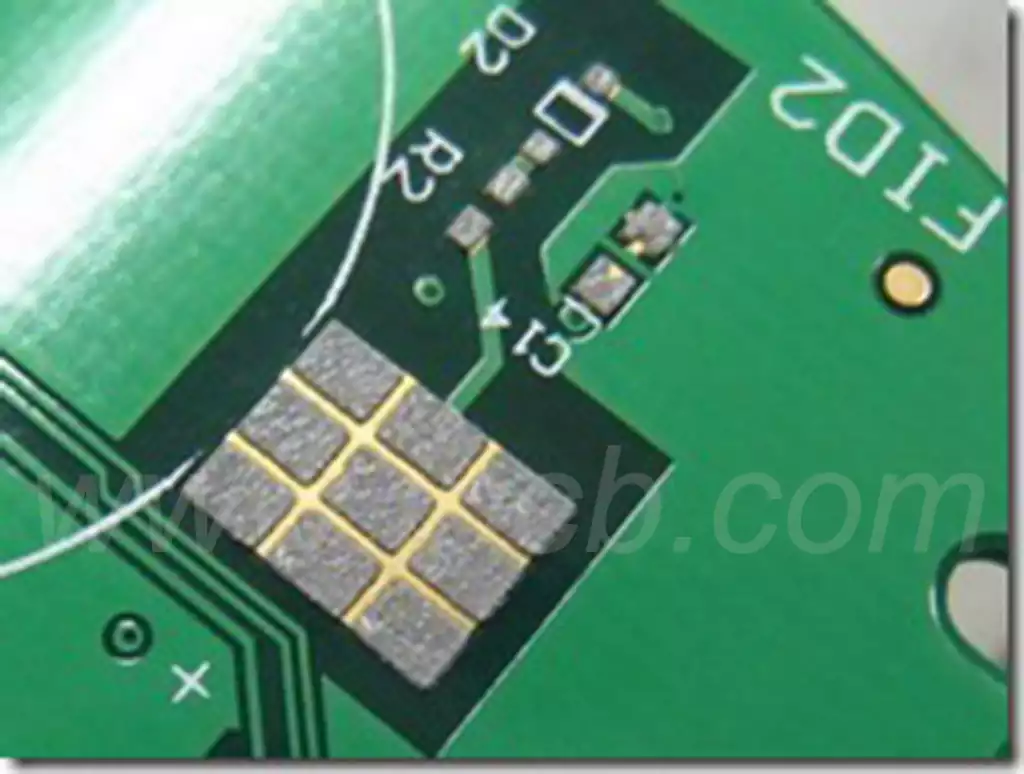
Tin melting temperature has a significant impact on the quality of the circuit board, too high or too low melting point temperature may cause soldering defects and circuit board damage. Proper temperature control not only improves soldering quality, but also extends the life of the board.
1.The effect of too high a temperature
When the melting temperature of the solder paste is too high, the temperature of the soldering area will also increase. This high temperature effect can lead to deformation of the substrate or breakage of the solder joints, which can seriously affect the overall quality of the board. In addition, high temperatures can also cause the solder to melt and scatter, increasing the speed of oxidation reaction, which will further reduce the quality of the solder.
2.The effect of too low a temperature
If the soldering temperature is too low, the solder may not be able to fully integrate, resulting in weak soldering. This will lead to the circuit board in the working process of poor contact or short-circuit problems, thus affecting the normal operation of the equipment. Therefore, it is crucial to precisely control the soldering temperature to ensure that the solder can melt properly and combine well with the circuit board and components.
3.Importance of temperature control
Controlling the temperature during the soldering process is one of the key factors to ensure the quality of circuit board soldering.The correct preheating time and soldering temperature not only ensures good solder flow, but also improves the reliability of the solder joints. If the preheating time is too short, it will lead to insufficient heating of the solder, which will lead to the formation of bubbles and tin particles,while too long a preheating time may make the components overheat.
4.Soldering process and parameter adjustment
The quality of soldering is affected by a variety of parameters, including the characteristics of the solder paste, substrate materials, component solderability and so on. Therefore, in the development of the soldering process, must take into account these factors, reasonable setting of the soldering temperature and time. Continuous optimization of these process parameters helps to improve the soldering quality of the board and reduce the production defect rate.
Reasonable control of the tin melting temperature as well as the soldering process parameters is essential to improve the quality of soldering. Focusing on factors such as heating time, solder selection, preheating methods and soldering speed can significantly improve the reliability of soldered connections, extend board life and enhance product performance. These optimization measures will help the electronics manufacturing industry achieve higher quality standards and market competitiveness.