In the rapidly evolving world of electronics, innovation and efficiency are paramount. One such innovation that has garnered significant attention is the Aluminum Flex Printed Circuit Board (PCB).
Combining the flexibility of traditional flex PCBs with the durability and heat dissipation properties of aluminum, Aluminum Flex PCBs are finding applications in a variety of high-performance electronics. This article delves into the composition, manufacturing process, benefits, applications, and future potential of Aluminum Flex PCBs.
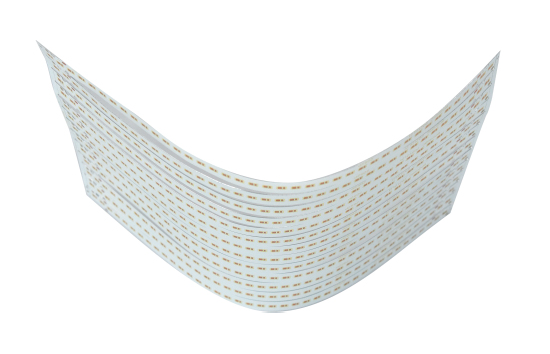
Composition and Structure
Aluminum Flex PCBs are a hybrid of aluminum-based and flexible PCBs. They consist of a flexible dielectric layer, usually polyimide, that is bonded to an aluminum substrate. The key components include:
- Aluminum Substrate: Acts as the base layer, providing mechanical support and excellent thermal conductivity.
- Dielectric Layer: A flexible insulating layer that can bend and flex without breaking.
- Conductive Layer: Typically made of copper, where the circuitry is etched.
- Coverlay: A protective layer that shields the circuitry from environmental damage.
Properties of Aluminum
Aluminum is chosen for its advantageous properties:
- Thermal Conductivity: Aluminum has high thermal conductivity, allowing efficient heat dissipation.
- Mechanical Strength: It provides robust mechanical support, reducing the risk of damage during handling and operation.
- Lightweight: Despite its strength, aluminum is relatively lightweight, an important factor in mobile and portable devices.
Manufacturing Process
The manufacturing of Aluminum Flex PCBs involves several critical steps to ensure flexibility and durability:
- Preparation of the Aluminum Substrate: The aluminum substrate is cleaned and treated to enhance adhesion.
- Application of the Dielectric Layer: A flexible dielectric layer, such as polyimide, is applied to the aluminum substrate using adhesives.
- Circuit Patterning: Copper foil is laminated onto the dielectric layer and etched to form the required circuit patterns.
- Application of Coverlay: A protective coverlay is applied to protect the circuitry.
- Cutting and Shaping: The PCB is cut and shaped according to the design specifications.
- Quality Control: Rigorous testing is conducted to ensure the PCB meets all mechanical and electrical requirements.
Benefits of Aluminum Flex PCBs
Enhanced Thermal Management
One of the standout benefits of Aluminum Flex PCBs is their superior thermal management. The aluminum substrate effectively dissipates heat away from critical components, reducing the risk of overheating and improving the overall reliability of the electronic device. This makes them particularly suitable for high-power applications such as LED lighting, automotive electronics, and power supplies.
Flexibility and Durability
Combining the flexibility of traditional flex PCBs with the strength of aluminum, these PCBs can withstand mechanical stresses and bending. This is particularly beneficial in applications where space is constrained, and the PCB needs to fit into tight or irregularly shaped enclosures.
Lightweight and Compact Design
The use of aluminum allows for a lightweight design without compromising on strength and durability. This is essential in modern electronic devices where reducing weight and size is crucial, such as in mobile devices, wearables, and aerospace applications.
Reliability and Longevity
Aluminum Flex PCBs offer enhanced reliability due to their robust construction and superior thermal properties. The risk of thermal expansion and contraction, which can cause traditional PCBs to crack or fail, is significantly reduced. This ensures a longer lifespan and better performance over time.
Applications of Aluminum Flex PCBs
Automotive Industry
The automotive industry demands high-performance, reliable, and heat-resistant components. Aluminum Flex PCBs are ideal for use in automotive lighting systems, engine control units, and infotainment systems, where they can handle high temperatures and mechanical stresses.
LED Lighting
LED lighting systems generate significant heat, which can affect performance and longevity. Aluminum Flex PCBs efficiently dissipate heat, ensuring the LEDs operate within optimal temperature ranges, thus enhancing their lifespan and reliability.
Consumer Electronics
In consumer electronics, where compact and lightweight designs are paramount, Aluminum Flex PCBs offer the perfect solution. They are used in smartphones, tablets, laptops, and wearable devices, providing the necessary flexibility and durability.
Medical Devices
Medical devices require precision, reliability, and miniaturization. Aluminum Flex PCBs are used in medical imaging equipment, diagnostic devices, and wearable health monitors, where their flexibility and thermal management capabilities are critical.
Aerospace and Defense
In aerospace and defense applications, where reliability and performance are crucial, Aluminum Flex PCBs are employed in communication systems, navigation equipment, and avionics. Their ability to withstand extreme conditions and mechanical stresses makes them ideal for such demanding environments.
Future Potential and Innovations
Advancements in Material Science
Ongoing advancements in material science are expected to further enhance the properties of Aluminum Flex PCBs. New dielectric materials with improved flexibility and thermal conductivity are being developed, which will further expand their application range.
Integration with Advanced Technologies
The integration of Aluminum Flex PCBs with advanced technologies such as 5G, IoT, and AI will drive innovation in various industries. These PCBs will play a critical role in the development of next-generation devices that require high performance, reliability, and compact design.
Sustainable Manufacturing Practices
As the electronics industry moves towards more sustainable practices, the use of recyclable materials like aluminum in PCBs will become more prevalent. Aluminum Flex PCBs align well with these goals, offering an environmentally friendly alternative to traditional PCBs.
Conclusion
Aluminum Flex PCBs represent a significant advancement in PCB technology, combining the best attributes of aluminum and flexible PCBs. Their superior thermal management, flexibility, durability, and lightweight design make them ideal for a wide range of applications, from automotive and consumer electronics to medical devices and aerospace. As technology continues to evolve, Aluminum Flex PCBs will undoubtedly play a pivotal role in the development of innovative, high-performance electronic devices.
Above is all my sharing. Thanks for you read.