Vehicle electronic PCB board is a circuit board specifically designed and manufactured for automotive electronic systems. It carries functional modules such as the engine control unit (ECU), in car entertainment system, and driving assistance system, playing a crucial role in connecting and transmitting conductive signals, ensuring the normal operation of automotive electronic devices.
With the trend of Vehicle electronics and informatization, the demand for Vehicle PCB boards continues to grow. Especially in the fields of new energy vehicles and intelligent vehicles, the application of PCBs in Vehicle electronics is expected to continue to increase, bringing more growth opportunities to related industries.
The future innovation of PCB technology in the field of vehicle electronics may mainly focus on the following aspects:
Electrification: With the rise of new energy vehicles, the demand for electronic control systems and battery management systems continues to increase. These systems require higher technical requirements for PCBs, especially in terms of stability and safety. For example, Battery Management Systems (BMS) have very high requirements for PCB boards and typically use multi-layer boards with better stability. In addition, flexible printed circuit boards (FPCs) are gradually replacing traditional battery harnesses, which enhances the application value of PCBs in new energy vehicles.
Intelligence: The development of intelligent cars has driven the application of advanced driving assistance systems (ADAS) and intelligent cockpit technologies. These systems require higher performance PCBs to support their complex electronic functions. For example, sensors and controllers in ADAS systems have strict requirements for the reliability and performance of PCBs.
Technical and customer barriers: With the increasing demand for high-frequency PCBs, FPCs, and HDI boards in new energy vehicles, higher requirements have been placed on the technical capabilities of automotive PCB manufacturers. At the same time, the electronic control system and assisted driving system of new energy vehicles are related to driving safety, and require higher stability and safety of vehicle PCBs. It is more difficult to pass customer certification, and customer barriers are significantly higher than in the traditional automotive field.
Market competition and economies of scale: The value of new energy vehicle PCBs is about 6 times that of traditional cars, which means that binding large customers can obtain larger orders. Once obtaining PCB orders for core components, it will bring huge value and make it easier to form economies of scale. Domestic manufacturers benefit from the improvement of automotive electronic integration and need to participate in their design process early on, making the connection between PCB suppliers and vehicle manufacturers closer.
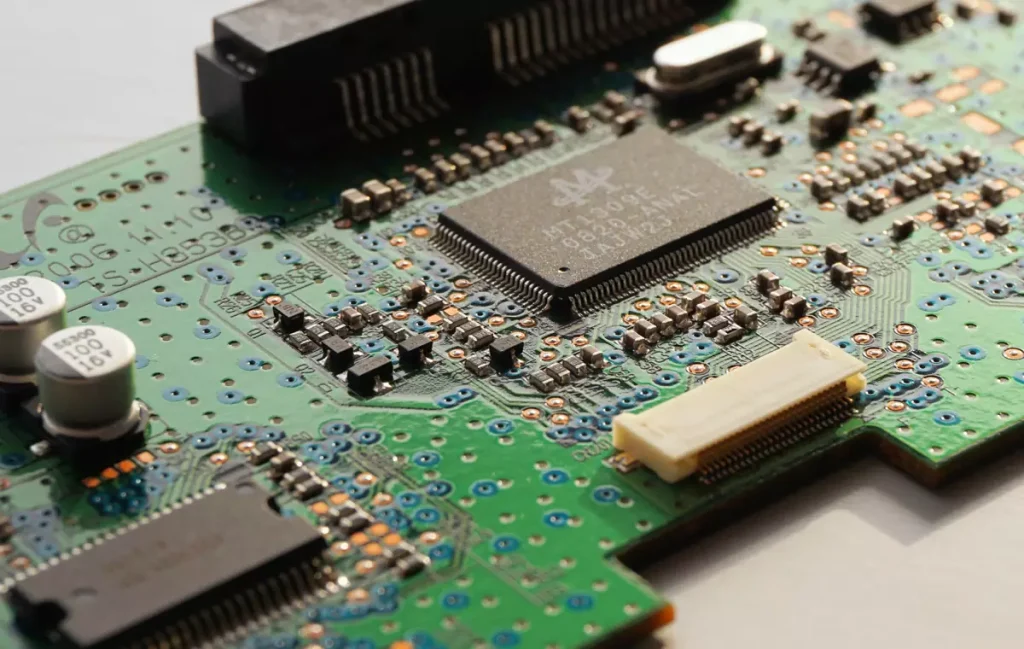
Intelligent automotive electronics have had a positive impact on the PCB industry, not only driving market growth but also providing new development opportunities for PCB manufacturers. With the continuous transformation of the automotive industry, the application of PCBs in automotive electronics is expected to continue to increase, bringing more growth opportunities to related industries.
Overview of Automotive Electronics Industry Standards
IPC Standards: IPC (Association Connecting Electronics Industries) has developed a series of standards for electronic manufacturing, among which IPC-A-600 and IPC-A-610 are the basic standards for evaluating PCB quality and acceptability. For automotive applications, IPC-6012DA “Qualification and Performance Specification for Automotive Applications” is a PCB requirement specifically designed for the automotive industry.
ISO/TS 16949 (now IATF 16949): This is a specific quality management system standard in the automotive industry that requires suppliers to maintain a high level of quality in the design, development, production, installation, and service processes. Although mainly targeting whole vehicle manufacturers and their direct suppliers, its principles also apply to PCB manufacturers.
AEC-Q200: Among the series of standards developed by the Automotive Electronics Council (AEC), AEC-Q200 specifically focuses on the qualification certification of passive components. Although it does not directly specify PCBs, it reflects the strict reliability requirements that automotive electronic components must meet. The materials and components used in PCBs should comply with the spirit of this standard.
UL Standards: A series of safety standards from Underwriters Laboratories (UL), such as UL 796, have specific requirements for the electrical safety and fire performance of PCBs to ensure the safety of automotive electronic equipment under extreme conditions.
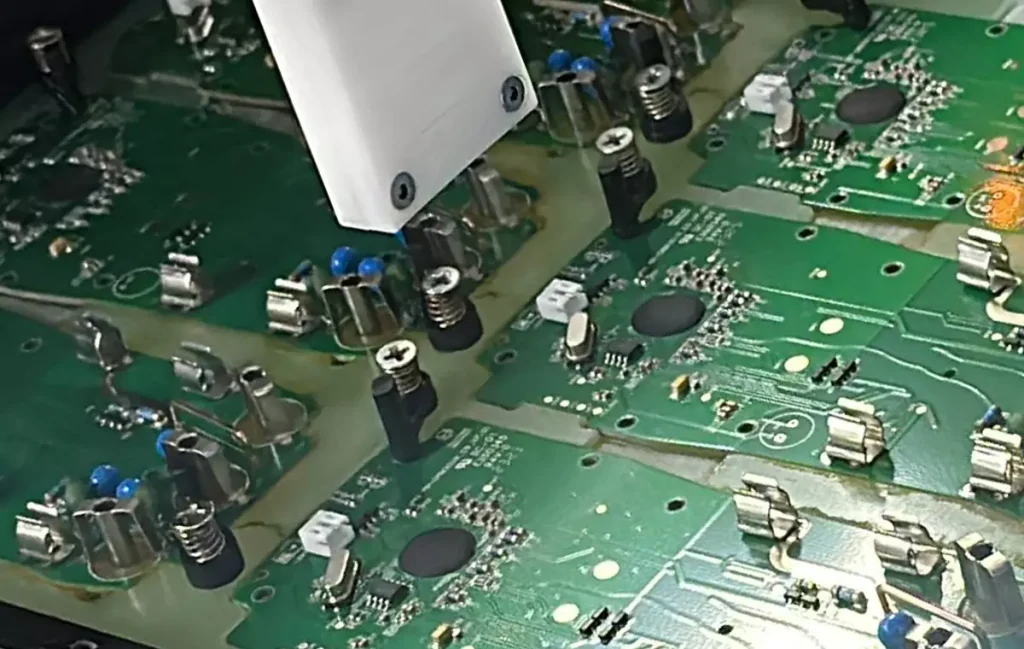
The quality inspection of vehicle electronic circuit boards is a complex process involving multiple disciplines such as materials science, electrical engineering, and environmental science. Only by strictly adhering to the above industry standards and implementing meticulous quality control in each production process can the final product operate stably and safely in harsh automotive electronic environments. With the rapid development of autonomous driving and electric vehicle technology, the quality requirements for PCBs will only become increasingly high. Continuous technological innovation and standard updates will be the key to future development.