Wave soldering refers to the molten brazing material, by electric pump or electromagnetic pump jet into the design requirements of the solder crest, can also be formed by injecting nitrogen into the solder pool, so that the pre-loaded components of the printed circuit board through the solder crest, in the brazing material surface to form a specific shape of the brazing material peaks, loaded with components of the PCB at a particular angle, and a certain depth of immersion through the brazing material crest to achieve the brazing process of the solder joints called Wave soldering.
Wave soldering process
- Board loading
The printed circuit board (PCB) is loaded into the carrier of the wave soldering machine to ensure that the PCB is fixed and stable for subsequent operations.
2.Apply flux
Before soldering, it is necessary to apply a layer of flux (rosin or other flux) on the PCB substrate to prevent bridging or false soldering during the soldering process.
3.Preheating
Heat the PCB to a certain temperature to evaporate the moisture on the flux and component pins, and also to reduce the temperature difference between the PCB and components to prevent stress damage.
4.Soldering
Feed the PCB into the soldering area of the wave soldering machine, where molten solder from the solder bath is pumped onto the PCB to fill the gap between the component pins and the pads on the board, connecting the component to the board.
- Hot Air Knife
After soldering, a hot air knife is used to blow away the excess solder to make the solder joints smoother and more uniform.
6.Cooling
Cool the soldered PCB board to room temperature to solidify the solder joints and ensure their strength and stability.
7.Unloading
Remove the soldered PCB from the carrier of the wave soldering machine for subsequent inspection and testing.
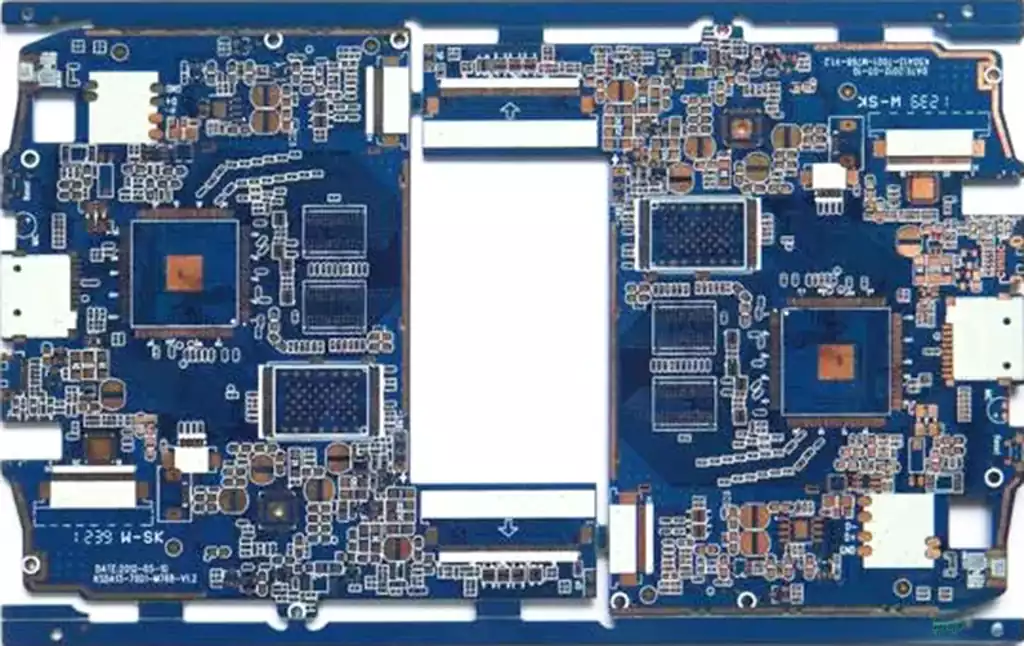
Process advantages:
- Save labor and materials, improve productivity and reduce production costs;
- The circuit board contact with high-temperature soldering work is short, can reduce the warping and deformation of the circuit office.
- Eliminate the interference and influence of human factors on product quality, improve the quality and reliability of the solder joints;
- Wave soldering machine solder abundant activities, conducive to progress in the quality of solder joints
- Improvement of the operating environment and the physical and mental health of the operator due to the adoption of a good exhaust system;
- The floating layer of antioxidant meter on the exterior of molten solder isolates the air, as long as the solder wave is exposed to the air, cutting down the time of oxidization, which can cut down the waste of solder brought about by oxidized slag.
- Good consistency, to ensure the consistency of the quality of product installation and process standardization, standardization;
- Can complete the work that can not be done by manual operation.
Applications.
Wave soldering is widely used in the production of electronic products, such as cell phones, computers, home appliances and so on. In these products, wave soldering technology can realize fast and efficient welding of a large number of components, which provides a strong guarantee for the stability and reliability of the products.
Wave soldering equipment mainly consists of welding host, control system, transportation system, flux spraying system, cooling system and other parts. Among them, the welding host is the core of the wave soldering equipment, responsible for realizing the wave formation of molten solder and the welding of components. The control system, on the other hand, is responsible for the overall operation of the equipment and parameter settings to ensure the stability and reliability of the welding process.
When operating this equipment, the following points need to be noted:
- Selection and preheating of solder: Select the appropriate solder and preheat it according to the melting point and characteristics of the solder to ensure that the solder can flow smoothly and form a stable wave in the soldering process.
- The use of flux: flux can improve the quality of welding and reduce welding defects. In the use of flux, need to pay attention to the spray volume, spray time and spray position and other parameters of the settings to ensure that the flux can give full play to its role.
- Pre-treatment of components: Before welding, components need to be cleaned and pre-treated to remove oil, oxides and other impurities on the surface of the components to ensure the quality of welding.
- Welding speed and temperature control: welding speed and temperature are important factors affecting welding quality. In actual operation, according to the type of components and welding requirements, need to reasonably adjust the welding speed and temperature to ensure the stability of the welding process and welding quality.
As an important technology in the electronics manufacturing industry, wave soldering provides a strong guarantee for the production of electronic products with its efficient, stable and reliable soldering process. Through precise process control, it not only improves production efficiency and reduces production costs, but also ensures the high quality of the welded joints and product reliability.