What is a protoboard?A protoboard, also known as a ProtoType board, is essentially an early sample of a product that is designed to test a design idea and see if it works. While most prototypes are made just to test basic user functionality, PCB prototypes need to be functional in some way, as they are made to test the overall functionality of the design.
The use of protoboard is very important at the beginning of the programme design, you are investing in the purchase of a board, but are able to determine if the device meets the needs of your product design and to what extent it can be squeezed.
Why use a protoboard?
When developing a new PCB-based design, you may go through several design revisions. In order to complete production in a timely manner, you need to test the new design quickly, as a lengthy design process can result in lost revenue. Our prototyping service is not only fast, but we can test designs before full production, minimising project waste and maximising your return on investment.
The cost of standard production batches can quickly escalate. The sooner you identify design flaws or inefficiencies in your PCB design, the less it will cost to fix them. If you don’t use prototype boards for testing, you may run into problems at some point late in production, after you’ve already invested heavily in producing standard PCBs. In addition, our prototyping service is also suitable for small production runs, with a minimum of just five boards.
Engineers also often use protoboard to test the functionality of single PCBs in more complex products. Before adding the next level of functionality, they order prototypes that implement the most basic functions. If each function is not tested individually, performance problems may be encountered in subsequent processes, and it can be difficult to determine which board is causing the problem. By prototyping each function step-by-step, significant time and resources can be saved.
While the manufacturing tolerances of protoboard may not be as tight as those of standard production batches, they still accurately reflect the way the final PCB solution will work. We can produce prototypes that look and function almost identically to the final product, but with lower manufacturing tolerances and possibly without some of the more advanced features. However, we take great care to ensure that the prototype board is an accurate representation of how a standard production PCB would work.
Once you have fully validated the design with the protoboard, you can move on to a standard production batch that has tighter manufacturing tolerances, can handle more features, and can accept larger order quantities. As part of our standard production service, we offer a manufacturing design analysis to help identify any issues that may affect production. If any potential problems are identified, we will contact you to work together to develop the necessary solutions.
If you are developing a new product or undertaking a redesign, then our protoboard production service may be of assistance to you. It can help you to identify any problems that may exist in your design or changes that need to be made before investing a lot of time and money. This will improve the economics of your project, resulting in a higher quality end product and contributing to its overall success.
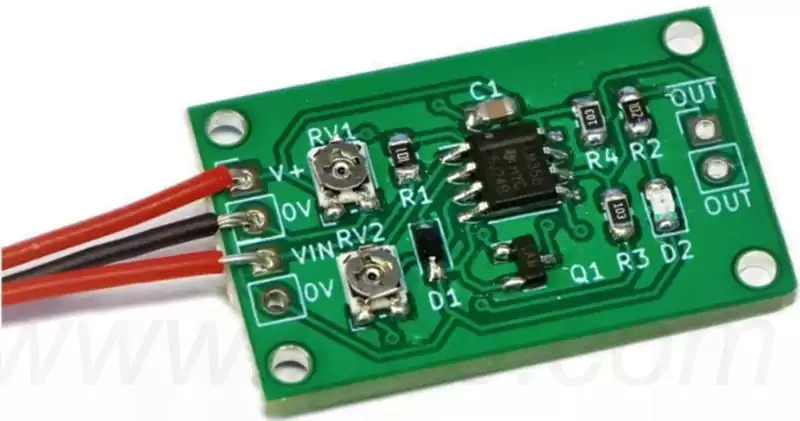
Benefits of protoboard
Speed up the process and reduce costs
During the PCB design process, engineers often need to go through several iterations to create the final product, which results in a long timeline. The advent of protoboard, however, has effectively accelerated the overall process of design and manufacturing in the following ways:
1) Comprehensive testing:
Protoboard for PCB design engineers to provide a fast, accurate means of testing to help them find problems in the design in a timely manner. Without this link, the discovery of design defects may take more time, and once it can not be delivered on time, it may also cause customer dissatisfaction, which in turn leads to loss of revenue.
2) Demonstrate in advance to facilitate communication:
Customers usually want to see the physical product at multiple stages of the production process. Providing protoboard as a reference helps to better communicate design concepts, while also minimising communication barriers with customers and the time it takes for customers to request redesigns due to lack of understanding or dissatisfaction.
3) Reduce rework and improve efficiency:
Through protoboard testing, the board can be fully viewed and tested before formally put into production, thus effectively reducing rework. Once the defective product into the production stage, the later will need to spend more time and cost to correct. The emergence of protoboard, it greatly reduces this risk.
To promote manufacturing and production smoother
When choosing a third-party PCB prototyping service, it is important to find a partner with smooth communication. In the design process, there are several factors that can lead to errors, including:
1) Version confusion and lack of communication
During the design process, PCB versions can accumulate and overlap due to changes in the customer or design team. Without proper documentation, it is difficult to distinguish which is the best version. In addition, the best design solution may sometimes be ignored in order to meet customer requirements.
2) Design field limitations
A designer may be better at designing a particular type of PCB, but may have less experience in other areas, which may introduce some minor problems in the design.
3) Limitations of Design Rule Checking (DRC)
Although the DRC tool is very helpful in finding obvious problems in a design, it has its limitations and cannot cover all possible problems.
4) Prototype assistance to reduce communication costs and rework
Customers often want to see the physical product at multiple stages in the production process. Providing PCB prototypes as an aid can better communicate design concepts and reduce communication barriers with customers, as well as the time it takes for customers to request redesigns due to lack of understanding or dissatisfaction. PCB prototyping also minimises rework by allowing the board to be fully viewed and tested before going into production. Once the defective product into the production stage, the later will need to spend more time and cost to correct, while the prototyping effectively avoid this risk.
In advance to verify and test product features
With accurate and reliable protoboard, it is easier to deal with various design challenges in the development process. High-quality prototypes can truly reflect the function of the final product, providing engineers with valuable testing and verification opportunities, specifically in the following areas:
(1) PCB design verification
Through prototyping, engineers can find and correct defects in the design in a timely manner in the early stages of development. The more accurate the protoboard, the more accurate the identification of defects, so that the design cost can be controlled at the lowest level, and effectively shorten the project cycle.
2) Functionality testing
Some designs may work in theory, but problems may occur in practice. Accurate PCB prototypes can help engineers assess the difference between theoretical and actual values to ensure the feasibility of the design.
Using protoboard, engineers can conduct a comprehensive check and evaluation of the product’s various functions.
3) Environmental conditions test
Many products need to be used in specific environmental conditions, so PCB products must undergo rigorous testing to ensure that they can operate properly under these conditions. For example, protoboard usually undergo temperature change tests, power fluctuation tests, shock resistance tests, etc. to verify their stability and reliability under various environmental conditions.
4) Final Product Design and Optimisation
Protoboard also help engineers determine if adjustments need to be made to the final PCB design to accommodate planned product or packaging requirements. Accurate protoboard can greatly simplify the rest of the development process, and for engineers to successfully put into production plans to be fully prepared.
Independent testing of single components
Engineers often use protoboard testing, the most critical is the test of single components and functions. Prototype PCB testing focuses on each single function integrated in the PCB to ensure that they can work as expected. This type of testing serves a variety of purposes, including:
1) Verifying design theory
Simple PCB prototypes are used in the proof-of-concept stage, allowing engineers to physically view and test the design theory before moving further into the design process. In this way, engineers can determine if the design is valid and, if not, they can quickly pinpoint the problem.
2) Disassembling Complex Designs
Often, simple protoboards are used to disassemble the basic components of the final PCB, ensuring that the design successfully implements a basic function before moving on to the next stage. This step-by-step approach to testing helps to identify design problems in a modular way, enabling faster and more accurate adjustments to be made. By testing each function individually, engineers can do so efficiently and effectively.
Cutting Costs
Standard PCB production running costs are quite high, and prototyping plays a vital role in reducing production costs. It helps engineers to solve and avoid the following potential problems in a timely manner:
(1) early identification of design flaws
Engineers who recognise design flaws early can fix them quickly and at low cost. Conversely, if the problem is delayed until production is in full swing, the cost of fixing the problem will escalate and may even destroy the overall budget.
With high-quality PCB prototyping services, engineers can quickly and accurately identify and resolve design flaws, which can significantly reduce costs in the long run.
2) Clear product adjustment needs
In some cases, adjustments to the PCB may lead to deviations in shape or material from the original plan, which in turn affects the overall product specifications and manufacturing requirements.
Through protoboard, engineers can determine whether the need to adjust the product early, so as to optimise the planning process, and reduce the product and its related packaging redesign costs.
Protoboard in the paste before the following preparations must be made
1.According to the PCB product process documentation of the mounting schedule to receive materials (components, PCB boards, solder paste) and check one by one.
2.Has opened the packaging of PCB circuit boards, according to the length of the opening time and whether the moisture or pollution, cleaning and baking treatment.
3.For the moisture-proof requirements of the components, regularly check whether there is moisture, if found to have moisture components, moisture components to be dealt with moisture treatment (material baking)
4.Check the humidity display card attached to the package after opening, if the indicated temperature > 10% (read at 23 ℃ ± 5 ℃), indicating that the components have been affected by moisture, the need for components to remove moisture treatment before mounting.
Each PCB production equipment status check. The following must be checked before switching on the machine to ensure safe operation.
1.Check whether the air pressure of the compressed air source meets the requirements of the equipment, it should be more than 6kg/cm2.
2.Check and make sure that there are no obstacles on the guide rail, within the range of movement of the mounting head, around the automatic replacement nozzle bank, or on the pallet rack.
According to the specifications and type of components to select the appropriate feeder and correctly install the components.
Protoboard plays a vital role in the development of electronic products. Not only does it help engineers speed up the design process and reduce costs, but it also allows for early verification of product functionality, independent testing of single components, and effective circumvention of potential design flaws and the need for product adjustments. For any team working on electronic product development, choosing a high quality PCB prototyping service is a smart way to improve product quality, increase profitability and drive project success.