Cold welding is a special method in welding technology, which is widely used in metal processing, electronic manufacturing and the production of high-precision equipment. What is cold welding in the electronies industy ? Cold welding is significantly different from traditional hot welding.
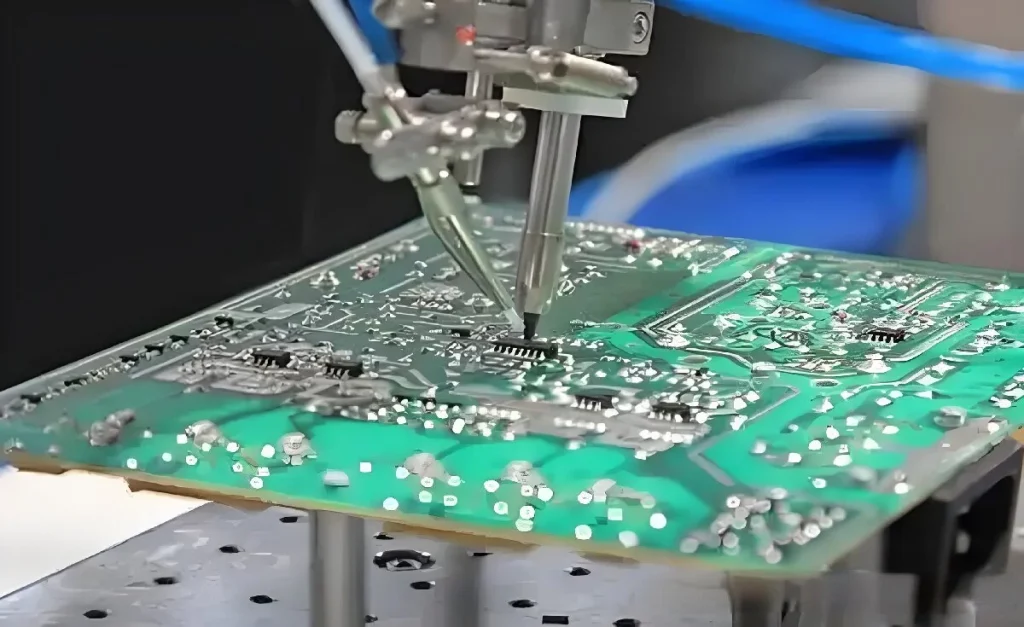
The main difference is that cold welding does not rely on high temperature to melt metal, but uses physical action to make the metal surface in close contact, thereby achieving the combination of metals. Because cold welding has many unique advantages and application value, it has gradually become an important welding method in the industrial field.
Definition and working principle of cold welding
Cold welding usually refers to the process of connecting metal materials without melting under normal temperature conditions by high pressure or other mechanical means. The key is that the applied external force increases the interaction force between the surface atoms of the two metals, and finally forms a connection between the metals. The cold welding process does not involve any additional welding materials and does not generate high temperatures, so it is regarded as a very environmentally friendly and efficient welding method.
During the cold welding process, the structure of the metal surface changes, the attraction between atoms increases, and the contact area between the metal molecules undergoes plastic deformation, forming a solid connection point. In this way, the metal surface is compressed and in close contact, and finally the connection between the metals is achieved.
Cold welding is usually used for materials that are not suitable for heating or are easily damaged at high temperatures, such as aluminum, copper, silver, etc. In practical applications, cold welding technology occupies an important position in the field of high-precision welding, especially in the manufacture of electronic devices and precision machining.
Working principle of cold welding
The working principle of cold welding is based on the physical contact and force between atoms on the metal surface. When two metal surfaces are in contact, the molecules will attract each other. At this time, the molecular structure of the metal will undergo slight changes, resulting in a strong attraction. Through the action of external forces, the metal surface is compressed and deformed at the contact point, and the attraction between atoms is further strengthened, and finally the fusion between the metals is achieved.
This process does not use an external heat source, and the metal does not melt. Instead, the metal surface is compressed by external force, making the metal surface contact more closely. In this process, due to the lack of high temperature interference, the physical properties and structure of the metal are almost unaffected. Therefore, cold welding technology is usually used for precision products and equipment that are sensitive to heat.
Surface pretreatment: To ensure the cold welding effect, the metal surface needs to be thoroughly cleaned to remove impurities such as oxides and oil stains. The smoother the surface, the better the cold welding effect. Common cleaning methods include chemical cleaning, sandblasting, etc.
Pressure: The surfaces of two metal materials are brought into close contact and sufficient pressure is applied to cause plastic deformation of the metal surface. The application of external force causes the atoms in the contact area of the metal surface to move closer, increasing the attraction between atoms, thereby promoting the formation of the connection.
Metal connection: Under the action of pressure, the distance between atoms on the metal surface is reduced, and the atoms in the contact area interact and generate metal bonds, and finally complete the connection.
Advantages of cold welding
Cold welding technology has many advantages that traditional welding methods cannot match, which makes it widely used in many industrial fields. The following are some of the main advantages of cold welding:
No need for high temperature: The biggest feature of cold welding technology is that there is no high temperature involved. Traditional welding methods often require high temperature to melt the metal, while cold welding can complete the connection at room temperature without overheating and deformation of the metal. Therefore, cold welding is suitable for many temperature-sensitive materials.
No welding material: Cold welding does not require the use of welding wire or welding rod, which reduces the consumption of welding materials. This not only reduces production costs, but also avoids the adverse effects of welding materials during welding, such as oxidation of welding materials.
Avoid thermal damage: Since there is no high-temperature heating, cold welding can effectively avoid structural damage to the metal caused by overheating. For some precision parts, hot welding often leads to a decrease in the strength and hardness of the material, while cold welding can maintain the original properties of the material.
Applicable to a variety of metals: Cold welding is suitable for a variety of metals, especially for metals such as aluminum and copper that are difficult to weld by traditional hot welding. Cold welding can achieve effective connection. This makes cold welding widely used in high-precision industries such as aerospace and electronic manufacturing.
Energy saving and environmental protection: Since cold welding does not require additional heat sources and welding materials, it has low energy consumption and does not produce harmful gases during the welding process. Therefore, it is a very environmentally friendly welding method.
Application fields of cold welding
The application of cold welding technology in many fields has been widely recognized, especially in some high-precision and demanding industrial fields. The following are several major application fields of cold welding technology:
Electronic industry: Cold welding is widely used in the manufacture of electronic components, especially when connecting microelectronic components. Cold welding can not only maintain the precision of electronic components, but also avoid damage to electronic components caused by high temperature, ensuring its stable performance.
Aerospace: Cold welding technology has important applications in the aerospace field, especially in the connection of some high-strength and high-precision parts. Since cold welding avoids the thermal damage that may be caused by high-temperature welding, it can ensure the performance and structural stability of parts in aerospace equipment.
Jewelry industry: Cold welding also has important applications in the jewelry industry, especially in the welding of precious metals such as gold and silver. Since precious metals are prone to discoloration or melting at high temperatures, cold welding can avoid the defects of high-temperature welding, so that the appearance and quality of jewelry products are better guaranteed.
Automobile manufacturing: In automobile manufacturing, the connection of many small parts requires very high precision. Cold welding can help manufacturers connect parts and avoid the impact of traditional welding methods on the shape of parts. In addition, cold welding is also commonly used for electrical connections to ensure the stable operation of automotive circuits.
Limitations and challenges of cold welding
Although cold welding technology has many advantages, it also has some limitations, which makes it unable to replace traditional hot welding methods in some cases. First, the welding strength of cold welding is generally not as high as that of traditional hot welding, especially under high-load working conditions, the stability of cold welding joints may be insufficient. Secondly, cold welding requires a high degree of finish on the metal surface. If the metal surface is not smooth enough or has oxides, the effect of cold welding will be affected. Finally, cold welding equipment requires high precision, especially in the cold welding process that requires high pressure, the stability and precision of the equipment have a direct impact on the welding quality.
Comparison between cold welding and hot welding
Cold welding and hot welding are two common welding methods, and their working principles, scope of application, advantages and disadvantages are different. Choosing cold welding or hot welding depends mainly on the specific application requirements.
Temperature requirements: cold welding does not require high temperature, while hot welding usually requires high temperature to melt the metal, which is suitable for general metal connections.
Welding materials: cold welding does not require additional welding materials, while hot welding requires the use of welding rods or welding wires, which increases costs.
Applicability: cold welding is suitable for high-precision, temperature-sensitive connections, while hot welding is suitable for larger-scale welding tasks, such as structural parts connection.
Welding strength: The welding strength of hot welding is usually higher than that of cold welding, which is suitable for occasions with large loads.
The development and future trend of cold welding technology
With the continuous progress of industrial technology, cold welding technology is also constantly developing and improving. The modern manufacturing industry has increasingly high requirements for precision processing, energy saving and environmental protection as well as material protection, which makes the application of cold welding technology continue to expand.
In the future, with the combination of nanotechnology, automated equipment and artificial intelligence, cold welding technology is expected to further improve welding precision and efficiency. For example, the use of nano-scale surface treatment technology can enable the metal surface to achieve a higher degree of finish, thereby enhancing the strength of the cold welding connection.
In addition, the introduction of intelligent welding equipment will make the cold welding process more controllable and efficient, reducing human error and improving production consistency.
In the future, cold welding technology may also have breakthrough applications in the field of biomedical engineering. For example, miniature electronic components in medical devices require highly precise connections, and cold welding technology can ensure stable connections without causing thermal damage to the components.
In addition, with the research and development of new alloy materials, cold welding technology may be expanded to more types of materials, so that its scope of application is even wider.
Summary
As an advanced welding technology, cold welding has many unique advantages, such as no heat damage, environmental protection, and no welding materials. It has been widely used in electronic manufacturing, aerospace, jewelry making and other fields, and occupies an important position in many high-precision industries. However, cold welding also has certain limitations, especially in terms of welding strength and metal surface treatment, which require more stringent control. With the continuous development of technology, cold welding is expected to play an important role in more fields and become an important supplement to traditional welding methods.