What is pcb potting? Potting is the polyurethane potting adhesive, silicone potting adhesive, epoxy resin potting adhesive with equipment or manual way into the device equipped with electronic components, lines, curing at room temperature or under the condition of heating into a thermosetting thermosetting polymer insulating material with excellent performance, so as to achieve the purpose of bonding, sealing, potting and coating protection.
The main role of potting is:
Strengthen the integrity of electronic devices, improve the resistance to external impact, vibration;
Improve the insulation between the internal components and lines, conducive to device miniaturization, lightweight;
Avoid direct exposure of components and lines, and improve the waterproof, dustproof and moistureproof performance of the device;
Heat transfer and thermal conductivity.
There are three main types of PCB board potting adhesive, which are polyurethane potting adhesive, epoxy resin potting adhesive, and silicone potting adhesive. In the preparation of PCB substrate process how to choose potting compound?
1.polyurethane potting compound
Temperature requirements, not more than 100 degrees Celsius, after the encapsulation of more vapor bubbles, encapsulation conditions in a vacuum, adhesion between epoxy and silicone.
Advantages: excellent low-temperature, shockproof performance is among the three *.
Disadvantages: high temperature resistance is poor, the surface of the cured colloid is not smooth and poor toughness, aging resistance and UV resistance are weak, the colloid is easy to discolor.
Scope of application: suitable for potting indoor circuit board components with low heat generation.
2.Epoxy resin potting compound
Advantages: excellent high temperature resistance and electrical insulation, easy to operate, very stable before and after curing, excellent adhesion to a variety of metal substrates and porous substrates.
Disadvantages: weak resistance to hot and cold changes, easy to produce cracks after the impact of heat and cold, resulting in water vapor from the cracks to penetrate into the electronic components, moisture-proof ability is poor. After curing, the hardness of the gel is high and brittle, easy to strain the electronic components.
Scope of application: suitable for potting at room temperature and no special requirements for environmental mechanical properties of electronic components.
3.Silicone potting compound
Advantages: strong anti-aging ability, good weather resistance, excellent impact resistance.
Excellent resistance to hot and cold changes, can be used in a wide range of operating temperatures, can be used in -60 ℃ ~ 200 ℃ temperature range to maintain the elasticity of the non-cracking.
Excellent electrical properties and insulation ability, potting effectively improve the insulation between the internal components and lines, improve the stability of electronic components.
No corrosion of electronic components and no by-products in the curing reaction.
With excellent repair ability, can be quickly and easily after the sealing of the components out of the repair and replacement.
Excellent thermal conductivity and flame retardant ability, effectively improve the heat dissipation ability and safety factor of electronic components.
Low viscosity, good fluidity, able to penetrate into the small gaps and components underneath.
Room temperature curing or heating curing, good self-foaming, more convenient to use.
Curing shrinkage is small, with excellent waterproof performance and shock resistance.
Disadvantages: high price, poor adhesion.
Scope of application: suitable for potting all kinds of electronic components working in harsh environments.
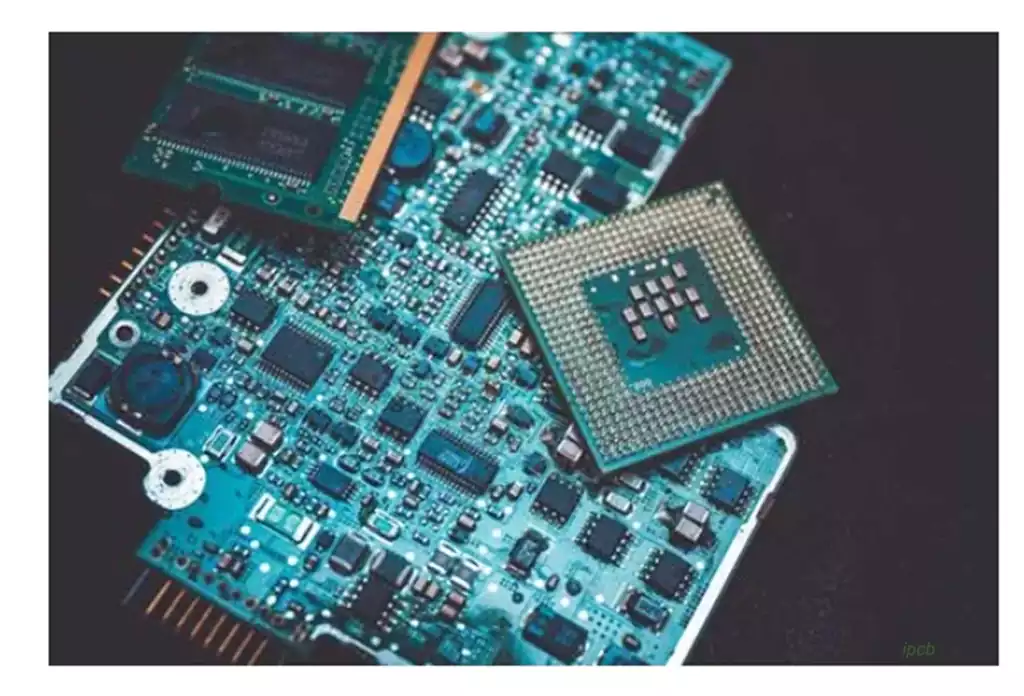
Potting process
Potting is a liquid compound that is mechanically or manually potted into the device with electronic components or lines, and cured into a thermosetting polymer insulating material with excellent performance at room temperature or under heating conditions. Can strengthen the integrity of electronic components, improve the resistance to external impact, vibration; improve the insulation between the internal components, lines, is conducive to the miniaturization of components, lightweight; to avoid direct exposure of components and lines, to improve the waterproofing of components, moisture-proof performance, improve stability.
Nowadays, the common potting methods are mainly manual vacuum potting and mechanical vacuum potting two ways, and mechanical vacuum potting can be divided into A, B components first mixed defoaming after potting and first separate defoaming after mixed potting two cases. In contrast, mechanical vacuum potting equipment investment, maintenance costs are high, but the consistency and reliability of the product is significantly better than the manual vacuum potting process.
Potting product quality, mainly with product design, component selection, assembly and the use of potting materials are closely related to the potting process is not to be ignored. Epoxy potting has normal and vacuum two kinds of potting process.
Epoxy resin. Amine room temperature curing potting material, generally used for low-voltage electrical appliances, mostly using normal potting.
Epoxy resin. Acid anhydride heating curing potting material, generally used for high-voltage electronic devices potting, more vacuum potting process.
At present, there are common manual vacuum potting and mechanical vacuum potting two ways, and mechanical vacuum potting can be divided into A, B components first mixed defoaming after potting and first separate defoaming after mixed potting two cases. There are three operation methods:
The first: single-component pcb potting adhesive, direct use, can also be directly infused;
The second type: two-component condensed pcb potting adhesive, curing agent 2% -3% or other ratios, mixing – vacuum defoaming – potting;
The third type: add molding electronic potting compound, curing agent 1:1, 10:1;
The pcb potting can better resist the influence of the external environment, such as dust, moisture, vibration, etc., so as to improve the stability and reliability of the equipment. As an important electronic manufacturing process, circuit board potting plays a key role in improving the stability and reliability of equipment