I.Overview of pcba testing standards
Visual inspection: through the magnifying glass and microscope and other tools on the circuit board appearance check to ensure that there are no welding errors, component damage and other issues.
Functional testing: the use of special test equipment to test the functions of the circuit board to ensure that all functions work properly.
Soldering quality: Check the quality of the soldering points, including whether the soldering is even, whether the weld is solid, and make the necessary repairs.
Preparation: Prepare the equipment, tools and documents required for the inspection.
Appearance Inspection: Checks the appearance of the board to make sure it is in good condition and that there is no damage or contamination.
Soldering Inspection: Use a microscope to check the quality of solder joints and connections.
Functionality Test: Use test equipment to test the board’s functionality.
Documentation of results: Documentation of inspection results, including problem descriptions and solutions.
Summarize and feedback: Summarize the problems and experiences in the inspection process, and give feedback for improvement.
PCBA test standard is the key to ensure the quality of cell phone circuit board assembly, including the installation of each component, welding quality, electrical performance and other aspects of the inspection and verification.
What is Pcba?
PCBA’s full English name is Printed Circuit Board Assembly, PCBA for the domestic abbreviation, can be interpreted as an empty circuit board by pasting on the patch components of the entire process or after the DIP plug-in of the entire process, this entire process is called PCBA, do you know? In fact, PCBA is only the domestic writing, foreign standard writing is PCB ‘A, but with the deepening of domestic and foreign trade, by the domestic influence of more and more foreign friends have begun to learn us to PCB ‘A called PCBA. It is the “heart” and “brain” of electronic products, is an important term in the electronics manufacturing industry.
Simply put, PCBA is a piece of light PCB (Printed Circuit Board) after a process, transformed into a board filled with electronic components. This process includes the procurement of components, PCB production, SMT chip processing, DIP plug-in processing, PCBA testing and so on. After completing all these steps, the PCB board becomes a PCBA board, which can perform all kinds of amazing functions of electronic products.
PCBA can be said to be the most important part of all electronic components, small to our lives used in cell phones, computers, electrical appliances, 3c digital, such as desktop computers, the main chassis composed of a monitor, mouse, keyboard, U disk and so on products, as large as the network communications, automotive electronics, military research and other industries can not do without the use of PCBA, PCBA is similar to the neural network with the human brain, is the core of all electronic products. Is the core of all electronic products. It is responsible for receiving our operating instructions, and then computing processing, and then output the corresponding results, so that we can enjoy the convenience and fun of technology.
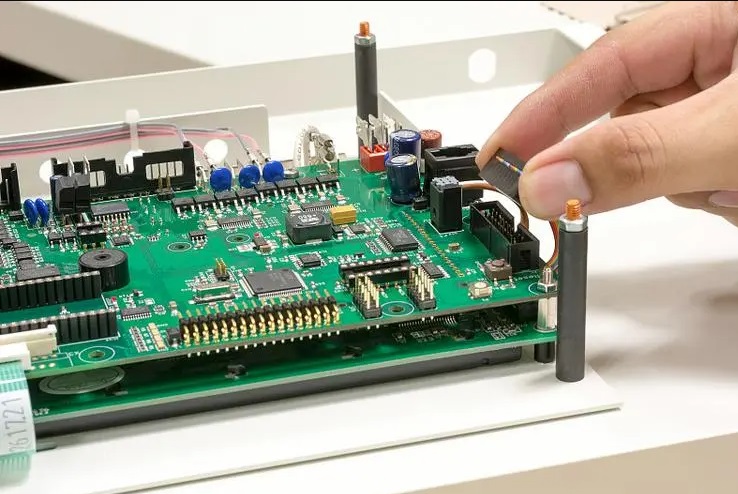
What is pcba test?
PCBA process is complex, in the production process, may be due to equipment or improper operation of a variety of problems, can not guarantee that the products produced are qualified, so it is necessary to carry out PCBA testing to ensure that each product will not appear quality problems. PCBA test mainly includes: ICT test, FCT test, aging test, fatigue test, test in harsh environments in these five forms.
1, ICT test: ICT test, also known as online tester, ICT test is mainly through the test probe contact PCB test point to detect the line open, short circuit and PCBA board components on the welding situation. ICT test has a simple operation, high accuracy. Some low-end PCBA boards can be specialized in ICT test fixtures, which can effectively reduce the cost of testing. Includes circuit on and off, voltage and current values and fluctuation curves, amplitude, noise and so on.
2, FCT test: FCT test can also be referred to as PCBA function test, the test target can provide a simulated operating environment (excitation and load), so that it works in a variety of states, in order to measure the output parameters in line with the requirements. FCT test refers to the internal function of the target test, the test mainly includes voltage, current, power, power factor, frequency, duty cycle, brightness and color, character recognition, sound recognition, sound recognition, and so on. Character recognition, sound recognition, temperature measurement, pressure measurement, motion control, FLASH and EEPROM burning, etc., simulation test of the function of the entire PCBA board, to find out the problems in the hardware and software, and equipped with the necessary production fixtures and test racks.
3, fatigue test: PCBA board sampling, and function of high-frequency, long-time operation, observe whether the failure, to determine the probability of failure of the test, so as to provide feedback on the working performance of the PCBA board within the electronic product.
4, test in harsh environments: PCBA board exposed to extreme values of temperature, humidity, drop, splash, vibration, to obtain a random sample of the test results, so as to infer the reliability of the entire PCBA board batch of products.
5, aging test: the PCBA board and electronic products for a long time to power, keep it working and observe whether there is any failure failure, simulate the user’s operation, after the aging test of electronic products before the batch factory sales.
IV. Cell phone pcba test process
With the improvement of people’s living standards, cell phones have become one of the most commonly used electronic devices. However, this small device behind the cell phone hides a lot of complex technology, need to carry out strict testing process to ensure its quality and performance.
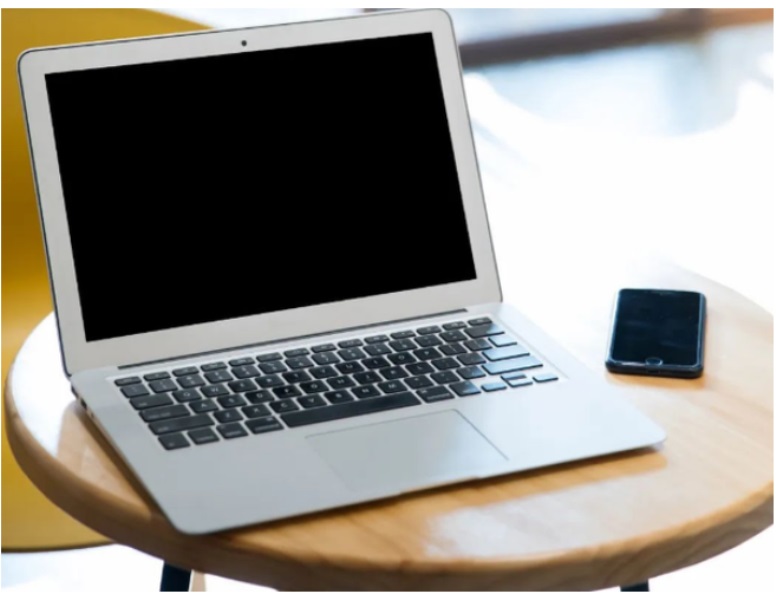
1.Raw material testing
First of all, the raw materials of the cell phone PCBA need to be tested. This includes testing of components such as batteries, screens, sound modules, touch-sensitive modules, signal receivers, etc. to ensure that they all meet production requirements. For example, the battery needs to be tested for its capacity and charge/discharge performance, and the screen needs to be tested for its color accuracy and sensitivity.
2.Assembly Testing
During the assembly process, the quality of each step of the assembly process needs to be tested to ensure that each component can work properly.
3.Function Test
After assembly, the phone needs to be functionally tested. This includes testing the phone, network, Wi-Fi, Bluetooth, GPS, camera and other functions. Also, the phone’s music, video, games and other applications need to be tested to ensure that they work properly in a variety of different situations.
4.Quality Test
Quality testing is the last and most important step in PCBA testing for cell phones. This test requires long time stable operation test for the cell phone, as well as various emergency situations, such as high and low temperature environments, vibration, drop and so on.
Cell phone PCBA test process is a very complex and strict process, need to put all aspects of strict control, and the test time is also very long, from raw material testing to quality testing, always maintain a high degree of professionalism to ensure the quality and performance of the phone, to provide users with a more stable experience.
V. What is the content of cell phone pcba test?
First, functional testing, also known as MMI testing, is an important part of cell phone PCBA testing. This step through the use of specific test tools and equipment, such as wireless routers, Bluetooth sticks, GPS signal amplifiers and DC power supply, to test the main board of the phone’s various human-computer interaction function is normal. For example, the wireless router is used to detect whether the phone can connect to WIFI and normal network use; the Bluetooth stick detects whether the phone can connect to Bluetooth and share file information; the GPS signal amplifier helps the phone to quickly detect GPS and positioning; and the DC power supply provides a stable voltage for the mainboard of the cell phone to power on and work. In addition, there are special MMI fixtures for external devices such as screens, antennas, microphones, speakers, cameras, etc., all of which are made on the fixtures, which are connected to the main board of the cell phone and then turned on to simulate human-computer interaction testing.
Next is the appearance check, this step uses a magnifying glass to check whether the motherboard components are broken, deformed, dirty, scratched, false solder, tin, shift, floating high, bumping parts, side stand and other appearance problems. The use of a magnifying glass is essential because the main board of the cell phone is a high precision component that needs to be magnified for inspection.
After completing the function and appearance test, the cell phone PCBA enters the packaging stage, where the motherboard is put into bubble bag, knife card, then PE bag and sealed, and finally put into the carton. This step ensures product protection and safe transportation.
Before the products leave the factory, there will also be QA sampling, quality personnel to test the products to be extracted a certain percentage of functional tests and appearance checks, as well as the model, software, quantity and order requirements are consistent. This step ensures the quality of the product and meets customer requirements.
Finally, warehousing stage, warehousing personnel according to the order information to check the number of product models, after confirming that there is no error, fill out the warehousing list into the warehouse. The warehouse manager receives the products and prepares them for shipment.
The whole testing process also involves some important principles and precautions, such as all PCBA finished product operators must be equipped with grounding wristbands, inspection of PCBA boards must use a special microscope, the room temperature is maintained at 25 ± 5 ℃, the inspection of the light source to reach more than 500Lux and so on. In addition, the appearance and performance sampling are carried out in accordance with GB2828-2003 standards to ensure the quality and safety of the products.
IV . The main reasons for pcba testing:
- Functional verification: PCBA testing verifies that each component on the board is working properly. This includes checking the correct functioning of components such as resistors, capacitors, transistors, integrated circuits etc. Through testing, potential component failures or contact problems can be detected to ensure that the electronic product is functioning properly as intended.
- Fault Detection: PCBA testing can help detect and diagnose any faults or defects on a circuit board. This can include problems such as short circuits, broken circuits, cold soldering, poor soldering, improper component mounting, and more. By detecting and repairing these problems early, it can reduce problems in subsequent production stages and maintenance stages, and improve product quality and reliability.
- Consistency and quality control: PCBA testing can ensure that mass-produced boards have a consistent level of quality. By testing during the production process, variations or inconsistencies in the manufacturing process can be captured, which can help improve productivity and reduce scrap rates.
- Troubleshooting: If the final assembled electronic product fails, PCBA test data can be used to quickly locate and troubleshoot the problem. This helps to improve the efficiency of after-sales service and reduce repair time and costs.
- Compliance with standards and specifications: many industries and markets have specific quality standards and specifications requirements, electronic products must meet these requirements to be put on the market. pcba testing can help to verify that the product is in line with these standards, to ensure that the product is legally marketed and sold.
The benefits brought by the cell phone pcba test mainly include improving the product qualification rate, enhancing user experience, and guaranteeing product quality and reliability.
Improve the product qualification rate: through pcba testing, can effectively improve the product qualification rate, reduce the product rework rate. This is because pcba testing is an important part of the whole pcba process. Through basic testing such as ICT test, FCT test, etc., as well as some tests under extreme conditions, such as fatigue test, test under harsh environment, etc., we can ensure that the quality and performance of the products meet the standards. If problems are found in the testing process, corrections and adjustments can be made in time so as to perfect the product and avoid serious problems after the product is put on the market.
Enhance user experience: pcba testing not only focuses on the functionality of the product, but also on the user experience. Through rigorous testing, to ensure the normal operation of the functions of the phone, such as communication performance, interface interaction, etc., so as to enhance the user experience. In addition, through simulated assembly testing and other means, it can detect the problems that may be encountered in the actual use of cell phones, further improving the usability of the product and user satisfaction.
Guarantee product quality and reliability: pcba testing makes electrical contact with test points on the pcba by using spring-loaded pins, injecting signals and power, measuring electrical characteristics, verifying component connections and detecting defects. This test method ensures that the cell phone circuit boards are connected correctly, thus safeguarding product quality and reliability. Techniques such as flying probe testing are also used in pcba testing, further improving the accuracy and efficiency of testing.
In summary, the benefits brought about by cell phone pcba testing are significant, not only to improve the product qualification rate and user experience, but also to ensure the quality and reliability of the product, which is of great significance to enhance the market competitiveness of cell phones and user satisfaction!