PCB cutting is a common operation in electronics manufacturing. While specialised equipment such as laser cutters and shears can provide highly accurate cuts, what to cut pcb with nipper is still a practical and cost-effective option in some cases.
Common types of nipper
Diagonal Nose nipper: Diagonal nose pliers are the most commonly used cutting tool for making precise cuts in PCBs. The angled jaws allow easy access to narrow spaces and are suitable for cutting a wide range of small components.
Scissor nipper: Scissor pliers are also an effective cutting tool, especially for cutting thicker PCBs or larger areas of sheet metal. Its wider jaws are able to exert a greater cutting force.
E-pliers: E-pliers are characterised by their thin, sharp jaws and are suitable for very small and complex PCB cutting tasks. It is able to perform delicate operations in small spaces and is suitable for repairing and cutting complex circuits.
In choosing the right what to cut pcb with nipper, there are several factors to consider:
Cutting needs
It is vital to define your cutting needs. PCBs of different thicknesses and configurations require different types of nippers. For thicker PCBs, such as multilayer boards or boards that contain a lot of copper foil, shear pliers or diagonal jaw pliers with more cutting power are a better choice. These types of pliers are designed with sturdy cutting parts that can easily handle thick materials and reduce the effort involved in cutting. On the contrary, when you need to handle thin PCB boards or perform delicate component removal, electronic pliers are especially suitable due to their high-precision design and compact size. They ensure accurate and clean cuts without affecting surrounding components.
Jaw shape and sharpness
The shape and sharpness of the jaws of a pliers directly affects the quality and efficiency of the cut. The ideal pliers should have sharp jaws, which not only reduces resistance during cutting, but also ensures a flat and precise cut. Therefore, when making your selection, be sure to check the jaws of the pliers for signs of wear or rust, which can reduce the cutting effect and may even damage the PCB board. Also, depending on the cutting requirements, choose pliers with different jaw designs, such as wavy, flat or bevelled, to suit different cutting scenarios and material characteristics of the PCB board.
Comfort and Grip
The design of the pliers’ handles should not be overlooked. A well-designed handle with a comfortable grip not only prevents slippage during use, but also reduces hand fatigue brought about by prolonged operation, thus enhancing cutting accuracy and stability. Quality handles are often made of non-slip materials such as rubber or special plastics to increase grip while ensuring a good feel. In addition, the length and shape of the handle should be ergonomic to provide optimum leverage and control during operation.
Safety
Safety is an important factor that must be considered when choosing pliers. Especially when performing frequent or intense cutting operations, choosing pliers with protective designs can significantly reduce the risk of accidents. These guards may include non-slip grips, spring release mechanisms to reduce hand pressure, and blade locking mechanisms to prevent accidental opening of the blades. These safety measures are especially important for beginners or less experienced operators, and they can go a long way towards protecting the operator from potential injury.
Electronic pliers, also known as fine shears or electronic shears, are cutting tools designed for use in electronics manufacturing. Compared to traditional shears or diagonal jaw pliers, e-pliers typically have a more compact size, finer cutting areas, and a higher degree of rigidity. These features allow electronic pliers to easily perform fine cutting tasks without damaging circuit board copper foils and components.
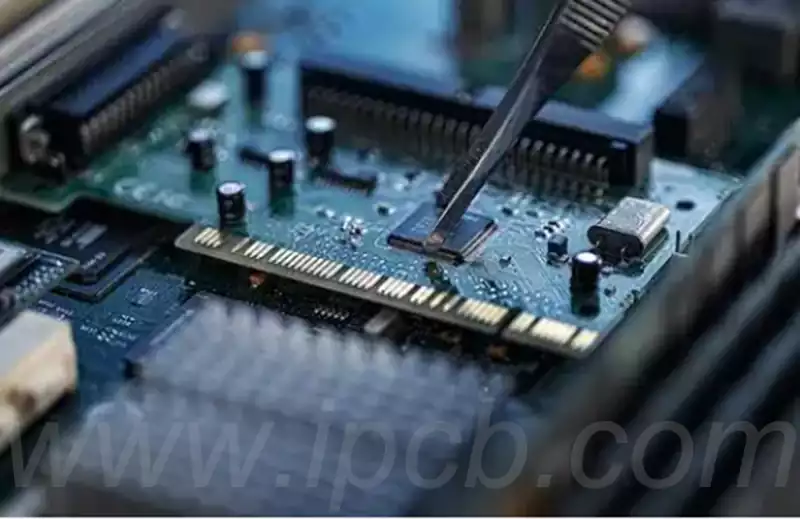
Advantages of electronic pliers for cutting circuit boards
- Fine control and operating flexibility
The electronic pliers have good operational flexibility and control, suitable for detailed cutting work. It can work in small spaces and complex circuit layouts, making it easy for operators to perform detailed cutting according to their own needs. For example, when dealing with small circuit boards or complex circuits, electronic pliers can help achieve high-precision cutting results, to ensure the integrity and normal function of the circuit components.
2.Multifunctionality
Electronic pliers can not only be used to cut circuit boards, but can also perform different functions such as pinching, bending and handling. This makes them more versatile in handling various electronic components and suitable for use in a variety of situations. For example, electronic pliers can easily perform cutting and adjusting tasks without the need for frequent tool changes, improving work efficiency.
- Easy to carry and use
Electronic pliers are small in size and lightweight in design, making them easy to carry. Whether in the laboratory, workbench or field work, electronic pliers can easily cope with. Compared to larger cutting equipment, it can operate in a limited space, suitable for mobile work and a variety of work scenarios. This portability ensures that maintenance personnel can quickly respond to urgent repair needs. - Simple and easy to use
Compared with other cutting tools, the use of electronic pliers is very simple and does not require complex training or operating instructions. All that is required is a basic understanding of operating techniques to effectively carry out cutting work. This is a great advantage for novices and non-professionals as it lowers the barrier to entry and enables more people to participate in PCB cutting tasks. - Reduced soldering stress
When using electronic pliers to cut circuit boards, the amount of force applied during cutting is relatively controllable, which means that it is possible to reduce the amount of stress placed on the PCB material. This is particularly important to maintain the structural integrity of the board, especially when the board is divided into boards to reduce soldering stress can effectively reduce the risk of subsequent welding process.
what to cut pcb with nipper process
Pre-treatment Cleaning
Before starting to cut a printed circuit board (PCB), the first step is to thoroughly clean the area to be cut. Use a clean cloth to gently brush away any debris and dust from the PCB surface to ensure a clean, dirt-free surface for the cutting process.
Accurate Measurement and Marking
With the help of precise ruler and marking tools, measure and clearly mark out the boundary and travelling line of the PCB to be cut. The marking line serves as a guide for the cut, while the boundary points help to locate the corners of the cut, both of which together outline the dimensional blueprint of the customised PCB. A hobby knife is then used to gently carve a shallow guide groove along the marked line.
Placement of protective pads
Before cutting, a layer of paper is placed underneath the PCB as a protective pad. This is to prevent unnecessary abrasion and scratches on the underside of the PCB during the cutting process and to ensure the beauty and integrity of the finished product.
Smooth and careful cutting
Using the appropriate pliers, the circuit board is cut to the required size in a smooth and even manner along the pre-set marking lines or guide slots. Due to the fragility of the PCB material, it is important to keep the cutting force gentle to avoid damage caused by excessive force.
When approaching the end of the cut, special care is needed to ensure that the end of the board is cut accurately, and to check that the edges are flat to avoid roughness or jaggedness.
Edge Polishing and Final Cleaning
If the cut edges are slightly rough, it is recommended to gently sand them with sandpaper until the edges are smooth and consistent, giving the PCB a finished texture.
Whether the edges need to be sanded or not, after the completion of the cutting process, the PCB should be fully cleaned again to remove any debris and dust that may have been generated during the cutting process, to ensure that the surface of the PCB is clean and tidy.
What to cut pcb with nipper is a technique that is both traditional and practical. By choosing the right type of pliers, mastering the correct cutting techniques, and focusing on every detail of the cutting process, we can ensure that the cutting quality and efficiency for the innovation and development of electronic products to provide a solid foundation.