Test points are an important design element in printed circuit boards and can be used as locations to probe signals or apply test stimuli during development, verification, debugging, field service and repair. They provide easy access to critical nodes in a circuit without the need to connect probes directly to components or tracks that could cause damage.
Test Point Types
Probe Accessible Test Points
Probe test points are points that are easily accessible to technicians with handheld devices or probes. These test points are easily recognisable, with common markings such as ‘GND’ (ground), ‘PWR’ (power), etc. Probe testing is primarily used to carry out surface level testing, i.e. to verify that the current supply is accurate and that the ground value is as required.
Automated Test Points
These test points are designed for automated test equipment. Automated test points on circuit boards are through-holes, through-pins, and small metal landing pads designed to accommodate the probes of an automated test system. Automated test points are capable of supporting automated test procedures using automated test probes. Broken down further, automated test points are of three types:
Bare PCB Test Points: Bare PCB tests are performed prior to component assembly to ensure good electrical connectivity throughout the board.
ICT test points on PCBAs: ICT (in-circuit testing) is designed to ensure that all components on the board are functioning correctly. A probe on the test fixture makes contact with a test point on the board to complete the test process.
Flying probe test point: Flying probe test is an automated test method for small-lot, multi-product boards to evaluate the operation of components on a PCB or PCBA board. In this test, multiple highly mobile probes are programmed to contact test points or component pins to detect faults such as opens, shorts, resistance, capacitance and component orientation.
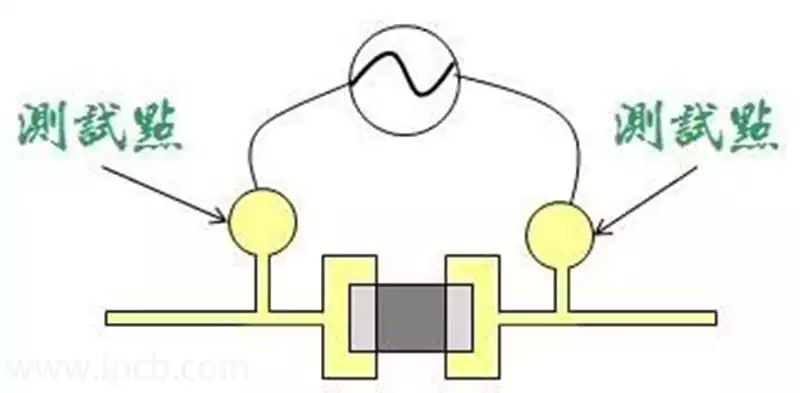
Why do PCB circuit boards need test points?
To facilitate the functional verification of the board
Ensure circuit connectivity
In the production process of PCB circuit boards, there may be circuit breaks, short circuits and other conditions. Test points create convenient conditions for circuit connectivity testing. In the case of multi-layer PCBs, for example, where the inner circuitry cannot be viewed directly with the naked eye, test points are set up at important nodes, and with the help of a multimeter or professional connectivity testing equipment, it is possible to quickly determine whether the connections between the various layers of circuits are accurate or not. Without test points, it would be extremely difficult, if not impossible, to check the connectivity of multi-layer PCBs, which could result in defective boards entering the subsequent production phase.
For complex circuit systems, such as computer motherboards, which have tens of thousands of electronic components and intricate wiring. Test points can help technicians in the production of assembly, quickly confirm that the connection between the various functional modules is in a normal state. For example, when checking the CPU power supply line, the test point can quickly determine whether the power supply can be smoothly transferred to the CPU, preventing the CPU from not functioning properly due to line failure.
Verifying Component Performance
After the electronic components have been soldered to the PCB, it is necessary to verify that they function correctly. They make it possible to measure the input and output signals of components with the help of specialised test instruments such as oscilloscopes and logic analysers. Taking the amplifier chip on the circuit board as an example, test points connected to the input and output of the amplifier chip make it possible to observe whether the output signal after amplification of the input signal by the chip achieves the desired effect. If there were no test points, it would be extremely cumbersome to reach the pins of the component to carry out signal measurements, perhaps requiring the removal of other components around the component, and possibly even causing damage to the circuit board.
In digital circuits, the functional accuracy of logic gates plays a key role. Test points make it easy for technicians to use logic analysers to monitor the input and output logic levels of logic gates to ensure that they perform logic operations as designed. For example, in the FPGA (Field Programmable Gate Array) development board, a large number of test points distributed around the FPGA chip, for developers to debug and verify the function of custom logic circuits to provide a convenient.
Improve production efficiency and quality control
Efficient Testing in Production
In the mass production process of PCB circuit boards, each board has to undergo strict quality inspection. It creates the conditions for automated test equipment to quickly inspect circuit boards. For example, at the end of an SMT (Surface Mount Technology) production line, there is usually an In-Circuit Testing (ICT) machine, which can test most of the components and circuits on the board in just a few seconds by establishing a connection to a test point on the PCB. Without test points, ICT equipment would not function properly or would have to use more complex and time-consuming testing methods, which would undoubtedly significantly reduce productivity.
For some of the circuit boards that require functional testing, such as mobile phone motherboards, the boards can be simulated during production with the help of test fixtures connected to the test points to test functions such as power-on, call, data transmission, and so on. This test point-based functional testing can quickly screen out defective products and ensure that only qualified products can move on to the next assembly process. Without test points, functional testing would be extremely complex, perhaps requiring manual inspection of components and functions one by one, leading to longer production cycles and higher costs.
Troubleshooting and Repair
When a circuit board fails after being put into use, test points point maintenance personnel in the direction of the key to troubleshooting. With the help of signal measurements on different test points, the scope of the fault can be gradually narrowed down to precisely locate the components or lines where the fault lies. For example, in a faulty TV motherboard, the repairer can measure the test points of the power supply part to determine whether the power supply link is faulty or the subsequent load circuit is faulty. If there is no test point, the maintenance personnel may only be able to carry out clueless investigation of the entire power supply circuit, which will undoubtedly consume a lot of time and energy.
In industrial control circuit boards, given the complexity and harshness of the operating environment, the board is prone to failure. Test points help maintenance personnel to quickly diagnose the problem, thereby reducing equipment downtime. For example, when the automated production line on the PLC (Programmable Logic Controller) control board failure, through the test point can quickly detect the input and output signals are normal, and then determine whether the PLC chip itself is faulty, or external connection line problems, in order to repair the fault in a timely manner, so that the production line to return to normal operation.