PCB (Printed Circuit Board) is an important platform for connecting electronic components. In the process of PCB fabrication, pcb test points are certain wiring points set on the PCB for circuit testing and debugging. Test points are very important for the operation and debugging of circuits, which improves the reliability of circuits, reduces production costs, and increases manufacturing efficiency.
PCB test points can be tested and tested by a variety of testing equipment, such as multimeters, oscilloscopes, network analyzers, etc., circuit connectivity, resistance, capacitance, power, frequency, and other aspects of the detection and testing. This can greatly improve the speed and efficiency of testing, maintenance, and debugging, and shorten the product development cycle. In the manufacturing process, the test point can be used to check the quality and reliability of the PCB and improve the shipment rate and quality of the product.
PCB test point design principles
In PCB design, the location, number and type of test points need to be carefully considered. Here are some key design principles:
Reasonable layout: Test points should be located near critical signal lines or power/ground lines for easy monitoring. Also, avoid placing test points in high-frequency signal areas to minimize interference with signal integrity.
The right number: Too many test points may introduce additional electrical performance issues, while too few test points may not fully reflect the board’s performance. Determine the appropriate number of test points based on the board’s complexity and test requirements.
Type selection: Depending on the test requirements, different types of test points can be selected, such as bed-of-pins test points, flying probe test points, and boundary-scan test points.
Consider Maintainability: When designing test points, future maintenance and troubleshooting needs should be considered. Test points that are easily accessible and recognizable can speed up the maintenance process.
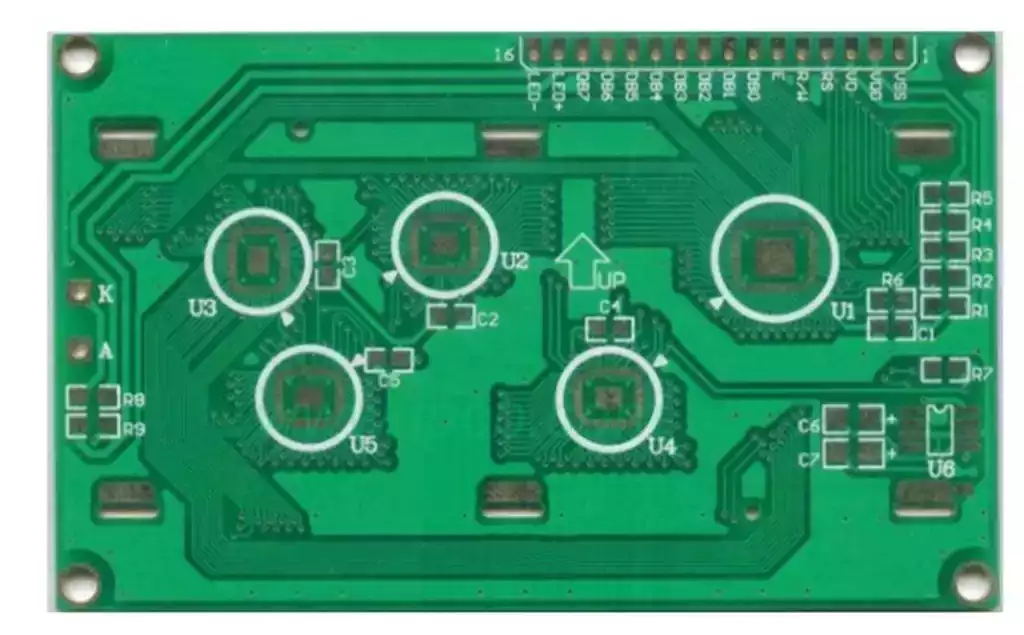
The following steps are essential when implementing circuit board testing:
Determine test requirements: Define the purpose of the test, such as functional testing, troubleshooting, or performance verification. This will help to determine the required test points and test types.
Design test point layout: According to the layout and wiring of the printed circuit board, rationalize the location of test points. At the same time, consider the need for future maintenance and place some test points in easily accessible locations.
Choose the right type of test point: Choose the right type of test point according to the test requirements. For example, bed-of-pin test points are suitable for mass production and functional testing, while flying probe test points are suitable for high-density and miniaturized boards.
Implementing Test Points: Test points are implemented as one of the processes in the PCB manufacturing process. This includes processes such as drilling, plating, and soldering. Ensure that each step meets the process requirements for good electrical performance and reliability.
Validation and Optimization: After completing the implementation of the test points, validation and optimization are necessary steps. Through functional testing, simulation analysis actual measurements, etc., to ensure that the electrical performance of the test point meets the expected requirements. If performance problems or failures are found, the test point layout can be adjusted and optimized.
PCB test points play an important role in ensuring the quality and reliability of electronic products. By following reasonable design principles and implementation methods, test points can be effectively utilized to improve productivity, reduce maintenance costs, and enhance overall product performance.