LED light pcb board is a technology that combines LED light with printed circuit board (PCB).LED pcb is a kind of electronic components based on LED, using the conductive paths and components on the PCB, to provide stable current and control signals for the LED light, so that the LED light can light up normally.
The working principle of LED light pcb board is mainly based on the LED light-emitting principle and the control principle of electronic circuit.
The core part of the LED lamp consists of a wafer composed of p-type semiconductors and n-type semiconductors, and there is a transition layer between them, called the p-n junction. When current passes through the LED light, electrons are injected from the p-type semiconductor into the n-type semiconductor and compound with holes in the n-type semiconductor to release energy. This energy is emitted in the form of light, which enables the LED lamp to emit light.
The printed circuit board is responsible for providing a stable current and control signals for the LED light. PCB is full of conductive paths and electronic components, such as resistors, capacitors, etc., which work together to ensure that the current can flow smoothly and steadily through the LED light. At the same time, the control components on the PCB can also adjust the brightness and color of the LED lights to meet different lighting needs.
Specifically, when the LED light pcb board is powered on, the current flows to the LED lamp through the conductive path on the circuit board. Inside the LED light, the current excites the electrons in the semiconductor material, causing them to jump to higher energy levels and release energy. This energy is emitted in the form of light, illuminating the surroundings. At the same time, other components on the PCB, such as resistors and capacitors, play the role of current limiting and filtering to ensure that the LED light can work stably and reliably.
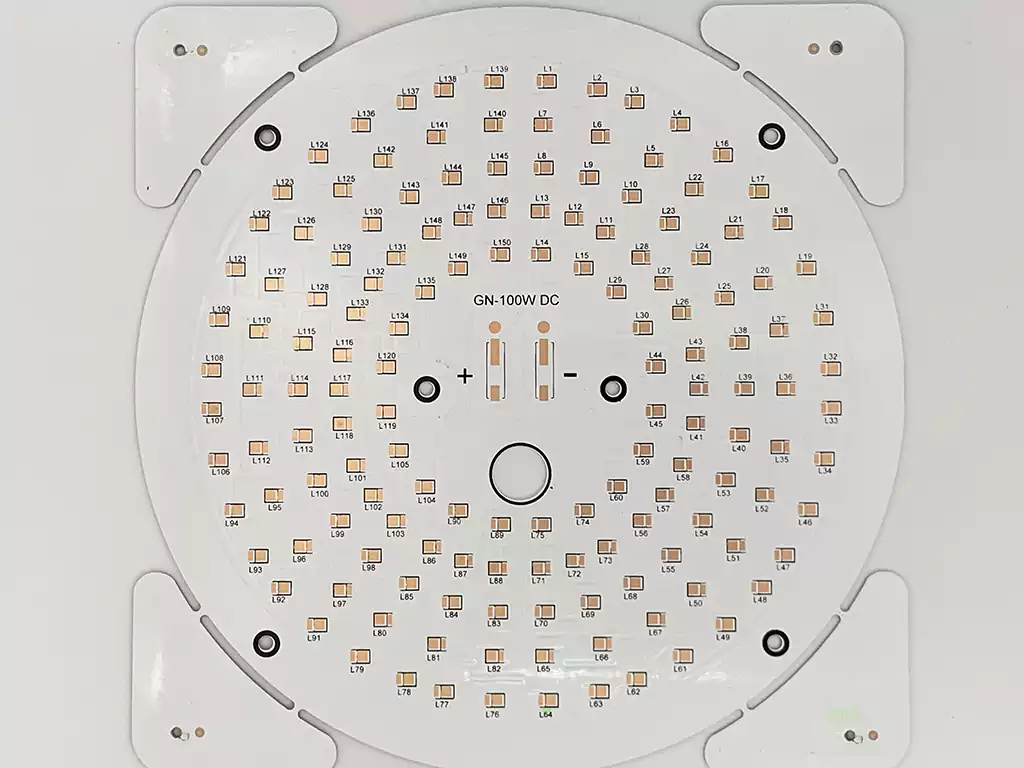
LED lamp PCB construction
LED lamp PCB (printed circuit board) is a key component of LED lamps and lanterns, and its construction directly affects the performance of LEDs and heat dissipation ability. The following are the main construction elements of LED lamp PCB:
- substrate material
The substrate material is the core part of the PCB, commonly used materials include:
Aluminum substrate: has excellent thermal conductivity, widely used in high-power LED lamps and lanterns, can effectively dissipate heat.
FR-4 material: mainly used for low-power LED applications, compared with the aluminum substrate, thermal conductivity is poor, but the cost is lower.
Metal substrates: Metal substrates other than aluminum (such as copper substrates) are also used in some special applications to provide good thermal management.
- Circuit Layout
The circuit layout of the LED light PCB is an important factor that affects its performance, including:
LED pads: The pads of each LED chip on the PCB are designed to ensure a good electrical connection. The size and spacing of the pads should be designed according to the LED specifications and operating current.
Route Paths: In order to minimize signal interference and improve energy efficiency, the PCB route design needs to be as short and straight as possible. Reasonable path design can avoid current loss and impedance matching problems.
- Thermal Management Design
Effective thermal management design is essential to maintain the performance of LED fixtures:
Heat sink: V-shaped or porous heat sink structure can accelerate heat dissipation, often used in combination with aluminum-based PCB.
Thermal conductive material: Use thermal conductive adhesive or thermal interface material between PCB and LED to enhance heat transfer capability.
- Other electronic components
LED light PCB may also integrate other electronic components, such as:
Resistors: Used to limit the current and protect the LED from overcurrent.
Capacitor: Used to smooth the supply voltage to ensure that the LED works with stable output.
- Surface treatment
Surface treatment can improve the durability and oxidation resistance of the PCB, common treatments include:
Gold or tin plating: Enhance the soldering performance and corrosion resistance, the PCB conductivity to improve.
Heat-resistant coating: Enhance the stability of PCB in high temperature environment to prevent thermal damage.
PCB LED lights offer excellent energy efficiency, low cost and maximum design flexibility, so it can be incorporated into many lighting applications:
Telecommunication: LED indicators and displays are always used in telecommunication equipment due to the surrounding machinery and they have a high heat transfer capacity. Therefore, aluminum based LED pcb plays an important role in their application.
Automotive: Aluminum pcb led is also used in cars for indicator lights, brake lights and headlights, among other applications. There are some factors that make aluminum pcb ideal in the automotive industry such as durability and competitive pricing.
Computers: LED displays and indicators are becoming increasingly popular in computer applications. Due to the heat sensitive nature of computer machinery, aluminum pcb led is an ideal solution. In addition to LED applications, aluminum pcb’s are also used in computer components such as power supply units and CPU boards because of their ability to dissipate and transfer heat.
Medical: Lighting tools used in surgical procedures and medical examinations often use high power LED lights, and these LED lights often use aluminum pcb’s, largely due to the durability and heat transfer capabilities of aluminum pcb led’s – this ensures that the medical equipment operates correctly regardless of the number of patients circulating in the infirmary. In addition to lighting tools, medical scanning technology often uses aluminum PCBs.
Advantages of LEDs
Lower power consumption: Replacing incandescent lamps with LEDs reduces power consumption by more than 80%.
Longer life: LEDs typically have a life expectancy of more than 20,000 hours and can be used 24/7 for up to 3 years, 25 times longer than incandescent lamps. This not only saves money, but also reduces the frequency of replacement.
Higher efficiency: incandescent lamps emit more heat. LED lamps can reduce this by up to 20%. This suggests that unnecessary heating can be reduced while using more powerful LED lights.
Smaller size: Due to their small size, LED lights can come in a variety of sizes and can be used in separate applications. Manufacturers can incorporate LEDs into anything, be it electronic devices or cars, and even traffic signals as well as signs on the road incorporate LED lights.
Environmentally friendly: In contrast to other bulbs, LED lights do not contain mercury. Therefore, LEDs have less impact on the environment and are easier to dispose of.
As a core component of modern lighting technology, LED light pcb board is bringing a better lighting experience to people’s life and work with its technical advantages of high efficiency, energy saving and environmental protection.