DIP packaging (Dual In-line Package), also known as dual in-line package technology, refers to the use of dual in-line form of integrated circuit chip package, the vast majority of small and medium-sized integrated circuits are used in this package form, the number of pins is generally no more than 100. DIP package CPU chip has two rows of pins, you need to be inserted into the chip socket with DIP structure. Of course, it can also be directly inserted in the same number of holes and geometric arrangement of the circuit board for welding.DIP package chip from the chip socket should be inserted and removed with special care, so as not to damage the pins.
Structure and Principle
The structure of DIP dual in-line package technology is mainly composed of a chip carrier board, pins, package shell and base plate. Among them, the chip carrier board is used to carry the chip, the pins are used to connect the chip and the external circuit, the package shell is used to protect the chip and the pins, and the base plate is used to fix the package shell to the circuit board.
In the DIP dual in-line package technology, the chip is placed in the center of the chip carrier board, the pins are soldered on both sides of the chip to form a two-row arrangement. The package housing is made of plastic or metal to protect the chip and pins from the external environment. The base plate is usually made of metal and is used to fix the package case to the circuit board.
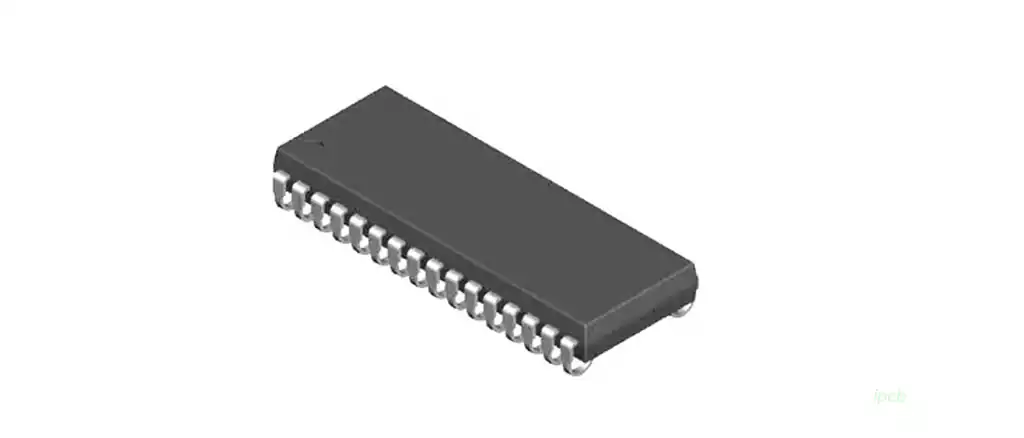
Features of dip packages.
Easy soldering and maintenance
The pin design of it optimizes the soldering process, allowing engineers to easily insert the IC into the PCB aperture for soldering operations. At the same time, its structural features also facilitate subsequent repair work, because when a failure occurs or a component needs to be replaced, it can be quickly and easily removed and replaced.
Excellent Heat Dissipation
Because it typically has a large case surface area, it exhibits superior thermal performance compared to other, more compact package forms. This feature is critical to the stability and durability of integrated circuits when operating under high loads, and effective heat dissipation extends component life.
Broad Compatibility
It exhibits excellent compatibility and work seamlessly with many types of sockets, boards and connectors. This means that engineers have more flexibility in designing circuits with components using it without having to worry about compatibility issues.
Highly efficient automated production
DIP packages are ideal for automated production lines because the pins are neatly arranged and easy to recognize. Automation equipment on the production line can easily recognize and handle pcb components, thus increasing production efficiency and reducing production costs.
Excellent Stability and Reliability
The design of it ensures a solid connection between the component and the PCB board, reducing the risk of poor connections caused by vibration or temperature changes. As a result, it is widely used in applications that require high stability and reliability, such as medical devices, aerospace and other fields.
Easy identification and categorization
The pins on DIP packages are usually arranged in a standardized spacing, and the pin numbers are clearly visible. This allows engineers to easily identify the function of each pin, facilitating proper installation and debugging of components. At the same time, the standardized pin arrangement also facilitates component sorting and inventory management.
DIP packaging technology occupies an important position in the field of IC packaging due to its unique structure and principle. Its easy soldering and repair process, excellent heat dissipation, broad compatibility, efficient automated production, excellent stability and reliability, and convenient marking and classification make this packaging technology the preferred packaging form for small and medium-sized ICs. As technology continues to advance and the application areas of integrated circuits continue to expand, DIP packaging technology, with its unique advantages, will continue to play an important role in the electronics industry.