PCB reflow plate, also known as reflow board or thermal reflow board, is an auxiliary tool in the PCB manufacturing process. Its main function is to remove the solder paste or soldering material from the surface of the PCB’s pads evenly and quickly through the process of heating and cooling during the soldering process to ensure the quality and reliability of the soldering. At the same time, the PCB reflow board can also effectively prevent defects such as bubbles and holes produced during the welding process, and improve the qualification rate of the product.
The working principle of reflow soldering
Reflow soldering mainly uses heat to make the solder paste melt, and then through the capillary action between the welding component pins and PCB pads, so that the molten solder paste flows into and fills the gap between the pins and pads, to be soldered after the solder paste cools and solidifies to form a permanent electrical connection. Reflow soldering process, solder paste from solid to liquid and then to the solid phase change process, this process requires precise control of temperature and time to ensure the quality of welding.
Reflow soldering mainly uses heat to make the solder paste melt, and then through the capillary action between the soldering component pins and PCB pads, so that the molten solder paste flows into and fills the gap between the pins and pads, to be cooled and solidified after the formation of a permanent electrical connection of the solder paste. Reflow soldering process, solder paste from solid to liquid and then to the solid phase change process, this process requires precise control of temperature and time to ensure the quality of welding.
Reflow soldering consists of four main temperature zones: a warming zone, a constant temperature zone, a soldering zone, and a cooling zone. This is also a reaction to the paste on the circuit board with good components in the reflow soldering machine in the process of change.
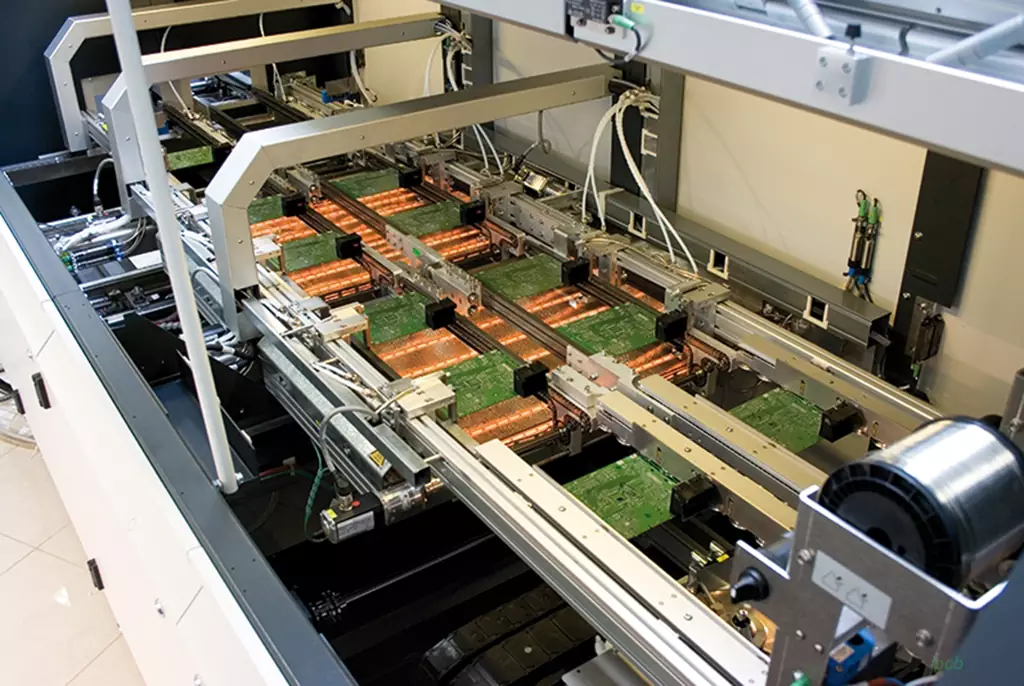
The role of the reflow soldering temperature zone
Temperature zone in the reflow soldering machine welding in the first stage, the PCB board for preheating, warming, the paste for activation, part of the solvent evaporated, and the PCB board and components of the water evaporation, eliminating the stress within the PCB board.
The role of reflow soldering insulation area
PCB board into the holding area, to reach a certain temperature, to prevent sudden entry into the welding of high-temperature areas, damage to the PCB board and components. The role of this temperature zone is also to keep the temperature of the components stable, so that the temperature of different sizes of components on the PCB board has been to reduce the temperature difference between the entire PCB board, and the flux in the solder paste evaporate cleanly to remove the oxides of the pads and component pins.
The role of reflow soldering area
PCB board into the welding area, the temperature reaches the highest, when the paste from the paste has become liquid, fully infiltrated pads, component pins, the duration of this link is relatively short, to prevent high-temperature damage to the PCB board and components.
The role of reflow cooling zone
After the paste becomes liquid, the next can be cooled, the faster the better, the slower the cooling rate is too slow, easy to produce gray roughness, generally cooled to 75 ° C on the curing, this time to achieve the welding of the PCB board.
Reflow process
- Preheating
Preheating stage is the PCB board placed in the temperature gradually rising preheating area to help the solvent in the solder paste evaporation, to avoid vapor bubbles in the high temperature stage, affecting the quality of welding. At the same time, preheating can also slow down the temperature difference between the PCB board and components, reducing thermal shock. - Melting
Melting stage is the core of the reflow soldering process, the stage in the solder paste at a specific temperature melting, so that the components and the PCB board to form a mechanical connection and electrical connection. In this stage, temperature and time need to be controlled to ensure the quality of soldering. - Equalization
Equalization stage is to make all components on the circuit board to reach the same temperature, to ensure the stability and consistency of the welding quality. In this stage, you need to control the temperature and time to ensure that all components can achieve the best welding state.
4.Cooling
Cooling stage is the PCB board from the high temperature state gradually cooled down, so that the welding material solidification, the formation of stable mechanical and electrical connections. In this stage, the cooling rate needs to be controlled to avoid thermal stress due to excessive cooling, resulting in a decline in welding quality.
- Post-treatment
Post-processing stage is the PCB board has been completed welding appearance inspection, testing and rework and other processing to ensure product quality and reliability. In this stage, the welding quality needs to be strictly inspected to find and deal with defective products in order to improve the product qualification rate.
PCB reflow plate can effectively complete the connection of solder joints between circuit boards and surface-mounted components in a very short period of time, thus enhancing the robustness of the solder joints and significantly reducing the risk of poor soldering.