Ceramic Printed Circuit Board is advanced circuit boards that offer superior performance and reliability, especially in demanding high-performance electronic applications. Unlike conventional circuit boards made from organic materials such as fiberglass or epoxy, ceramic PCB is manufactured using ceramic materials, which gives them unique properties and features. These boards are designed to excel where high thermal conductivity, excellent electrical performance at high frequencies, and robustness in harsh environments are critical.
Types of Ceramic PCB
Thick Film – These boards have conductor layers that are over 10 microns thick and are made of silver or gold. Manufacturers of thick film ceramic PCBs can place capacitors, anode conductors and semiconductors on the boards through printing and high temperature sintering. Laser trimming allows for different resistance values.
Thin Film – These boards have conductors less than 10 microns thick. Thin-film ceramic PCBs are suitable for circuits requiring high accuracy, stability and performance. Microwave circuits make extensive use of thin film ceramic PCBs.
DCB or Direct Copper Bonding – These boards utilize a special technology that bonds copper to one or both sides of a metal core under high temperature and pressure. the DCB technology offers good thermal conductivity, high mechanical strength, excellent galvanic isolation, corrosion resistance, good adhesion, high reliability, and excellent thermal cycling. DCB ceramic boards can be etched just like regular FR4 PCBs.
Multi-layer ceramic PCB
Single, double, and multilayer ceramic PCBs can be fabricated just like regular PCBs. in multilayer ceramic PCBs, the high thermal conductivity prevents hot spots from forming on the internal circuit layers and surfaces because the ceramic material helps to transfer heat evenly across the board.
Due to the mismatch between the coefficients of thermal expansion of FR-4 and copper, through-holes in multilayer FR-4 boards are susceptible to fracture during thermal cycling. Designers must take special care to prevent through-hole failure.
The coefficient of thermal expansion of ceramic circuit boards is close to the value of their conductor traces. This reduces the stress on these structures during thermal cycling. The high thermal conductivity of the circuit boards also helps to ensure that the thermal expansion is more uniform, thus preventing any through-holes from being subjected to large stresses.
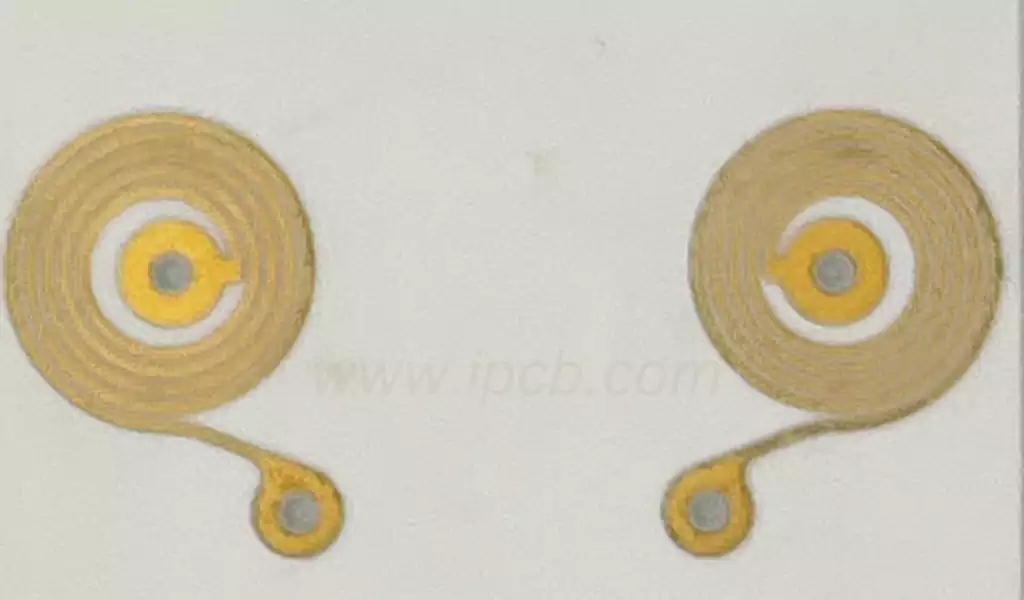
Differences between Thin Film Ceramic Substrates and Thick Film Ceramic Substrates
There are two main differences between thick film ceramic substrates and thin film ceramic substrates:
(1) the difference in film thickness
Thick film ceramic substrate film thickness is generally greater than 10μm, the film thickness of the film is less than 10μm,mostly in less than 1μm;
(2) the difference between the manufacturing process
Thick-film ceramic substrates generally use screen printing process,thin-film ceramic substrates using vacuum evaporation,magnetron sputtering and other process methods.
The basis of the ceramic circuit board lies in its ceramic substrate, ceramic substrate has many advantages that distinguish it from traditional circuit boards. One of its outstanding features is its excellent thermal conductivity, which enables it to effectively dissipate the heat generated by components. This makes ceramic PCBs the first choice for applications that generate large amounts of heat and require efficient thermal management.
The excellent electrical properties of ceramic materials, especially at high frequencies, make ceramic PCBs particularly suitable for radio frequency (RF) and microwave applications. These boards maintain signal integrity and minimize signal loss, making them indispensable in industries such as telecommunications, aerospace and satellite communications.
In addition, ceramic PCBs have impressive mechanical strength and durability, allowing them to withstand challenging mechanical stresses and vibrations. Their chemical resistance and ability to withstand harsh environments make them ideal for applications that require exposure to corrosive substances.
Ceramic printed circuit boards (ceramic PCBs) are becoming an integral part of high-performance electronic applications due to their superior performance and reliability. Whether thick film, thin film, or DCB (Direct Copper Bonding) ceramic PCBs, they offer unique advantages in their respective fields, meeting a wide range of needs from high-frequency electrical performance to resistance to harsh environments.