With the development of electric vehicles and renewable energy technologies, the battery management system (BMS) becomes the key to the safety of battery use and performance optimization. The battery pcb board, as an important part of the BMS, is responsible for monitoring and managing the charging and discharging process of the battery. In this paper, we will discuss the battery pcb board in detail
A pcb is a carrier for electronic components, providing electrical connections and support. pcb boards are usually composed of insulating and conductive materials that form complex circuit structures.
BMS is mainly composed of two parts, hardware and software, the hardware part includes the battery pcb board and the software part is responsible for data processing and management. Battery management system is a system to manage the battery, usually with the function of measuring the battery voltage, to prevent or avoid the battery over-discharge, over-charge, over-temperature and other abnormal conditions. With the development of technology, many functions have been gradually added. The object is usually a secondary battery that can be recharged again, and in recent years, most of them appear at the same time with lithium-ion battery packs.
Classification of battery pcb board
Single battery pcb: for single battery monitoring and management.
Multi-battery pcb: used to monitor multiple battery units, commonly used in electric vehicles and energy storage systems.
Battery pcb board design principles
1. Design requirements and standards
Design of battery pcb needs to follow national and industry standards, such as UL, IPC, etc., to ensure safety and reliability.
2.Circuit design basis
Voltage and current calculation: rational circuit design based on the characteristics of the battery.
Signal integrity analysis: to ensure the integrity of the signal in the transmission process, to avoid interference.
3.Layout and wiring design
Component Layout Optimization: Reasonable arrangement of component positions to reduce signal interference.
Power supply and grounding layer design: design effective power supply and grounding scheme to enhance system stability.
4.Thermal Management Design
Thermal design principle: Ensure that the battery operates within a safe temperature range through reasonable thermal design.
Thermal simulation analysis: Use simulation software to predict the thermal performance of pcb and optimize the design.
5. Power and grounding design
Multi-layer pcb design: allocate dedicated power and grounding layers in multi-layer pcb to reduce power supply noise.
Ground loop design: avoid the formation of ground loops to ensure signal stability.
6. Component selection
High-temperature resistant components: Select components that can withstand high temperatures, especially in the case of heat generated by the battery operation.
High-reliability components: Use high-reliability components to ensure that there will be no failure in long-time operation.
7. Testing and Verification
Prototype testing: Prototype testing is conducted after the design is completed to verify the feasibility and stability of the design.
Simulation test: Test the circuit design through circuit simulation software to find potential problems and optimize.
8. Manufacturing
Simple design: Minimize complex circuits and layouts to facilitate production and assembly.
Standardized components: Use standardized components to reduce production costs and risks.
Pcb Manufacturing Process
1. Design and Document Generation
Circuit design: Use pcb design software (e.g. Altium Designer, Eagle, etc.) to create circuit schematics and pcb layouts.
Generate Gerber file: Convert the design to Gerber format, including layer information, drilling position, etc.
2. Material Preparation
Substrate selection: Commonly used substrates include FR-4, aluminum substrate, flexible pcb, etc., according to the specific application requirements.
Copper Foil Preparation: Select the appropriate thickness of copper foil, usually used to form the conductive path.
3. Manufacturing steps
Coating of photosensitive material: Apply photosensitive coating (dry or wet film) on the surface of the substrate.
Exposure: The circuit pattern is transferred to the photosensitive material by exposure.
Developing: The unexposed area is removed to form the circuit pattern.
Etching: A chemical etchant is used to remove excess copper, leaving the desired circuit pattern.
Drilling: Drill connection holes in the pcb using a drilling machine according to the design drawings.
Deburring process: Remove burrs after drilling holes to ensure connection quality.
4. Plating
Copper plating: electroplating on the pcb surface to improve conductivity and soldering performance.
Surface treatment: chemical nickel-gold plating, hot air leveling (HASL) and other methods to ensure good surface welding performance.
5. silk screen printing
Marker printing: printing markers, symbols and patterns on the pcb surface to facilitate component identification and operation.
6. Assembly
Component placement: automatically place the components onto the pcb through the placement machine.
Soldering: Reflow or wave soldering is used for component soldering to ensure the quality of solder joints.
7. Test
Function test: Function test on pcb to ensure all circuits and components work properly.
Automatic Optical Inspection (AOI): Use AOI equipment to inspect the soldering quality and component position.
8. Packaging and Delivery
Cleaning: clean the pcb surface and remove the residue from the soldering process.
Packing: Pack the qualified pcb to ensure safe transportation.
9. Follow-up service
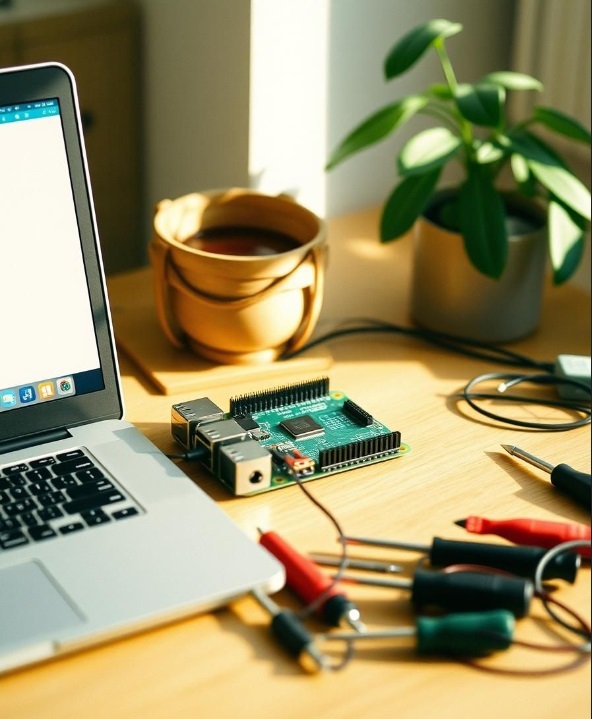
Technical support: provide customers with technical support for use and maintenance, solve problems encountered in the process of use.
Function and application of battery pcb board
Functions: Voltage monitoring-Real-time monitoring of the voltage of the battery cells to ensure that each cell is in a safe range. Current monitoring-Monitoring changes in current during charging and discharging to optimize charging and discharging efficiency. Temperature Monitoring- Use temperature sensors to detect battery temperature to prevent overheating.
Protection Functions: Overcharge Protection – Prevents the battery charging voltage from being too high to avoid battery damage or explosion. Over-discharge protection – prevents the battery discharge voltage from being too low, avoiding shortening of battery life due to over-discharge. Short-circuit protection-measure the short-circuit situation, cut off the circuit in time to protect the battery and circuit safety.
Equalization function: In a multi-cell battery pack, equalization charging ensures that the voltage of each battery cell is consistent, prolonging the service life of the battery pack. Data communication: Communicate with the main control system or external devices through 2C, CAN, UART and other protocols to transmit battery status and parameters. Data Recording: Record battery usage data to provide basis for subsequent analysis and maintenance.
Fault detection: real-time monitoring of battery operation status, timely detection of faults and early warning. Condition assessment: Evaluate the health condition of the battery and provide maintenance suggestions.
Application Fields
1.Electric Vehicle (EV)
Battery pcb boards are used in electric vehicles to manage the charging and discharging process of battery packs to ensure the safety and performance of electric vehicles.
2.Energy Storage Systems
Battery pcb boards are used to monitor and manage large battery packs in home and industrial energy storage systems to enhance the safety and reliability of energy storage.
3.Portable electronic devices
Such as cell phones, tablet PCs and laptops, battery pcb boards are used to manage the charging and discharging of built-in batteries and safety protection.
4.Power tools
Battery pcb boards are responsible for battery management in power tools to ensure that the tools are safe and reliable during use.
5.Medical equipment
In portable medical devices, the battery pcb board ensures the battery management when the device is in use and ensures the normal operation of the device.
6. Wearable devices
Such as smart watches and health monitoring devices, battery pcb boards provide miniaturized and efficient battery management solutions.
The main role of a battery pcb board is to protect the battery from damage and ensure that it operates within safe limits.
Battery pcb boards, also known as protection circuit boards, play a key role in lithium batteries. Its main duty is to ensure that the battery operates within a safe range, preventing overdischarge by limiting the minimum discharge voltage of the battery. This voltage range is usually set between 2.8 and 3v. Once the voltage drops below this range, the circuit board cuts off the output, thus protecting the battery from damage, such as preventing a device from suddenly shutting down due to a low charge. In addition, the protection circuit board controls the maximum charging current to prevent too high a current from causing the battery to overheat, or even triggering cell damage or more serious consequences. It also monitors the battery temperature during the charging process, and if the temperature is too high, the circuit board will automatically interrupt charging to ensure the safety of the user and the device.
The protection circuit board usually consists of components such as MOSFET-specific integrated circuits and temperature sensors, which are highly integrated SMD components that are often irreparable once damaged. The circuit board is usually encapsulated inside the battery, near the electrode tabs of the battery. Some manufacturers also add additional components to the circuit board, such as identification resistors, vibration motors or charging circuits, to enhance the functionality and safety of the battery.
Future Development Trends
The future development trend of battery pcb boards is mainly reflected in the growth of demand for high-performance electronic products, the application of high-density interconnect technology (HDI), the adoption of environmentally friendly materials, the growth of flexible circuit boards, and the application of automated manufacturing.
Growth in demand for high-performance electronics: With the iteration of the AI big model and the wave of automotive electrification/intelligent drive, the pcb industry is expected to usher in new development opportunities. Server and automotive electronics become the main driving force, driving the global pcb industry recovery. Global pcb industry output value is expected to usher in a rebound in 2024, of which the server/data storage, automotive and communications industry future growth rate is more robust.
The application of high density interconnect technology (hdi): hdi boards and packaging substrates and other high-end pcb products accounted for a gradual increase in the proportion of these products in high-end consumer electronics, servers and chips and other fields are widely used. With the continuous upgrading of electronic products, the performance requirements for pcb circuit boards are also increasingly high, the future market trend will be to high-density, high-speed, multi-layer boards and flexible circuit boards and other directions.
Adoption of environmentally friendly materials: With the improvement of environmental awareness and regulations, pcb chemicals industry is also developing in the direction of green and environmental protection. More and more companies are beginning to develop and use low-toxicity, low-pollution, recyclable chemicals to reduce the harm to the environment and health.
Growth of Flexible Circuit Boards: Flexible circuit boards are favored because of their unique bendable characteristics, especially for applications with limited space or irregular shapes. With the diversification of electronic product forms, the growth of flexible circuit boards is a clear trend.
Application of automated manufacturing: In order to improve production efficiency, intelligent manufacturing systems can monitor production lines, optimize processes through data analysis, and improve product quality and consistency. The application of automated manufacturing will promote the pcb industry to the direction of higher efficiency and quality.
In summary, the future development trend of battery pcb board will be closely centered on the growth of demand for high-performance electronic products, the use of advanced high-density interconnection technology, focusing on the use of environmentally friendly materials, to adapt to the growth in demand for flexible circuit boards, as well as the application of automated manufacturing to adapt to the ever-changing market demand and technological advances
Battery pcb boards have a wide range of applications and play a key role in modern electronic devices. Its functions such as monitoring, protection, equalization charging and communication ensure the safety, efficiency and long life of the battery. As technology continues to advance, the design and application of battery pcb boards will continue to evolve, adapting to increasingly complex battery management requirements.