Ceramic pcb materials, with their excellent physical and chemical properties, are increasingly being used in electronics, aerospace, medical and energy applications. In this paper, we will discuss the properties of ceramic pcb materials, their preparation process and their wide range of applications. Currently, commonly used ceramic substrate materials for electronic packaging include alumina (Al2O3), aluminium nitride (AlN), silicon nitride (Si3N4), beryllium oxide (BeO) and so on.
Alumina ceramics with rich raw material sources, low prices, high insulation, thermal shock, chemical corrosion resistance and mechanical strength, is a good overall performance of the ceramic substrate materials, accounting for more than 80% of the total ceramic substrate materials. But because of its relatively low thermal conductivity (99% alumina thermal conductivity of about 30 W / (m – K), high coefficient of thermal expansion, generally used in automotive electronics, semiconductor lighting, electrical equipment and other fields.
Aluminium nitride ceramics thermal conductivity of alumina ceramics 6 ~ 8 times, but the coefficient of thermal expansion of only 50%, in addition to high dielectric strength, low dielectric constant, good corrosion resistance and other advantages. In addition to the higher cost, aluminium nitride ceramics are better than alumina ceramics, is a very ideal electronic packaging substrate materials, especially for thermal conductivity requirements of the field.
Silicon Nitride Ceramics (Si3N4)
In the existing ceramic pcb materials can be used as a substrate material, Si3N4 ceramic bending strength (more than 800 MPa), wear resistance, is the best comprehensive mechanical properties of ceramic materials, while its coefficient of thermal expansion is the smallest, and is therefore considered a very promising power device packaging substrate materials. However, its preparation process is complex, high cost, low thermal conductivity, mainly suitable for applications in the field of high strength requirements but not high heat dissipation requirements.
Beryllium Oxide (BeO)
BeO material has low density, high thermal conductivity, and good comprehensive performance.However,BeO materials also have some shortcomings, including:
(1) BeO powder is toxic, inhalation of large quantities of human body will lead to acute pneumonia,long-term inhalation will cause chronic beryllium lung disease, so special protective measures should be used in the production process;
(2) The sintering temperature of BeO can be as high as 1900°C or more, so the production cost is high;
(3) Thermal conductivity decreases with increasing temperature, for example, in the temperature range of 0°C ~ 600°C,the average thermal conductivity of BeO ceramics is 206.67 W/(m-K), but when the temperature rises to 800°C, its thermal conductivity decreases to one tenth,the above reasons limit the popularisation and application of beryllium oxide.However,in some high-power,high-frequency semiconductor devices,as well as avionics and satellite communications, in order to pursue high thermal conductivity and ideal high-frequency characteristics,still using BeO ceramic substrate.
Other Ceramic pcb Materials
In addition to the above ceramic pcb materials, silicon carbide (SiC), boron nitride (BN), etc. can also be used as ceramic substrate materials. Table 1 compares the performance of several commonly used ceramic pcb materials.
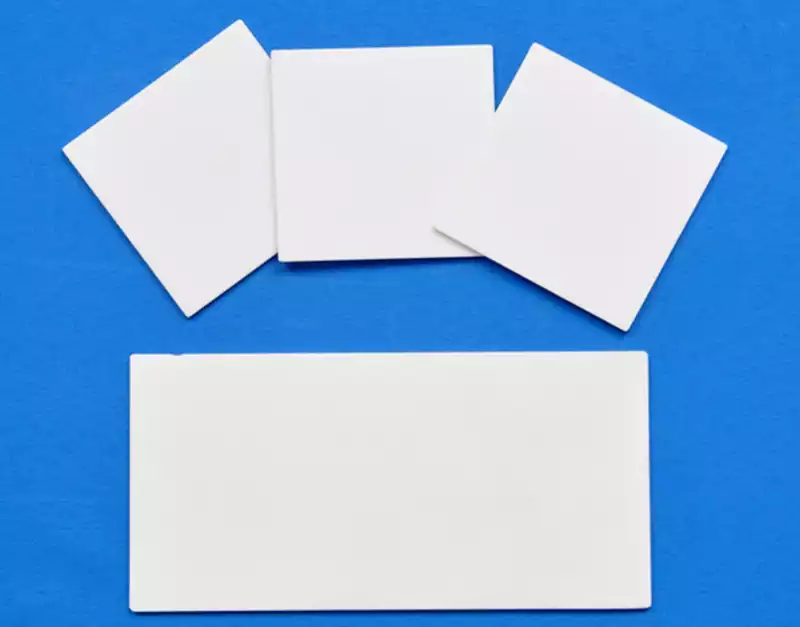
Factors to be considered when selecting ceramic PCB materials:
1.Thermal Conductivity
Thermal Conductivity: The thermal conductivity of ceramic materials is critical for high power and high frequency applications. Higher thermal conductivity can effectively dissipate heat and prevent electronic components from overheating. For example, Aluminium Nitride (AlN) has high thermal conductivity and is suitable for applications where the need for heat dissipation is greater than mechanical stability.
2.Coefficient of Thermal Expansion (CTE)
Coefficient of Thermal Expansion (CTE): A low CTE reduces the stress caused by temperature changes, thus extending the life of the PCB. Ceramic materials usually have a low CTE, which allows them to maintain a stable size and shape in high temperature environments.
3.Electrical insulation properties
Dielectric Strength and Dielectric Constant: Ceramic materials generally exhibit good electrical insulation properties and are suitable for the insulation and encapsulation of electronic components. Higher dielectric constants help in the design of high frequency circuits, reducing internal signal reflections and resonance noise.
4.Chemical Stability
Corrosion resistance: In some harsh environments, materials need to have good chemical stability and corrosion resistance to ensure reliable operation over long periods of time.
5.Mechanical Strength
Durability: The mechanical strength and rigidity of ceramic materials determines their performance in high vibration or high shock applications with higher durability and reliability.
6.Cost
Economical:The cost of ceramic PCB materials is usually high, so budgetary constraints need to be considered when selecting and weighing up the performance of the material against the cost based on the specific needs of the application, e.g. Aluminium Oxide is usually relatively inexpensive, whereas Aluminium Nitride and Beryllium Oxide are more costly.
7.Machinability
Manufacturing Process: Different ceramic materials have different levels of difficulty in processing. Beryllium Oxide (BeO) usually requires special treatment due to its toxicity and difficulty in processing, while Aluminium Oxide is easy to process and less costly.
8.Application-specific requirements
Application-specific requirements: The selection of materials needs to be based on specific application scenarios. For example, PCBs used in automotive, aerospace, high-temperature or high-frequency conditions may require more targeted ceramic materials.
Ceramic pcb materials have shown great potential in many areas thanks to their diverse and excellent properties. In the future, with the continuous progress of technology, the application range of ceramic substrate materials will be further expanded to provide strong support for scientific and technological development and industrial upgrading.