SMT high temperature soldering technology is a soldering method that uses peak soldering temperatures in excess of 220°C in the SMT (or Surface Mount Technology) process. This technique is typically implemented in the 245 to 247°C temperature range to ensure that the solder paste and the BGA (ball grid array) solder balls are able to achieve near complete fusion, resulting in a uniform solder joint configuration.
At higher temperatures than 220°C, there are two more complex process challenges. In the case of double-sided mounting, the BGA solder balls are often subjected to two reflow processes, and in most cases a third. In this process, the BGA solder ball after many repeated hot melt, has been in a semi-molten to melted state, the whole process can be regarded as a continuous process of ‘two collapses and mixed diffusion’. At the same time, the use of special process processing substrate, such as by the OSP (organic bonding film) process of the substrate, also faces a severe test.
When the high temperature process is frequent, the quality of the product may be abnormal. In order to avoid this problem, shortening the soldering time as a control method may lead to the creation of ‘micro voids’. These micro-voids are formed during the solidification of the solder joint and are usually close to circular in appearance, with a slight difference from the bad solder joints caused by voids.
Under these process conditions, the BGA solder ball melts and eventually collapses twice, while ensuring an even compositional distribution of the BGA solder joint. As a result, the process exhibits good stability. It can be inferred from this:
For the peak temperature of the BGA solder joint, to ensure that the solder and the solder ball can be fully mixed and achieve the secondary collapse, the more reasonable temperature range should be between 220 ℃ and 235 ℃. This temperature range can reduce both the incidence of voids and the phenomenon of segregation.
In terms of time, an excessively long welding time can lead to greater deformation, which in turn may trigger abnormalities. Therefore, the soldering temperature above 183°C should be kept above 40 seconds (usually 60 to 90 seconds can be chosen as a suitable time range).
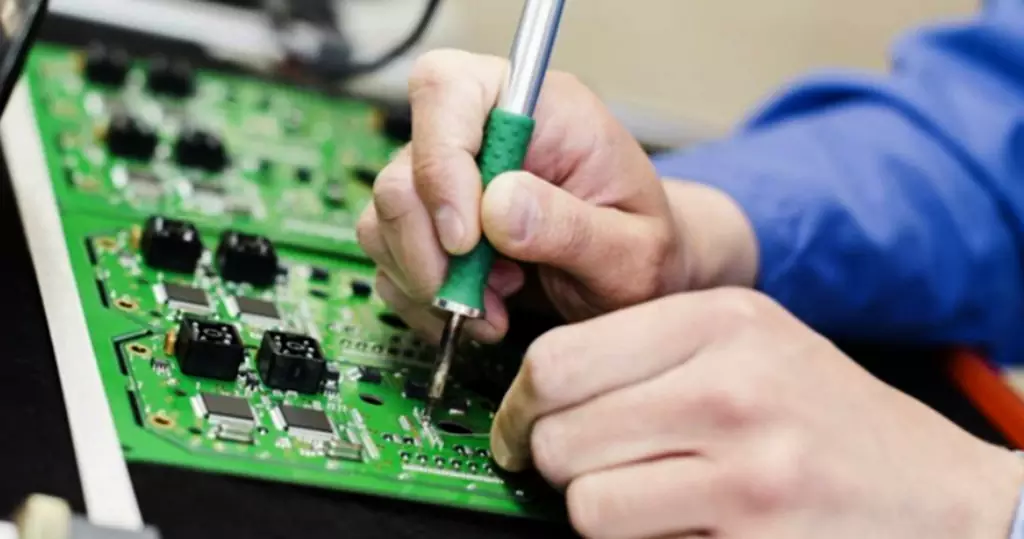
Mechanism of high temperature soldering technology
Principle of hot-melt bonding
High temperature soldering technology operates by means of hot-melt bonding, the core of which is to raise the temperature of the pads and the solder paste to achieve a strong electrical connection between the component and the circuit board.
Surface Tension Effect
When the temperature reaches a high state, the surface tension of the solder paste will be reduced accordingly, this change makes the solder paste can more smoothly cover the pad and component pins, and then form a uniform solder contact.
High temperature soldering technology plays an important role in modern manufacturing, especially in the connection and integration of electronic components. High temperature soldering offers the following significant advantages over traditional soldering methods:
Enhanced strength: High temperature soldering improves the mechanical strength of soldered joints by melting the solder and the base material to form a stronger connection at high temperatures. This increased strength ensures a more stable joint under the influence of vibration and mechanical stress.
Adaptability to a wide range of materials: This welding technique can be applied to a wide range of materials such as copper, aluminium and easily weldable metals, and it overcomes chemical and physical differences between the materials to form a long-lasting joint. This makes high-temperature welding highly adaptable to different applications.
Good electrical conductivity: In electronics, good electrical conductivity is an important characteristic of solder joints. High temperature soldering ensures excellent electrical contact between the solder and the component and PCB, thus improving the overall electrical performance. This is critical for high-frequency, high-speed signal transmission electronics.
Thermal shock resistance: High temperature soldered seams are able to withstand higher temperature variations without failing, making them suitable for use in electronic equipment that operates in high-temperature or shock-inducing environments. This characteristic makes high temperature welding is often used in aerospace, automotive and industrial equipment and other demanding areas.
Welding integration: Because high temperature soldering can be performed at higher temperatures, manufacturers are able to streamline their production processes and increase productivity by integrating the welding process, i.e., joining materials and securing components.
Fields of application of high temperature soldering technology
Surface mount technology (SMT) field
In the manufacturing process of SMT, high temperature soldering technology is commonly adopted for the soldering of SMD components and IC chips to ensure a solid connection between the components and the PCB board.
Wave soldering process
Wave soldering technology is widely used for plug-in components or PCBs that require double-sided soldering. The technology uses high temperature to melt the solder peaks, and then complete the task of welding connection.
High temperature soldering technology operation points
Temperature control
The temperature during the soldering process must be strictly controlled to prevent welding defects or component damage that may be caused by excessive temperature.
Welding time management
Reasonable control of the welding time to ensure the uniformity and stability of the welding, while avoiding over-welding or under-welding of the welding point.
High temperature soldering technology with its unique advantages in the modern manufacturing industry occupies an important position, but need to strictly regulate the temperature and welding time to ensure welding quality and product performance. With the continuous progress of technology, high temperature welding technology will play a greater role in the manufacturing industry.