PCB board is often designed for small-current applications, so what can be done to enhance PCB boards to withstand larger currents? After all, the current demand of the electronic products we use daily is usually only between tens of milliamps to a few amps, and if we suddenly encounter a high current of tens of amps or even more than 100 amps, it is likely to directly lead to damage to the circuit boards or cause safety accidents. What are the solutions to this concern?
The first method is to optimise the wiring on the PCB board.This is the most common tool we use when designing PCBs because the width of the wiring is directly proportional to its ability to carry current,but it does not increase linearly. For example, if a 10 mil wide cabling can safely carry 1A of current under the same conditions, then a 50 mil wide cabling does not mean that it can directly carry 5 times the current, i.e. 5A.
Therefore,it is critical to understand the basic structure of a PCB board before delving into it.Taking a simple double-layer board as an example, this type of circuit board consists of three layers:a top and bottom layer of copper foil (i.e., copper skin),and an insulating sheet in the middle. The copper foil is the main conduit through which current and signals travel through the PCB. When designing PCBs that need to carry high currents,we often adopt the following strategies:
(1) Widen the width of the conductor.Generally,the conventional standard is 1 ampere of current per millimetre (about 40 mils) of conductor that can be safely carried;
(2) Increase the thickness of the copper foil, e.g., 1 ounce, 2 ounces or more;
(3) Windowing the wire and adding metals such as tin, silver, and copper to enhance conductivity.
In engineering practice, the specific requirements for wiring length are not stringent.Usually,engineers will be based on the thickness of copper foil, temperature rise and wire diameter of the three key indicators to assess the current-carrying capacity of the PCB.In addition,by reviewing the relevant tables,we can learn how to increase the thickness of copper foil and widen the wire diameter to improve the thermal efficiency of the PCB board, thereby enhancing its current-carrying capacity.
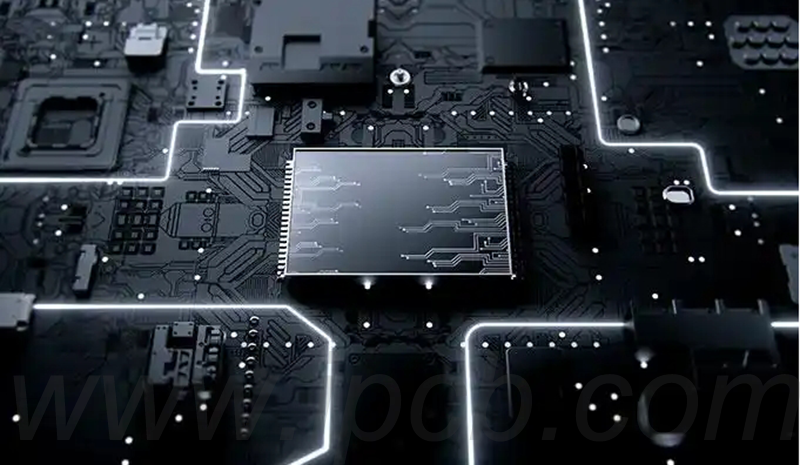
The second method is to use terminal blocks for wiring. In addition to wiring directly on the PCB board, terminal block wiring is also a viable option. Terminal blocks have two main functions:
(1) fixed role: as a screw post, it has a thread, which requires the use of metal must have a certain degree of hardness and easy to manufacture. In this regard, brass, aluminium alloys and steel are three common and cost-effective materials that have the appropriate hardness.
(2) Grounding function:For grounding, almost any type of metal can meet the grounding requirements since it does not carry large loads and the screw posts are usually thick and numerous.
The third method is to use copper rows.In industrial applications,especially such as transformers,server cabinets and other scenarios that need to carry high currents,we often need to customise copper rows for wiring.
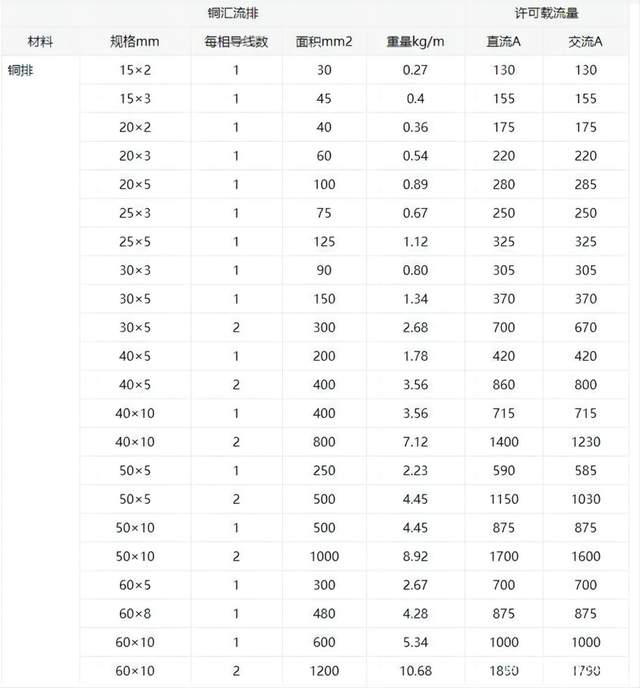
Cautions:
(1) When the current is too high, it may lead to severe heating of the PCB board, and possibly even localised overheating, as the current is not evenly distributed in the conductor. The glass transition temperature (TG) of commonly used FR4 materials is usually between 140 and 170 degrees C. Although exceeding this temperature may not cause combustion, it can lead to softening of the board and a significant drop in electrical properties.
(2) In addition, the reliability and stability of the board will be seriously affected as a result.
We have explored a variety of effective solutions to the problem of how PCB boards can carry high currents. From optimising PCB wiring, using terminal blocks, adopting copper rows, to applying special process means, each method has its unique advantages and applicable scenarios. However, no matter which method is used, close attention needs to be paid to current distribution, heat generation, and material reliability during the design and implementation process. Especially in the face of high-current applications, we must ensure that the PCB board can work safely and stably, to avoid the softening of the board due to excessive current, electrical performance degradation and other safety hazards.