PCB manufacturing is a complex and delicate process that involves numerous matching points,and the slightest mishap can lead to defects in the board, which in turn affects the quality of the entire PCB.Common quality problems such as short circuits and open circuits often stem from multiple factors.
Common causes of defects in PCB manufacturing include:
Short circuits
Poor pad design:To avoid short circuits,you can change round pads to oval shapes and increase the distance between pads.
Improper component orientation:For example,the legs of SOIC components may trigger short circuits if they are parallel to the tin wave.Therefore, the component orientation should be properly adjusted so that it is perpendicular to the tin wave.
Automatic plug-in foot bending: IPC stipulates that the length of the foot of the line should be less than 2mm, and the foot bending angle is too large which may lead to the falling of the parts,thus triggering a short circuit.Therefore,solder joints should be kept at least 2mm away from the line.
Other causes include oversized holes in the substrate, too low a temperature in the soldering furnace,poor solderability of the board,failure of the solder resist film, and contamination of the board surface. Engineers should carry out detailed troubleshooting for these causes.
Open circuit
Open circuit usually occurs when the trace is broken or the solder only stays on the pad without connecting with the component leads. This may be due to the lack of adhesion or connection between the component and the PCB board,similar to a short-circuit problem,and may occur during manufacturing,soldering,or other operations.
Vibration, stretching, dropping, or other mechanical deformation factors can damage traces or solder joints.
Chemical or moisture effects may also cause solder or metal parts to wear out,resulting in component lead breakage.
Dark and grainy joints on PCB board
This type of problem is usually caused by contaminated solder or excessive oxides in the dissolved tin,making the solder joint structure weak.
Another cause is a change in the composition of the solder,with too many impurities. In this case,it is necessary to add pure tin or replace the solder.
Spots or physical changes in the glassy fibre build-up (e.g. separation of layers) may also occur,but this is not a result of a bad solder joint,but rather of the substrate being heated too much.Reducing the preheating and soldering temperatures or increasing the substrate travelling speed can solve the problem.
PCB board solder joints become golden yellow
Under normal circumstances, the solder of the PCB board appears silver grey.However,sometimes the solder joints will appear golden yellow,which is mainly due to the high temperature. In this case, simply lower the temperature of the soldering furnace.
Environmental Effects
Environmental factors such as extreme temperatures, fluctuating temperatures, excessive humidity,and high-intensity vibration may cause damage to the PCB board.
Temperature variations may cause the board to deform, which can damage solder joints,bend the shape of the board,or cause copper traces to break.
Moisture in the air can cause oxidation,corrosion and rust on metal surfaces, adversely affecting exposed copper traces,solder joints,pads and component leads.
Accumulation of dirt, dust or debris on component and PCB surfaces can reduce air flow and cooling,resulting in PCB overheating and degradation of performance.
Vibration, dropping, hitting or bending a PCB board can cause it to deform or crack, while high currents or overvoltages can penetrate the board or cause rapid deterioration of components and pathways.
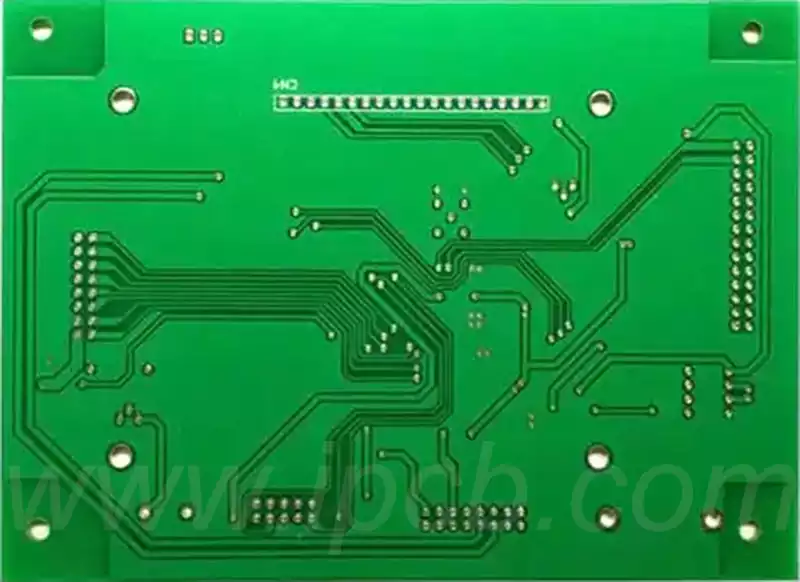
The problem of micro-etched layer separation is like an undercurrent, always threatening the quality of PCB products.It can not only weaken the performance of the PCB board, but also on the reliability and stability of the entire electronic device poses a major challenge.The following is an in-depth analysis of the problem and response strategy:
Root cause analysis:
Material quality is not up to standard:the selection of the substrate or plating materials, if there are impurities, uneven distribution and other issues, will weaken the plating and the substrate between the bonding force, laying the separation of hidden dangers.
Improper configuration of process parameters:If key parameters such as concentration, temperature, duration and flow rate of etching solution are not properly adjusted, it may lead to insufficient bonding between the plating layer and the substrate.
Inadequate surface treatment:pre-treatment steps such as cleaning, activation, etc.,if the implementation is not in place,will directly affect the adhesion effect of the subsequent coating.
Influence of environmental factors:Fluctuations in external environmental conditions,such as humidity and temperature, may interfere with material properties and thus affect the quality of the plated layer.
Preventive measures:
Strictly control the quality of materials: choose high-quality base materials and plating materials, to ensure that they meet the established standards and requirements, to reduce the risk of separation from the source.
Optimise process parameter settings: according to the material characteristics, finely adjust the ratio of etching solution, temperature, time and other key parameters to ensure the stability and repeatability of the process.
Strengthen the surface treatment process: Enhance the effectiveness of the pre-treatment step, adopt more efficient cleaning agents and activation means, and strengthen the chemical bonding force between the coating and the substrate.
Improve the working environment: Maintain a stable working environment to minimise the potential impact of temperature and humidity fluctuations on material performance.
Regular maintenance of production equipment: Ensure that production equipment is in optimal condition, and avoid quality problems caused by aging or malfunctioning equipment through regular inspections and calibrations.
Increase the number of quality inspection points: Increase the number of quality inspection points in the production process to detect and solve potential problems in time to ensure product quality.
The many quality issues faced during PCB manufacturing pose a serious challenge to product performance,reliability and stability.In order to ensure the excellent quality of PCBs,we must start from the source,strictly control the quality of materials,optimise process parameters,and strengthen the surface treatment process.At the same time,improving the working environment,regular maintenance of production equipment,and additional quality testing are all essential key measures.