Cleaning solution for circuit boards, commonly known as board washer, or circuit board cleaner, is a chemical industry cleaner solution used to clean flux and rosin on the surface of PCB boards after soldering, and is used for semiconductor-related parts, electronic parts, and metal parts, and is an ‘environmentally friendly’ cleaner that combines high cleanliness and safety.
The main function of cleaning solution for circuit boards is to clean circuit boards and electronic assemblies, stripping their surfaces of stains and oxides to ensure their proper functioning. Specifically, the role of electronic wash water can be summarised as follows:
1.Remove the accumulated dirt on the circuit boards
During the manufacturing and use of electronic products, various kinds of dirt, such as dust, grease, soldering residues, etc., will accumulate. These dirt will interfere with the interaction between the components on the circuit board, affecting the normal operation of electronic products. Surfactant and surfactant components contained in the cleaning solution for circuit boards can effectively remove such dirt.
2.Eliminate the oxidised layer on circuit boards
Long-term use or storage may lead to the formation of oxidised layers on the surfaces of components or connections on circuit boards. These oxidised layers can lead to problems such as heating and leakage of components during use.Cleaning solution for circuit boards as a de-oxidising ability of the liquid, can effectively remove these oxide layers, to protect the normal operation of electronic products.
3.Improve the quality of circuit boards
Remove the surface of the circuit board stains and oxidation layer, not only to ensure the normal operation of electronic components, but also to improve the overall quality of the circuit board. If it is not possible to remove these stains and oxidised layers, it may have an adverse effect on the subsequent process steps, which in turn affects the quality of the entire circuit board.
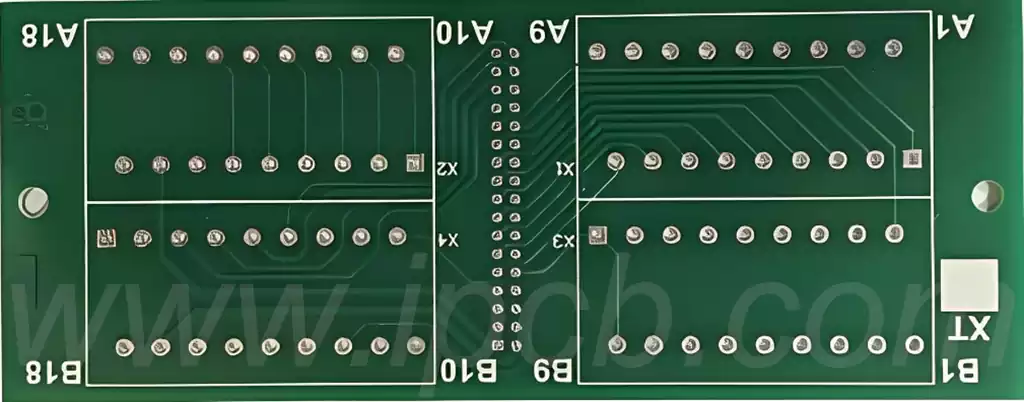
Cleaning solution for circuit boards Option 1: Aqueous Cleaners
The aqueous cleaning process relies on water as the cleaning medium, and small amounts of surfactants, additives, corrosion inhibitors and other chemical components (typically 2% to 10%) can be added to enhance the cleaning performance. According to the different characteristics of the contaminants on the printed circuit board, the flexibility to add additives to the water-based cleaner, thereby broadening its scope of application.
In combination with ultrasonic cleaning equipment, the insoluble dirt on electronic circuit boards can be effectively stripped off by using the ‘cavitation effect’ (i.e., the rapid formation and rupture of tiny bubbles) that occurs when ultrasonic waves travel through the cleaning solution. In view of the printed circuit boards and electronic components and ultrasonic compatibility needs, the cleaning of the ultrasonic frequency of 40KHz.
The aqueous cleaning process covers three major steps: washing, rinsing and drying. Firstly, aqueous cleaners with a concentration of 2% to 10% are used in combination with physical cleaning methods such as heating, brushing, spraying and ultrasonic waves to batch process the printed circuit boards; subsequently, two to three rinses are carried out using purified or de-ionised (DI) water; and lastly, drying is carried out by hot air.
Cleaning solution for circuit boards Option 2: Hydrocarbon Cleaners
Hydrocarbon Cleaning solution for circuit boards is suitable for manual brushing and localised surface wiping, but the operating environment needs to maintain air circulation to ensure that the concentration is within safety standards.
The characteristics of hydrocarbon cleaners include:
(1) Compared with hydrochlorofluorocarbons (HCFCs), their cleaning power is weakened and the removal effect is poorer.
(2) Higher safety risks, particularly flammability and explosiveness, especially at high air levels.
(3) Low boiling point and fast volatilisation, resulting in high consumption and increased costs.
Cleaning solution for circuit boards option three: organic solvents
The solvent cleaning process is relatively simple, requiring only the same solvent cleaner for cleaning and rinsing. Due to the high volatility of solvent cleaners, no special drying step is required. The solvent can be distilled and separated from the dirt and recycled after use, which reduces costs and simplifies waste liquid disposal. The original use of CFC-113 cleaning equipment can be used with minor adjustments; solvent cleaning is particularly suitable for water-sensitive, component sealing poor printed circuit board.
Solvent cleaning process includes the following:
1.Ultrasonic combined with immersion cleaning – spray cleaning – gas-phase rinsing and drying
2.Solvent heating immersion cleaning – cold rinsing – spray cleaning – gas phase rinsing and drying
3.Vapour phase cleaning–Ultrasonic combined with immersion cleaning–Cold rinsing–Vapour phase rinsing and drying
4.Vapour Phase Cleaning – Spray Cleaning – Vapour Rinsing & Drying
Cleaning solution for circuit boards is a key auxiliary material in electronic manufacturing, its main function is to clean circuit boards, remove surface dirt and oxides to ensure the normal operation of electronic products. The selection and use of PCB cleaners should be weighed against actual production requirements, cost-effectiveness, safety and environmental friendliness.