Wave soldering, also known as surge wave soldering, is a method of forming wave-like peaks through molten solder, so that the pads and component pins on the circuit board can be soldered as they pass through the peaks of the solder wave. The core of the solder tank is continuously heated and maintain a certain temperature of the solder, driven by the pump to form a continuous wave, when the circuit board at a certain angle and speed through the solder wave, the solder wetting pads and pins, after cooling to form a solid welding point.
The wave soldering process can be roughly divided into the following steps:
Preheating: The circuit board needs to pass through a preheating zone before entering the solder wave to remove moisture and reduce thermal stress, while preheating helps improve the wettability of the solder.
Flux Coating: After preheating, the surface of the board is coated with a layer of flux, which is used to remove the oxidised layer, prevent re-oxidation and improve the flow of the solder.
Wave soldering: The board passes through the solder wave at a set angle and speed, and the solder wets the pads and pins to form a solder joint.
Cooling: The circuit board enters the cooling zone after soldering to rapidly cool down and solidify the solder to ensure solder strength.
Cleaning: Remove residual flux and other contaminants to prevent corrosion.
Key parameters of wave soldering
Solder temperature: directly affects the wettability of the solder and the quality of the solder, generally controlled between 245 ° C and 260 ° C.
Transfer speed: too fast may lead to inadequate welding, too slow is easy to produce bridging, need to be adjusted according to the board thickness, component layout.
Wave height: affect the contact time of the solder and pads, pins, need to ensure that the solder can be fully wetted and not overflow.
Preheating temperature and time: insufficient preheating will lead to poor soldering, excessive preheating may damage the components, need to be precisely controlled.
Characteristics
Suitable for high volume soldering production.
High efficiency, able to weld multiple joints at the same time.
Suitable for products that do not require very high welding quality.
Reflow Soldering (Reflow Soldering) is a kind of surface assembling technique of soldering components one by one, through heating equipment to make the solder paste melt, and then form the process of soldering points on the PCB.
Process Flow
Solder Paste Coating: Solder paste is coated on the surface of the PCB and components are mounted.
Pre-heating stage: The PCB is gradually heated to a temperature that melts the solder paste.
Reflow Stage: Keep the solder paste in the molten state, so that the soldering point is properly combined with the components and PCB.
Cooling and curing: After the soldering is completed, the PCB is cooled and cured.
Features
Suitable for small batch or small to medium scale production.
High flexibility, suitable for multi-species and small quantity production.
Control of welding temperature and time more accurate, suitable for higher welding quality requirements of the product.
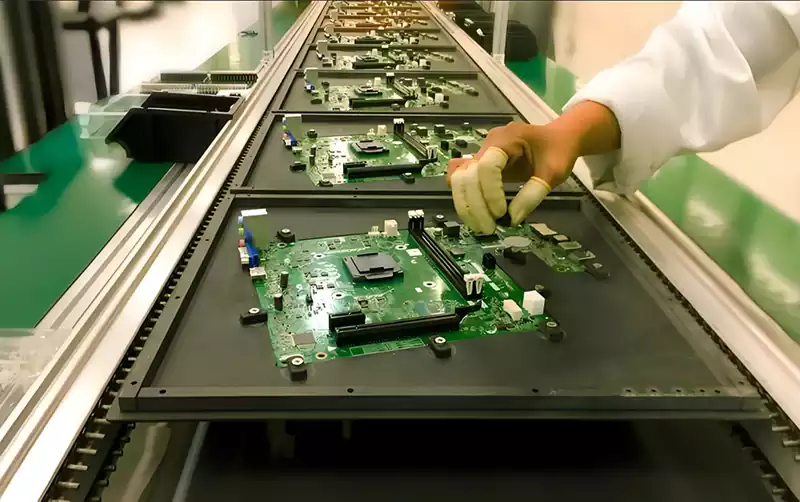
What is the difference between wave soldering and reflow soldering?
Wave Soldering: Wave soldering is the formation of solder peaks from molten solder, and then components are soldered through the peaks. This type of soldering is suitable for pin electronic components, whose pins are upright and need to be connected to the pads through the solder wave.
Reflow Soldering: Reflow soldering is to melt the solder by forming a reflow through the high temperature hot air, so that the solder joints are connected with the pads. It is mainly applicable to SMD electronic components, which have flat pins or solder ends that can be in direct contact with the pad.
Applicable objects
Wave soldering: Because of the way wave soldering works, it is more suitable for soldering pin electronic components, especially those that need to be connected to the pad through the wave of solder.
Reflow Soldering: Reflow soldering is more suitable for the soldering of SMD electronic components, and this type of soldering can effectively realise the electrical interconnection between the components and the pads.
Principle and process
Wave soldering: Wave soldering is through the jet melting soft brazing solder (such as lead-tin alloy), the formation of solder wave, so that the pre-loaded components of the printed circuit board through the solder wave, so as to achieve the components of the soldering end or pin and the printed circuit board pads between the mechanical and electrical connection. In this process, the high temperature liquid tin to maintain a sloping surface, and by a special device to make the liquid tin to form a wave-like phenomenon, hence the name ‘wave soldering’.
Reflow soldering: Reflow soldering is before the welding, pre-coated solder paste on the pad, and then through the high temperature hot air to make the solder paste melting, and the electronic components of the pins or soldering end and pad connection. This type of soldering makes use of the action of the hot air flow on the solder joints, so that the gel-like solder paste under a certain high temperature air flow to carry out the physical reaction, to achieve the purpose of soldering.