With the rapid development of automotive electronics technology,automotive pcb assembly as the core component of automotive intelligence and automation,the importance of its processing process is becoming increasingly prominent.
The processing flow of automotive pcb assembly:
1.Preparation stage of raw materials
Circuit board substrate selection: according to the special needs of automotive electronics, select the appropriate circuit board substrate materials. In view of the harshness of the internal environment of the car, such as large fluctuations in temperature, strong vibration and the presence of electromagnetic interference,usually choose a substrate with high heat resistance, excellent mechanical strength and good electromagnetic compatibility, such as specially modified FR-4 sheet or high-performance flexible sheet. These substrates must meet strict industry standards to ensure stable operation under complex working conditions.
Screening and purchasing of electronic components:Based on the design of automotive electronic circuits,we accurately select the required electronic components, including resistors,capacitors,inductors,chips,etc.The quality of the components has a significant impact on the quality of the PCBA.The quality of the components has a decisive impact on the quality of the PCBA,so it is necessary to use products that meet the automotive grade standards, which should have high reliability and adaptability in a wide temperature range and other characteristics.For example,chips used in automotive engine control systems must be able to operate accurately in extreme temperatures ranging from -40℃ to 125℃,thus ensuring stable engine regulation.Purchased components need to undergo strict factory inspection to check the integrity of their appearance and the accuracy of electrical parameters to prevent defective products from entering the production line.
2.SMT SMD Processing
Solder Paste Printing:Using carefully formulated solder paste,it is evenly printed onto the pads of the circuit board through the stencil.Automotive pcb assembly require a high degree of precision in solder paste printing,as even small deviations may lead to subsequent soldering defects, thus affecting the performance of the circuit. Stencils are usually made using high-precision laser cutting or etching processes, and different mesh sizes and shapes are designed for different types of component pads to ensure just the right amount of solder paste.For example,for tiny package components such as 0201, the mesh will be designed accordingly small,in order to control the amount of solder paste and prevent short-circuiting; while for large area pads such as BGA package chips,the mesh is designed to be larger, in order to ensure that sufficient solder paste, so as to achieve reliable soldering.
Component placement: With the help of high-precision placement machines,electronic components are quickly and accurately placed on the pads printed with solder paste.The bonder recognises the position of the component and carries out the pick-and-place operation according to a pre-set programme. In automotive electronics, the precision of the mounter needs to be in the micron range to cope with the many tiny and tightly packed components on complex PCBAs such as in-car navigation systems and self-driving controllers.The placement process ensures that the component pins are perfectly bonded to the solder paste,laying a solid foundation for subsequent soldering.
Reflow processing:After the mounting is completed,it enters the reflow soldering process.Through precise control of the temperature profile, the solder paste is heated,melted and solidified to form a reliable solder joint.The design of reflow temperature profile for automotive pcb assembly needs to take into account a variety of factors,such as the heat-resistant properties of different components,the material of the circuit board substrate and so on.Too high a temperature may damage the components,while too low can not guarantee the quality of the solder joints.Therefore,a multi-temperature reflow oven is usually used to ensure that the solder paste completes melting and solidification in the right time through the process of gradual heating,constant temperature and cooling, so as to achieve high-quality soldering.
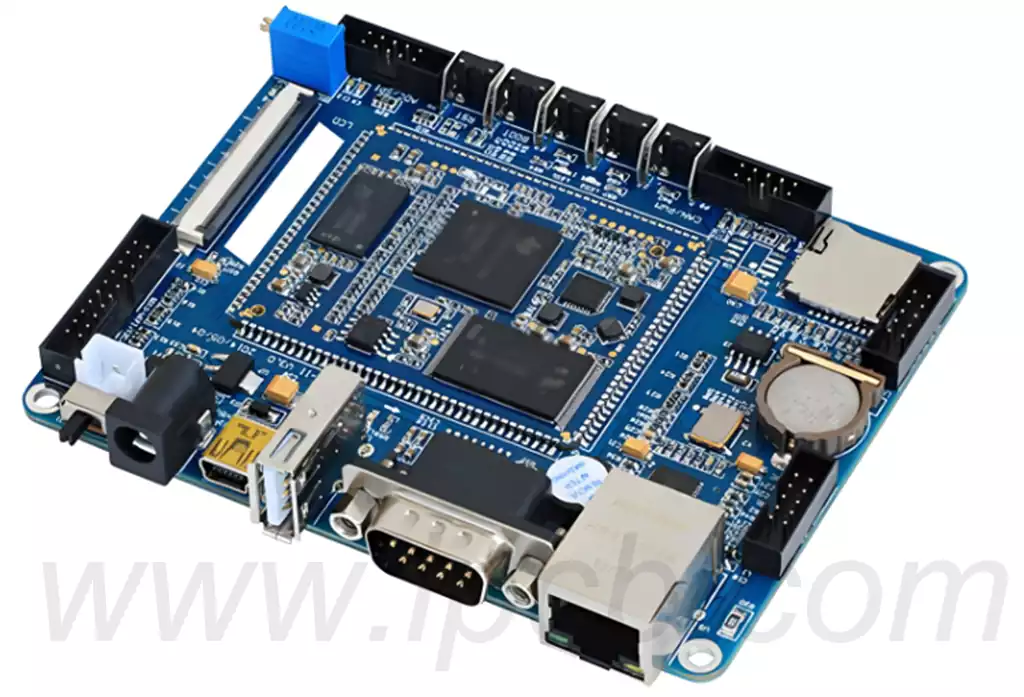
3.THT plug-in processing (if required)
For some automotive pcb assembly,it may also involve through-hole insertion technology (THT) processing link. For some components with higher power, high mechanical strength requirements or not suitable for SMT placement,such as large electrolytic capacitors, relays, etc.,THT process is required.
Insertion operation:Workers need to insert the pins of the components into the pre-drilled holes in the circuit board,requiring the insertion of the depth of the right and straight pins to ensure a good connection with the circuit board and the inner layer of the line.This process needs to be combined with manual operation and auxiliary tooling to ensure the accuracy and consistency of the plug-in.
Wave Soldering: After the insertion is complete, wave soldering equipment is used to perform the soldering. Liquid solder will form a shape similar to the wave, the board from the crest of the wave through, so that the component pins and circuit board pads are fully impregnated and welded together. The key to wave soldering is to control the temperature of the solder, the height of the wave and the speed of the solder to ensure that the solder joints are full and no welding phenomenon, while avoiding short-circuiting caused by too much solder and other problems.
4.Testing and debugging stage
Meticulous inspection of appearance: The completed automotive pcb assembly is subjected to a comprehensive and meticulous appearance inspection to check whether there are missing, offset or damaged components, and whether there are problems such as false soldering, short-circuiting or leakage of soldering joints.With the help of magnifying glasses, microscopes and other tools, inspectors will carefully screen every detail to ensure that the appearance of the PCBA meets the quality requirements. For example, when inspecting automotive airbag control PCBAs, any defect in the solder joints may cause the airbag to fail to eject properly at critical moments, thus endangering lives, so the appearance inspection is crucial.
Electrical performance testing:Use professional test equipment to detect the electrical parameters of the PCBA.Through the through test to confirm whether the circuit connection is normal;through the voltage and current test to verify that the power supply module and the output of the functional circuits are in line with the design standards;through the signal integrity test to ensure that the transmission of high-speed digital signals without error.Take the car audio PCBA as an example, the frequency response of the audio signal,distortion and other parameters need to be tested to ensure that the sound quality is clear and pure.Only PCBAs that have passed the electrical performance test can proceed to the next step.
Comprehensive functionality testing:Simulate the actual operating environment of the car,and conduct functionality testing on the PCBA.It is installed into the special test tooling and verified according to the operation process of automotive electronic equipment in actual use.For example,when testing the PCBA of automotive electric power steering system,it will simulate the working conditions under different vehicle speeds and steering angles to observe whether the PCBA can accurately control the power motor and achieve smooth steering.Functional testing can identify problems that are difficult to detect in electrical performance testing,thus ensuring that the PCBA meets the actual needs of the car.
5.Three-Proof Processing
Considering the complexity of the automotive driving environment,automotive pcb assembly usually need to be treated with three-proof (moisture-proof,mould-proof and salt spray-proof).Using special three-proof paint,and through spraying,dipping or brushing,etc.,a protective film is formed on the surface of PCBA to isolate the external moisture,mould,salt spray and other unfavourable factors,so as to extend the service life of PCBA.For example,the car driving in the sea,its electronic equipment is facing the risk of high salt spray erosion,after three anti-protection treatment of PCBA can effectively resist corrosion and protect the stable operation of the electronic system.
Automotive PCB assembly processing process is a complex and delicate system engineering,involving multiple links and key technologies.In the future, with the continuous progress of automotive electronics technology,automotive pcb assembly processing process will continue to optimise and innovate,bringing more surprises and possibilities for the automotive industry.