The phenomenon of PCB tin explosion refers to the occurrence of tin explosion and ejection at the junction of solder joints and soldering materials during the soldering process of PCB (printed circuit board). Specifically, when the high-temperature soldering iron tip or soldering heat source comes into contact with the solder wire or solder paste, if the soldering material, PCB board, or related components are affected by moisture, contain excessive impurities, or improperly use soldering flux, high pressure or bubbles may be generated during soldering, causing the solder material to explode and eject small solder beads.
The phenomenon of pcb tin explosion is usually accompanied by a sound of explosion, leaving bright colored small tin beads around the welding area. These tin beads not only affect the aesthetics of welding, but may also have adverse effects on the electrical connections of circuits, such as causing short circuits or reducing the mechanical strength of welding points.
The main reason for the phenomenon of tin explosion is that the viscosity of the flux is low, which cannot effectively slow down the evaporation rate of the solvent. When the solvent in the flux evaporates on the surface of the PCB,it will cause a decrease in the temperature of the board surface,which in turn causes the air in contact with the PCB board to condense and form mist,which accumulates on the board surface.When these mists come into contact with high-temperature soldering,the moisture inside will quickly evaporate and spread.If the PCB is not kept at an appropriate angle when immersed in solder, causing the vapor to not spread smoothly,a strong driving force will be formed, leading to solder explosion.
In addition, if the humidity in the working environment is high, the probability of tin explosion will significantly increase. When performing automatic soldering, if the preheating temperature is insufficient, the condensed moisture on the PCB cannot be completely evaporated. When it comes into contact with high-temperature soldering, it can also cause tin explosion.
The main reasons for solder flux explosion and tin splashing during tin wire soldering are as follows: Firstly, this situation is more likely to occur when the angle between the tin wire and the solder nozzle is close to 90 degrees,or when the rosin used is not of the cleaning free type.Secondly, the high temperature on the surface of the welding head is also an important factor.Generally,the usage temperature of lead-free tin wire should be maintained between 320-360 ℃, which is more suitable. In addition, the specific content of flux,the temperature setting of the soldering iron,and the choice of operation method are all crucial, as these factors may affect the stability of the solder wire during the soldering process, thereby increasing the risk of flux explosion and tin splashing.
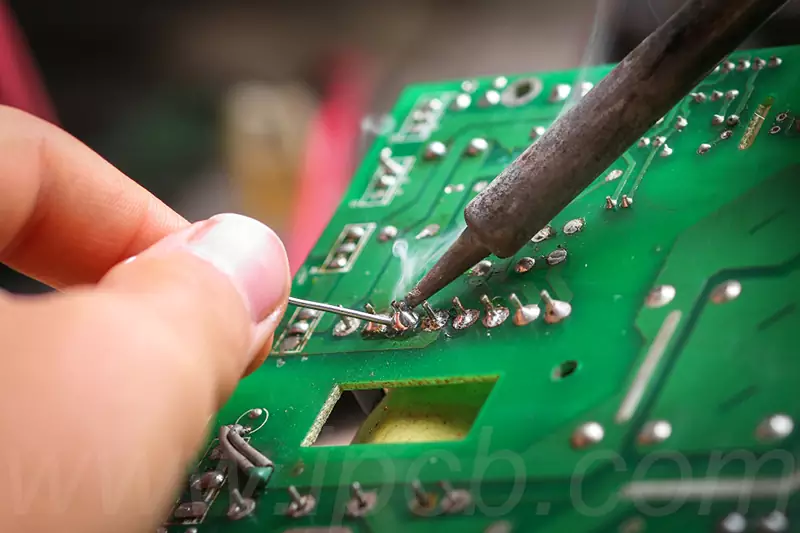
Resolvent:
During the production of solder wire, the content of flux can be appropriately reduced to lower the internal moisture content. But the premise of this approach is that after reducing the flux content, the solder wire can still maintain good solderability and firmness, as the quality of the solder wire ultimately depends on the soldering effect.
To prevent solder wires from getting damp,storage measures should be strengthened,including controlling the temperature and humidity of the storage environment to ensure that the storage or working environment remains dry.
In the production process of solder wire,it is necessary to strengthen inspection and control measures to prevent cracked solder wire from flowing into the drawing process. Once cracks are found in the solder wire,the cracked area should be immediately cut off and disposed of.
The phenomenon of PCB tin explosion is a complex and highly valued issue.In order to effectively reduce and prevent the occurrence of tin explosion, we should take comprehensive measures to ensure the safety of circuit boards