Circuit board etchant is a chemical reagent essential to the production process of printed circuit boards, mainly used to remove the copper foil portion of the printed circuit board that does not need to be retained, so that the circuit board to form the desired circuit pattern.
Common circuit board etchant
Alkaline circuit board etchant
In an alkaline environment, copper ions are prone to precipitate as copper hydroxide. To inhibit precipitation, sufficient ammonia is added to form an ammonia-copper complex ion group. This not only prevents precipitation, but also allows the original and continuously dissolved copper to form an extremely stable complex of ammonia-copper ions in solution. This divalent ammonia-copper complex ion acts as an oxidising agent, causing the oxidation and dissolution of the zero-valent copper metal. However, a monovalent cuprous ion is formed during the redox reaction. Alkaline etching reaction of the intermediate state of cuprous ion solubility is extremely low, with the help of ammonia, ammonia ions, and a large amount of oxygen in the air, so that it is further oxidised to soluble divalent copper ions, and then converted to the oxidising agent for copper etching, and so on, and continue to etch the copper, until the reaction slows down as a result of too much copper. Therefore, the general etching machine exhaust system, in addition to discharging the ammonia odour, but also provide fresh air to accelerate the copper etching process.
Adding ammonia to the copper chloride solution results in a complexation reaction with the chemical equation CuCl₂ + 4NH₃ → Cu(NH₃)₄Cl₂. When etching, the copper on the substrate is oxidised by the [Cu(NH₃)₄]²⁺ complex ion, and the etching reaction is: Cu(NH₃)₄Cl₂ + Cu → 2Cu(NH₃)₂Cl. The [Cu(NH₃)₂]¹⁺ generated does not have the ability to be etching . Under the action of excess ammonia and chloride ions, it can be rapidly oxidised by oxygen in the air, generating [Cu(NH₃)₄]²⁺ complex ions with etching ability, and the regeneration reaction is as follows: 2Cu(NH₃)₂Cl + 2NH₄Cl + 2NH₃ + 1/2O₂ → 2Cu(NH) ₃)₄Cl + H₂O. Therefore, ammonia and ammonium chloride (i.e., sub-liquid) need to be constantly replenished during etching.
Acidic circuit board etchant
Acidic circuit board etchant agents include hydrochloric acid, hydrochloric acid + sodium chlorate, hydrochloric acid + hydrogen peroxide, and other processes. Acid etching waste liquid mainly contains CuCl₂, HCl, NH₄Cl or NaCl and other components, copper content of 100 – 145g / L, acidity 1 – 4N, density 1.2 – 1.4g / ml. This type of acidic etching solution is widely used because of the side of the etching of a small, easy to control the rate, easy to regenerate and other characteristics.
During the etching process, Cu²⁺ acts with Cu to form Cu⁺. As the etching reaction advances, the amount of Cu⁺ increases, Cu²⁺ decreases, and the etching capacity of the etching solution decreases rapidly. In order to maintain stable etching capacity, need to add oxidant or drum into the air, prompting Cu⁺ as soon as possible into Cu ² ⁺, at the same time, when the etching cylinder Cu ² ⁺ concentration reaches a specific value or etching cylinder solution more than a specific volume, need to discharge part of the etching liquid in a timely manner, to ensure that the etching process is normal. The discharged liquid is called etching waste liquid.
Acid etching
Acidic circuit board etching agent mainly hydrochloric acid, hydrochloric acid + sodium chlorate, hydrochloric acid + hydrogen peroxide and other processes. Acid etching waste liquid mainly contains CuCl₂, HCl, NH₄Cl or NaCl and other components, copper content of 100 – 145g / L, acidity 1 – 4N, density 1.2 – 1.4g / ml.
Acidic circuit board etchant is widely used because it has the characteristics of small side etching, easy rate control and easy regeneration. During etching, Cu²⁺ interacts with Cu to form Cu⁺. As the etching reaction advances, the amount of Cu⁺ increases, Cu²⁺ decreases, and the etching capacity of the etching solution decreases. In order to maintain stable etching capacity, need to add oxidant or drum into the air, so that Cu⁺ as soon as possible into Cu²⁺. When the concentration of Cu²⁺ in the etching cylinder reaches a specific value or the solution exceeds a specific volume, it is necessary to discharge part of the etching solution in time, i.e. the etching waste solution.
Related reaction formula:
Cu²⁺ + Cu → Cu⁺
6Cu⁺ + NaClO₃ + 6H⁺ → 6Cu²⁺ + NaCl + 3H⁺ → 6Cu²⁺ + NaCl + 3H₂O → 6Cu²⁺ + 6HClO ₃ + 6H⁺ → 6Cu²⁺ + NaCl + 3H⁺ → 6Cu²⁺ + NaCl + 3H₂O → 6Cu²⁺ + NaCl + 3H₂O → 6Cu²⁺ + NaCl + 3H⁺ → 6Cu²⁺ + NaClO₃ + 6H⁺ → 6Cu²⁺ + NaClO₃ → 6Cu²⁺ + NaCl + 3H₂O → 6Cu² ⁺ + NaCl +3H₂O
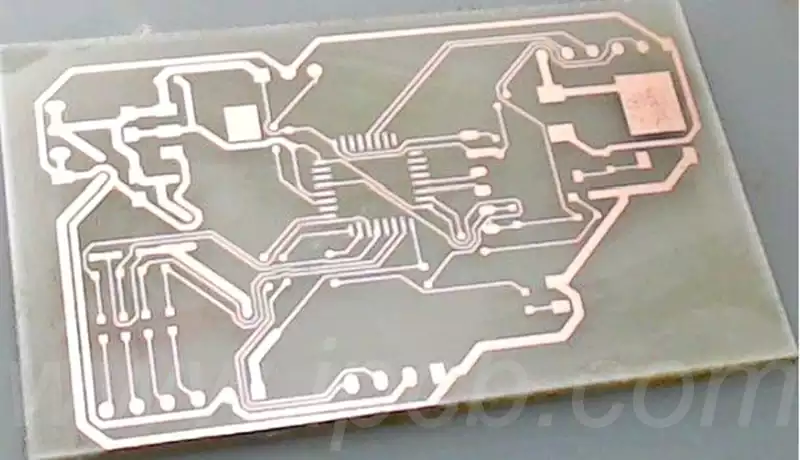
Methods of operation and practical tips
Selection of etchant and optimisation of parameters for circuit board etching
In order to ensure that the etching effect reaches the best state, the rational selection of circuit board etchant is a key prerequisite. In practice, the etching time and solution concentration can be dynamically adjusted through the test piece test method, so as to accurately match the process requirements and achieve high-quality etching.
Temperature control points
During the etching process, the temperature of the solution should be strictly monitored, and it is recommended to maintain it in the range of 20~30°C. Too high a temperature may cause the reaction rate to go out of control. Too high a temperature will easily cause the reaction rate to go out of control, while too low a temperature may cause reaction hysteresis, both of which will significantly reduce the etching accuracy.
Post-treatment and Cleaning Specifications
After the etching is completed, the residual etchant should be removed in time. Recommended use of dilute acid or alkaline solution for neutralisation and cleaning, the operation should grasp the cleaning intensity, to avoid damage to the circuit board substrate due to over-processing.
Etchant storage management
In order to protect the stability of etchant performance, the need to use sealed, light, moisture-proof storage environment, reduce contact with the air. At the same time, an expiration date management system should be established to avoid the failure of the active ingredient due to long-term storage.
Circuit board etchant as an indispensable key material in the field of electronic manufacturing, its performance and operation are directly related to the quality of the circuit board and production efficiency. With the rapid development of electronic technology, the performance of printed circuit boards is increasingly demanding, etchant technology is also constantly innovating and progressing. In the future, we look forward to seeing more efficient, environmentally friendly, low-cost etchant products, contributing to the sustainable development of the electronics manufacturing industry.