What is continuous tin? Continuous tin refers to the soldering of circuit board pads on the solder joints after the emergence of two and more solder joints. Pins of the solder connected to the phenomenon. Even tin is simply understood as solder has a connection, is a process abnormality. Defects, manifested in excessive solder bridges. Lianshi defects can appear in the THT process, can also appear in the SMT process.
Reasons for wave soldering with tin:
- High solder temperature: high temperature will make the solder fluidity enhancement, easy to form a continuous tin.
- Insufficient preheating: If the PCB board is not sufficiently preheated, the temperature of the pads and component feet will be lower than the temperature of the solder, resulting in excessive flow of solder.
- Too much flux or poor quality: excessive flux or low-quality flux will lead to increased solder fluidity, easy to form a continuous tin.
- Improper wave height: the wave is too high will increase the contact area of the solder, increasing the risk of tin.
- unreasonable pad design: such as pad spacing is too small, the shape of the pad is not suitable for automatic welding.
- Inaccurate placement of components: component feet away from the centre of the pad, resulting in the flow of solder in the cooling to the wrong location.
- Solder contains impurities: impurities in the solder will affect its fluidity and adhesion, resulting in continuous tin.
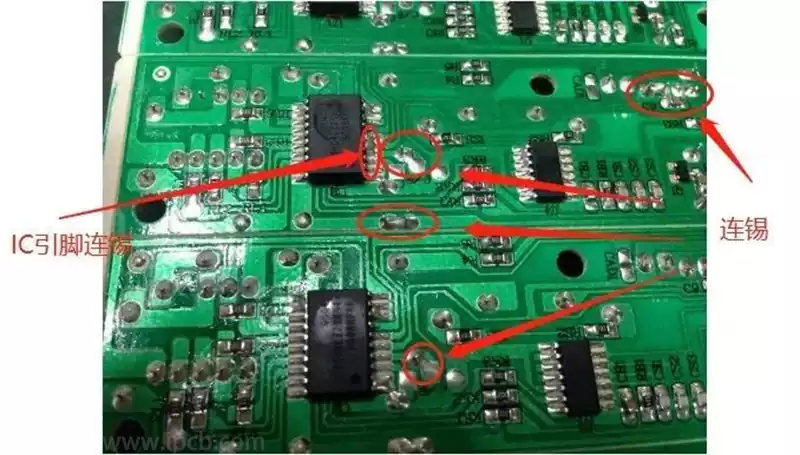
PCBA wave soldering tin problem solution:
- Optimise the welding process settings: by reasonably adjusting the welding temperature. Wave height and welding cycle and other parameters to shorten the wetting time and reduce the degree of wetting, and then avoid the solder in the component solder joints produced even tin phenomenon.
- Replacement of solder alloy materials: consider the use of better wetting and fluidity of the solder alloy to enhance the stability of the soldering process, thereby reducing the risk of tin.
- Replacement of component types: for those poor wettability. Easy to trigger even tin components, try to choose a better welding performance of the components to replace.
- Review the PCB board and component surface treatment: PCB board and component surface treatment may also lead to improper tin, so we need to carefully check whether there is oil. Oxidation and other issues, and timely cleaning and processing.
- Comprehensive inspection of equipment: need to carry out a comprehensive inspection of wave soldering equipment to confirm the existence of such as solder bath temperature fluctuations. Wave height uneven and other faults, once the problem is found, should immediately repair or replace the equipment.
Reflow soldering continuous tin causes and preventive measures
Improper line design: If the soldering point is too dense or unreasonable design, it may lead to continuous tin.
Countermeasures: Reasonable planning of PCB lines to ensure that the number of solder joints, area and symmetry are properly handled.
Pollutant impact: PCB pads or residual pollutants in the surrounding environment is another cause of even tin.
Preventive measures: strengthen the cleaning work, and ensure that the working environment to achieve a certain standard of dust prevention.
Insufficient preheating and flux problems: preheating temperature is not enough or flux activity is not enough, will lead to fluid viscosity is too large, thus triggering even tin.
Solution: Strictly control the preheating temperature, time and flux activity.
Solder Paste Printing Problems: Insufficient printing parameters or precision may lead to solder paste offset or bridging, which in turn leads to the formation of continuous tin in reflow soldering.
Countermeasure: Make appropriate adjustments to the solder paste printing machine to optimise the printing parameters and accuracy.
Continuous tin problems may lead to circuit short-circuit, chip burning and other serious consequences, although in a variety of inspection processes can be found and rework, but the high rate of tinned still need to be analysed in depth and take appropriate measures to solve the cause.