Circuit boards are classified according to their self-extinguishing time after fire ignition, and are usually classified into three grades: UL94 V-0, UL94 V-1, and UL94 V-2.
- UL94 V-0 rating
UL94 V-0 is the highest flame retardant rating, requiring the specimen to self-extinguish in no more than 10 seconds, including materials and circuit boards after the combination of the specimen. This rating applies to circuit boards with very high safety requirements, such as computer motherboards. - UL94 V-1 rating
UL94 V-1 rating requires the specimen to be self-extinguishing for no more than 30 seconds, and is also applicable to circuit board products with high safety requirements. - UL94 V-2 rating
UL94 V-2 rating requires a self-extinguishing time of no more than 60 seconds, and is suitable for circuit boards with general safety requirements.
The evaluation of the flame retardancy of circuit boards is based on the UL94 standard. The test method covers both horizontal and vertical test situations.
In the horizontal test, the board is suspended at a height of 50 mm above the floor and a flame is then forced underneath it. If the circuit board burns during the test, the test is terminated; if it extinguishes itself, the self-extinguishing time is recorded.
In the vertical placement test, the circuit board and related materials are also tested. During the test, the flame starts contacting from the bottom of the specimen and burns continuously at the top of the specimen for 10 times, with an interval of no more than 5 seconds between each burning. If the circuit board is ignited during the test and the burning time exceeds the specified range, or if it continues to burn or drip burning material before it is extinguished, or if the total burning time exceeds 250 seconds, the test is judged to have failed.
Types and Uses of Flame Retardants
Flame retardants, as a class of chemical substances capable of interfering with the combustion reaction process of polymers or achieving flame retardant effects by adjusting the combustion conditions, can be mainly divided into the following types:
Halogen flame retardants: In view of the large amount of toxic gases generated during combustion, they have been gradually discarded by the market in recent years.
Phosphorus flame retardants: their mechanism of action is to generate non-combustible gases and form a charcoal layer, so as to achieve the purpose of flame retardancy.
Nitrogen-based flame retardants: achieve flame retardancy by releasing non-combustible gases and lowering the combustion temperature.
Inorganic flame retardants, such as aluminium hydroxide and magnesium hydroxide, are flame retardant through heat absorption and the formation of carbon layers.
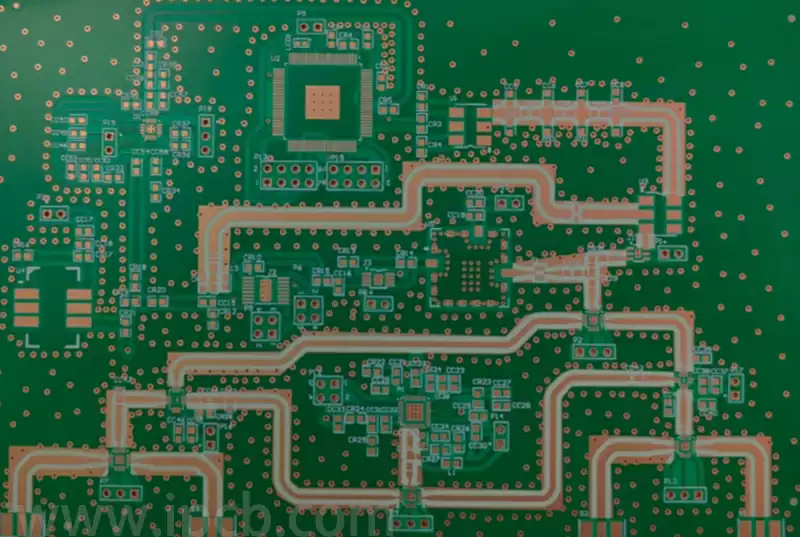
Flame Retardant Principles
The flame retardant principle of flame retardants mainly covers the following aspects:
Gaseous phase flame retardant principle: The oxygen concentration is diluted by the production of non-flammable gases, thus slowing down the combustion reaction.
Cohesive phase flame retardant principle: Forms a carbon layer or other physical barrier on the surface of the material to impede the transfer of heat and oxygen.
Interrupted Heat Exchange Flame Retardant Principle: Using the heat absorption reaction of chemical substances to reduce the temperature of the material, thus preventing the continuation of combustion.
Selection of Flame Retardant and its Impact
When selecting a flame retardant, it is important to thoroughly consider its possible effects on the resin system and the performance of the base material product. For example, nitrogen-containing resin matrices may become brittle as a result of the addition of flame retardants, whereas the release of moisture from hydrates at relatively low temperatures may lead to delamination of the laminate. Therefore, when selecting flame retardants, preference should be given to reactive flame retardants, which are able to incorporate into the polymer backbone by chemical bonding and thus have less impact on material properties.
Commonly used flame retardants include:
Aluminium hydroxide (ATH): reduces the concentration of flammable gases by generating water vapour and simultaneously forms a carbon layer to achieve flame retardancy.
Melamine derivatives: such as melamine polyphosphate (MPP), which produces combustible gases and char during decomposition.
Nitrogen-containing resins, such as phenylpropazine and melamine phenolic varnishes, which have high reactivity and high glass transition temperatures (Tg).
Phosphorus-containing resins and hardeners: e.g. DOPO, which offer high decomposition temperatures and Tg values, but may have some effect on the other properties of the material.
The evaluation and enhancement of flame retardant properties of circuit boards is an important part of ensuring the safe operation of electronic equipment. With the continuous development of material science and process technology, flame retardant technology will play a more critical role in the field of circuit boards, providing solid support for the stable operation of electronic equipment.