In the production of flex board, material deformation and delamination are important factors affecting product quality. In order to avoid such problems, the following detailed coping strategies can be adopted:
Substrate selection
The choice of material directly determines the basic bending performance of flex board. In terms of substrates, polyimide (PI) and polyester (PET) are commonly used insulating materials, in which the PI substrate by virtue of the unique molecular chain structure, with excellent flexibility and temperature resistance, can withstand frequent bending and not easy to be damaged, and the number of times of its bending resistance can reach more than 100,000 times, which is widely used in the scene of the high demand for bending performance; PET substrate, although the cost is lower, but flexibility and durability is relatively inferior, usually applied to products with less bending needs. PET base material, although the cost is lower, but the flexibility and durability of the relative inferior, usually applied to the bending of less demanding products. In terms of conductive materials, calendered copper foil is cold rolled and has good ductility and fatigue resistance, and its grains are arranged in a fibre-like manner, which can better disperse stress during bending, making it more suitable for frequent bending applications than electrolytic copper foil; the thickness of the copper foil also affects the bending performance, with thinner copper foils (e.g., 12μm – 35μm) being easier to bend, while thicker copper foils will increase rigidity and reduce bending flexibility. Thinner copper foils (e.g. 12μm – 35μm) are easier to bend, while thicker copper foils increase rigidity and reduce flexibility. In addition, the flexibility and bonding strength of the binder is also critical. If the binder is unable to deform synchronously with the substrate and the copper foil during the bending process, it may lead to separation of the layers and affect the overall performance.
Material Storage and Pre-treatment
Materials should be stored in a dry, constant temperature environment to prevent deformation caused by moisture and temperature fluctuations. Before being put into the SMT production line, flex board usually needs to be pre-baked to slowly expel the absorbed moisture and prevent delamination, blistering and other undesirable phenomena under the impact of high temperature of reflow soldering. Pre-baking conditions are generally 80-100 ℃, lasting 4-8 hours, under special circumstances can be increased to 125 ℃ or more, but need to shorten the baking time accordingly.
Lamination process control
Accurately control the temperature, pressure and time during the lamination process to ensure that the conductive layer is tightly bonded to the flex board. The use of high quality semi-cured sheets and laminating adhesives can improve the quality of lamination and reduce the risk of delamination. Hot presses are commonly used for laminating equipment and are heated by steam, thermal media (oil) and electricity. Steam heating is less costly, but the temperature is usually 160°C; electric heating can reach over 300°C, but the temperature distribution is uneven; heating with silicone oil as the medium can reach 200°C and the temperature distribution is even. Vacuum press is the ideal choice, although the equipment is expensive and slightly longer pressing cycle, but can ensure that the colloid fully fill the gaps in the circuit pattern, and improve the product qualification rate and production efficiency.
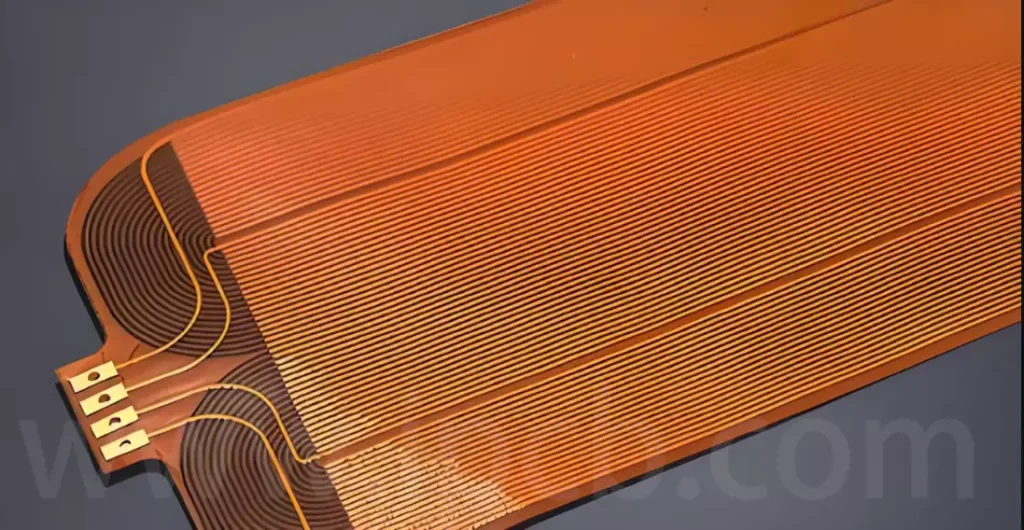
Structural design
Structural design has an important impact on the bending performance of the flex board. The rationality of the line layout is directly related to the distribution of stress, right-angle or sharp line design will form a stress concentration point, in the bending process is easy to cause line breakage; the use of curved or wavy line design, can effectively disperse the stress and extend the service life of the soft board. Multi-layer flex board layer matching should not be ignored, the thermal expansion coefficient of each layer of material needs to be as similar as possible, otherwise in the bending and temperature changes, the layer will produce shear stress, resulting in delamination phenomenon. The use of reinforcement plates need to be carefully designed, if the reinforcement area extends to the bending parts, will limit the deformation capacity of the soft board, increasing the risk of line damage; reasonable reinforcement should avoid the main bending area, only in the need to enhance the mechanical strength of the parts used, and the flexibility of the reinforcement material needs to be matched with the soft board.
Graphics transfer and etching
In the graphics transfer process, be sure to ensure the precision of the graphics and alignment accuracy, in order to avoid line open or short circuit. Etching, the etchant concentration and temperature should be uniformly controlled to reduce corrosion and deformation of the substrate. There are many factors that affect circuit etching performance, and it is necessary to continue to accumulate data to achieve high-precision etching.
Punching and plating
Accurately control the punching position and hole size to avoid excessive mechanical stress on the substrate. During the plating process, the metallisation quality of the hole wall should be ensured to prevent connection problems at a later stage. Before flex board plating, contaminants and oxidised layers on the conductor surface must be thoroughly removed to obtain a dense and strongly adherent plating layer.
Online monitoring
Multiple quality monitoring points are set up in the manufacturing process to monitor process parameters and product status in real time. Timely detection and correction of deviations and abnormalities in the production process to ensure stable product quality.
Finished Product Inspection
Strict electrical performance tests and appearance inspections are carried out on finished flex board to ensures that the line conducts well, the insulation meets the standards and there are no short circuits or broken circuits. Common inspection methods include appearance inspection, size and shape inspection, as well as electrical testing, reliability testing, and environmental adaptability testing. electrical testing of flex board comprehensively verifies the electrical performance of the flex pcb through integrated hardware systems and intelligent algorithms. In addition, AOI (Automatic Optical Inspection) is usually not suitable for FPC due to its uneven surface and high false judgement rate.
The manufacturing of flex boards is a complex systematic project to effectively avoid material deformation and delamination problems, improve the reliability and durability of flex boards, reduce the defect rate in the production process, and better ensure that the product maintains excellent performance in a variety of complex application scenarios, thus meeting the growing market demand.