Eutectic soldering, also known as low melting point alloy soldering, is a specific soldering technique. The process involves the removal of unstable oxide layers at the interface between the chip and the gold-plated base by gentle friction at specific temperatures and pressures, which causes the contacting surfaces to melt and form a liquid phase. Subsequently, when the temperature drops below the eutectic point, these grains formed from the liquid phase combine with each other to form a mechanical mixture.
Eutectic solder is a solder consisting of two or more metals with a common melting point, the most common of which is lead-tin eutectic solder. It consists of two metals with different abundances, which, in a certain ratio, will have a common melting point and form a eutectic organisation. The common composition of lead-tin eutectic solder is 63% tin and 37% lead.
Compared with other non-eutectic solder (e.g. Sn60/Pb40, melting range 183-190°C), eutectic solder has the following advantages:
- No melting range: melting directly from solid to liquid, avoiding poor soldering due to temperature fluctuations.
- Good wettability: high fluidity, can quickly fill the gap between the pads, forming a strong intermetallic compound (IMC).
- High mechanical strength: Uniform eutectic structure and better fatigue resistance than non-eutectic alloys.
The phenomenon of eutectic refers to the direct transformation of an alloy from a liquid to a solid at a relatively low temperature without going through a plastic phase. This transformation is accompanied by an equilibrium reaction between the two solids.
In solder wire, a metal alloy consisting of tin and lead is a common eutectic alloy. The solder wire with 63% tin and 37% lead is known as eutectic solder wire, or 6337 solder wire. This type of wire has a melting point of 183 degrees. When the tin content exceeds 63%, the crystallisation temperature rises, resulting in lower strength of the wire and a high overall alloy melting point. Conversely, when the tin content falls below 10%, the solder quality of the wire deteriorates, the joints become weak, and the solder lubrication properties diminish.
Characteristics of eutectic solder wire
Because eutectic solder wire can be rapidly converted from a solid to a liquid at high temperatures and does not need to undergo a semi-molten state, its melting point is slightly lower than that of non-eutectic solder wire. This characteristic reduces the possibility of damage to the soldered electronic components. In addition, eutectic wire has good fluidity. The low surface tension improves the quality of the solder joint and reduces soldering errors. Because of this, eutectic wires are widely used in the soldering process.
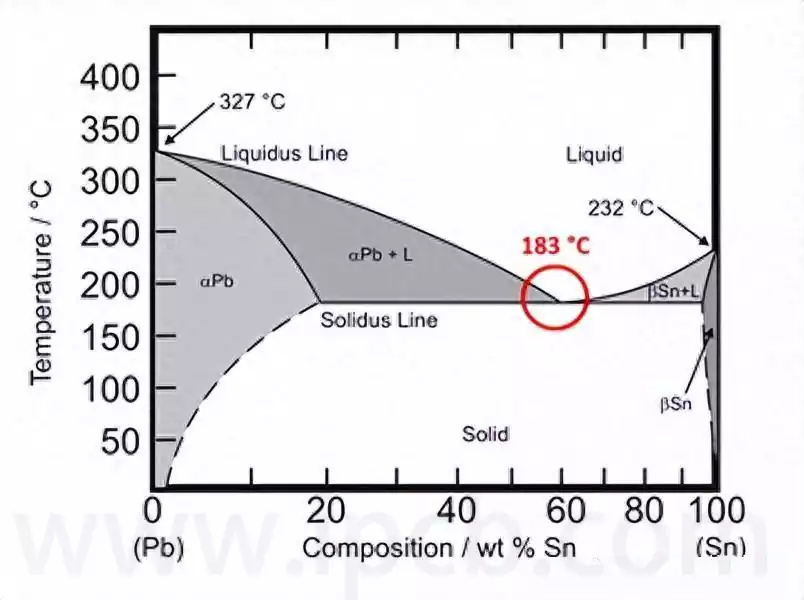
Fully automatic eutectic welding process introduction
- Fully automatic mounting principle
Differing from manual friction welding, fully automatic eutectic welding is completed through the execution of pre-written procedures and parameter settings by the equipment. Its working mechanism is based on the concept of material programming, the use of image recognition technology and coordinate system to accurately locate the target material, set the corresponding action parameters, and then realise the fully automatic eutectic welding operation.
2.Welding process
Fully automatic eutectic welding consists of a number of links: preparation of the workpiece before welding (including identification of the product assembly diagram.). Adjust the equipment clamping tools and select the appropriate chip nozzle); material preparation (such as heat sink cleaning. Wafer cutting and cleaning. Material placement and nozzle calibration); preparation of the programme (including the setting of the heating curve and welding process parameters); running the programme to complete the welding operation; and welding results inspection (the first piece of the appearance and void rate inspection, the rest of the samples for the appearance of the inspection). The action sequence of the suction nozzle is as follows: sucking and placing the heat sink, sucking and placing the soldering chip, sucking the chip for friction welding, and finally sucking the finished soldered heat sink assembly and putting it into the gel box.
- Selection of suction nozzles
In the fully automated soldering process, according to the different types of devices (e.g. microwave integrated circuits microstrip chip . Heat sink. Soldering chip. Chip and welding components) selection of the corresponding nozzle. Selection principles include high manufacturing accuracy, high temperature resistance, and size should be compatible with the soldered components. High-temperature performance, size should be matched with the device, and in the process of use shall not cause damage to the device.
Eutectic Solder Application and Environmental Challenges
- The mainstay of the electronics industry:
Used for PCB SMD soldering (SMT), chip packaging (such as BGA, QFN), because of its high reliability can reduce the risk of false soldering.
Aerospace, medical equipment and other areas with stringent requirements for welding quality are also preferred.
- Eco-friendly Substitution Trend:
Due to the toxicity of lead, the EU RoHS directive restricts the use of lead, and lead-free eutectic solder (e.g., Sn96.5/Ag3.0/Cu0.5, melting point 217°C) is gradually gaining popularity.
Lead-free solder has a higher melting point and needs to be adjusted to the soldering process (e.g. increase reflow temperature to 230-250°C).
Eutectic solder, as a key material in the field of electronics manufacturing, has long been widely used in the assembly of various types of high-precision electronic devices due to its superior soldering performance and excellent mechanical strength. However, with the increasingly stringent environmental regulations and the concept of sustainable development, lead-free eutectic solder has gradually replaced the traditional leaded solder as the industry development trend. In the future, the soldering process will continue to be optimised to adapt to the characteristics of new materials, while taking into account the dual needs of soldering quality and environmental protection. Continuous promotion of green soldering technology innovation is the way to realise the efficient, environmentally friendly and safe development of electronic manufacturing.