What is a high-Tg PCB? What are the advantages of using high Tg PCBs? When the temperature of a high Tg printed circuit board rises to a certain range, the substrate transitions from a ‘glass state’ to a ‘rubber state,’ and this temperature is referred to as the board’s glass transition temperature (Tg).
In other words, Tg is the highest temperature (°C) at which the substrate maintains its rigidity. This means that ordinary PCB substrate materials not only soften, deform, and melt, but also exhibit a significant decline in mechanical and electrical properties (I assume no one wants to see their PCB boards exhibit such issues).
Generally, boards with a Tg of 130°C or higher are considered standard, while those with a Tg greater than 170°C are classified as high-Tg, and those with a Tg greater than 150°C are considered medium-Tg. PCB printed circuit boards with a Tg ≥ 170°C are referred to as high-Tg printed circuit boards. When the substrate’s Tg is increased, the printed circuit board’s heat resistance, moisture resistance, chemical resistance, and stability characteristics are all improved. The higher the Tg value, the better the board’s temperature resistance performance, especially in lead-free processes, where high-Tg applications are more common.
High Tg refers to high heat resistance. With the rapid development of the electronics industry, particularly electronic products represented by computers, which are moving towards high functionality and high multilayer structures, PCB substrate materials require higher heat resistance as a critical guarantee. The emergence and development of high-density mounting technologies represented by SMT and CMT have made PCB increasingly reliant on the support of high heat resistance in terms of small aperture, fine line structures, and thin profiles.
Therefore, the difference between general FR-4 and high-Tg FR-4 lies in their mechanical strength, dimensional stability, adhesion, water absorption, thermal decomposition, and thermal expansion properties under thermal conditions, especially after moisture absorption. High-Tg products clearly outperform ordinary PCB substrate materials in these aspects. In recent years, the number of customers requesting high-Tg printed circuit boards has been increasing annually.
What is the difference between medium TG substrates and high TG substrates?
The primary difference between medium-TG substrates and high-TG substrates lies in their glass transition temperatures. Medium-TG substrates have relatively lower TG values and poorer heat resistance, which may allow them to function normally under non-extreme conditions but may experience performance degradation or failure under high-temperature conditions. In contrast, high-TG substrates, due to their higher glass transition temperatures, can maintain stability under higher-temperature environments, thereby offering greater advantages in specific application scenarios.
For example, if an electronic device needs to operate continuously in a high-temperature environment, a circuit board made from high-TG substrate would be more reliable than one made from medium-TG substrate, as the former can better withstand the effects of high temperatures.
In addition to differences in heat resistance, medium-TG and high-TG substrates may also exhibit variations in physical properties, mechanical strength, and electrical performance. Generally, high-TG substrates perform better in these aspects as well.
In summary, high-TG substrates, due to their excellent heat resistance and stability, offer higher reliability in harsh environments such as high temperatures and high humidity, and are therefore widely used in many high-end electronic products. Medium-TG substrates, although slightly inferior in performance, still have their applications in scenarios where material performance requirements are not stringent or cost control is strictly enforced.
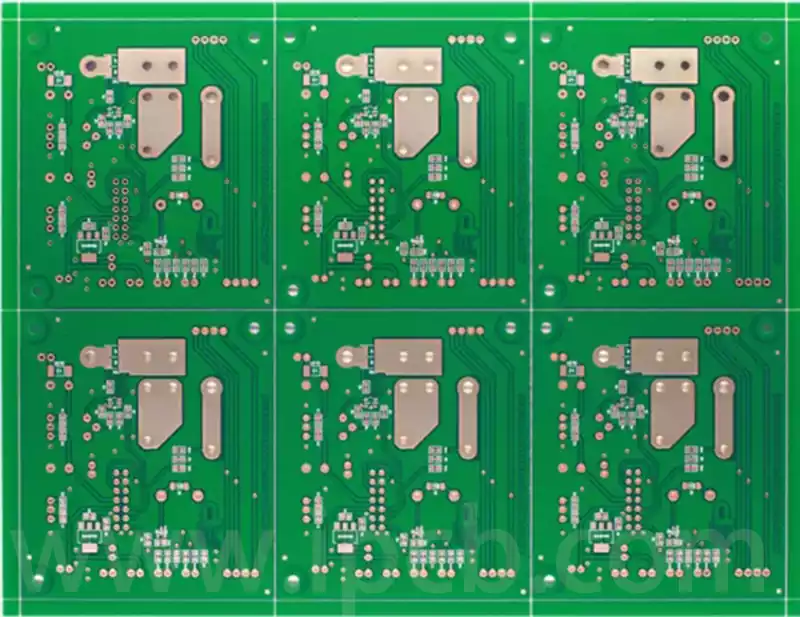
The main differences between high TG laminates and ordinary TG laminates are as follows:
a. Temperature control:
During PCB manufacturing, high TG laminate production requires higher temperature control and more sophisticated production equipment. The manufacturing process requires higher heat treatment temperatures, typically exceeding 180°C, to ensure that high TG laminates have sufficient high-temperature performance.
b. Mechanical strength:
High-TG laminates exhibit superior mechanical strength, maintaining specified mechanical properties at elevated temperatures;
c. Thermal Stability:
High-TG materials exhibit outstanding high-temperature thermal stability, including stable thermal expansion coefficients, high glass transition temperatures, and low moisture absorption rates. Their thermal expansion coefficient stability and resistance to thermal degradation surpass those of standard materials, ensuring that thermal expansion deformation does not affect the PCB circuitry.
d. High-frequency performance:
As the frequency of active components continues to increase, the demand for TG values also continues to rise. There is a significant correlation between TG values and high-frequency performance, manifested as: lower longitudinal voltage standing wave ratio (VSWR) requirements, lower signal loss caused by dielectric loss, and lower signal delay.
How to select the Tg value of PCB materials:
Whether lead-free soldering is used.
The temperature range for leaded soldering is 210–245°C, while the temperature range for lead-free soldering is typically 220–260°C.
FR4 materials have a Td value (thermal decomposition temperature), which is generally defined as the temperature at which the material loses 5% of its original mass. When the material is heated to this temperature, the chemical bonds within the resin begin to break, and volatile components are released, resulting in a reduction in resin content within the PCB substrate.
Taking Jiantou’s boards as an example, the conventional FR4 board KB-6160 has a Tg value of 135°C and a Td value of 305°C at 5% mass loss; the lead-free FR4 board KB-6168LE has a Tg value of 185°C and a Td value of 359°C at 5% mass loss.
If conventional KB-6160 boards with a Tg of 135°C are used in a lead-free processing environment, the maximum temperature can reach 260°C. Although this has not yet reached the Td value of 305°C at 5% mass loss, the board has already lost 1.5–3% of its resin mass, which directly affects the PCB’s electrical properties and may also cause issues such as delamination and voids during the soldering process.
Chip packaging density on the PCB.
When large-sized BGA-packaged chips are present on the PCB, high-Tg FR4 boards should typically be selected. This is particularly important when the board requires SMT secondary processing or multiple rework cycles.
For high-value chips, high-Tg materials, with their excellent thermal stability, can reduce cracks at the connection points between PCB traces and pads, as well as pad deformation caused by temperature changes, thereby improving the production yield of PCBA.
High-Tg materials offer higher reliability during PCB production and processing.
When the PCB’s hole spacing is less than 12 mil, using high-Tg materials can effectively reduce the wicking effect during via processing, thereby improving the production yield rate of the PCB.
Operating temperature of the PCB.
If the circuit board will operate in a high-temperature environment, materials with a higher Tg value should be selected to ensure its stability and reliability. For example, in the automotive electronics field, due to stringent requirements for the operational reliability of electronic devices under varying temperature conditions, automotive electronics PCBs typically require the use of materials with higher Tg values.
High-Tg PCB boards offer significant advantages and have widespread applications. When selecting PCB materials, the Tg value must be determined by comprehensively considering multiple factors, balancing performance and cost, to ensure product stability and reliability, thereby driving continuous progress in the electronics industry.