Custom PCB is circuit board that are designed and manufactured according to specific needs and applications. Compared to standardized circuit boards, custom PCBs can be perfectly adapted to the size, number of layers and functional requirements of a specific product to meet the diverse needs of customers. This ability to personalize designs is especially important in the rapid development of modern electronic products.
Custom pcb process
- Requirements Analysis
The first step in customizing a circuit board is to conduct a requirements analysis. At this stage, the team needs to communicate with the customer in depth to clarify the specific requirements of the circuit board, such as size, number of layers, material type and electrical performance requirements. - Design circuit diagram: To ensure the correctness of the circuit board, the circuit diagram must first be designed according to the needs of the electronic equipment.
- Selection of boards: Based on the designed circuit diagrams, suitable boards, such as FR-4 plywood or other high-temperature materials, need to be selected.
- Prototyping: This process is a key step in verifying whether the design is correct. By actually assembling and testing the prototype board, problems in the design can be found and adjusted.
- Testing and Verification
After the completion of prototyping, comprehensive functional testing and environmental testing to verify the performance and stability of the board in the actual application.Tests include electrical testing,thermal testing and vibration testing, based on test results for further design optimization. - Mass Production
Once the design documents have been prepared and approved by the manufacturer, mass production can begin. Strict quality control is required during the production process to ensure that each PCB meets the design specifications. - Post-processing and quality control
After production,the circuit boards need to undergo surface treatment, such as tin spraying and gold plating, to improve solderability and corrosion resistance. Final quality control is also required to ensure that each board meets the technical requirements. - Logistics and Delivery
The final step is the safe delivery of the finished PCB to the customer. This requires sound logistics planning to ensure that the boards are not damaged during transportation and are delivered in a timely manner.
Several types of customized PCBs exist on the market, including single-sided PCBs, double-sided PCBs, and multilayer PCBs. Each type of circuit board is suitable for different application scenarios. For instance, multilayer PCB offers higher electrical performance and complex circuit designs when space is limited. In addition, the combination of rigid and flexible PCBs demonstrates unique advantages in certain high-tech fields.
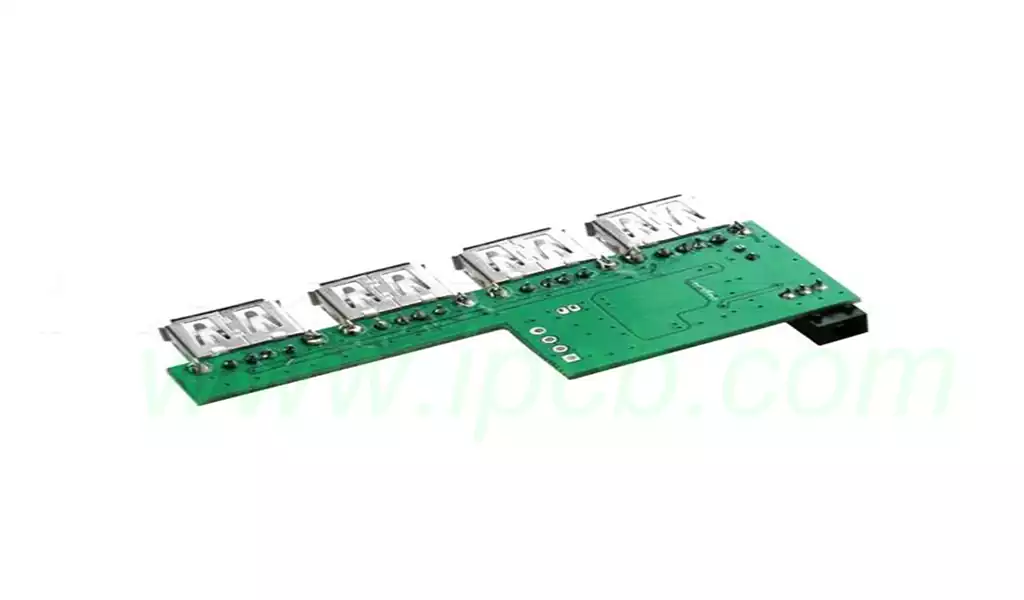
Custom PCB Multilayer Circuit Boards
PCB multilayer customization involves not only the circuit design itself, but also material selection, layer planning, and post-testing and verification. Each layer must be precisely designed to ensure smooth transmission of electronic signals while minimizing electromagnetic interference. Therefore, choosing an experienced PCB multilayer customization service provider is critical.
Our PCB multilayer customization process begins with an in-depth understanding of our customers’ needs.Through close communication with our customers, we are able to accurately grasp the functional requirements and performance specifications of the product,so that we can formulate a reasonable design plan. On this basis, we utilize advanced design software for circuit layout and simulation testing to ensure the feasibility and stability of the design.
During the manufacturing process of custom PCB multilayer circuit boards,we use high-quality raw materials combined with fine processing techniques, such as gold plating,blind buried holes,and other advanced processes,to meet a variety of complex design requirements.In addition,we emphasize on quality control during the production process,from raw material inspection to finished product testing,every step of the process is strictly controlled to ensure that every PCB multilayer circuit board delivered to our customers is of high quality.
For special applications,such as high-frequency communications or military fields,PCB multilayer customization needs to follow more stringent standards.We have the specialized team and experience to handle these difficult design and manufacturing tasks and provide our customers with products that are fully compliant with the specifications.
The key benefits of custom PCB include:
Due to their inherent outstanding reliability,these types of PCBs typically require minimal rework.
After designing and building the PCB,you can reuse the bill of materials,Gerber files,and schematics to cost-effectively fabricate another PCB.
This is useful when another prototype is needed that was not originally anticipated.
You can recycle the schematics to build a similar custom PCB in the future.
It saves design time after the board has been designed for the prototype.
The price of custom PCB varies depending on a number of factors.First, different boards and manufacturing processes result in different costs.Different production processes can lead to price differences.For example,the surface treatment process (e.g. tin spraying, gold plating, etc.) and the thickness of the board will directly affect the manufacturing cost.In addition,the number and size of holes drilled will also affect the total cost, usually the more holes drilled, the higher the cost.The level of yield also affects overhead costs;a higher yield means lower unit costs.Secondly,before customizing PCB boards, we need to understand the design requirements of the board,the more complex the design will require more time and resources for design and development. Lastly, the quantity and lead time for PCB board customization will also have an impact on the price, as small quantities may require additional handwork.
Custom printed circuit board can effectively meet diverse market needs due to their nature of being designed and manufactured to specific requirements. This personalized design capability not only enhances the performance of electronic products, but also provides more possibilities for innovation and improvement. From demand analysis to the entire process of production and delivery,custom PCB is able to provide corresponding solutions for different application scenarios and functional requirements.At the same time,with the continuous development of electronic technology, the market prospect of customized PCBs will be more and more broad,driving the industry to continue to move forward.Choosing an experienced manufacturer for customization will be the key for enterprises to gain advantages in the fierce competition.