Aluminum printed circuit board refers to a kind of printed circuit board with aluminum plate as the substrate, and copper conduction lines are processed on the surface through chemical etching or mechanical processing, etc. to form a circuit board. It is characterized by good thermal conductivity, mechanical strength and stability, and is suitable for use in harsh environments such as high temperature and high pressure.
Composition
- Line layer
The line layer (usually electrolytic copper foil) is etched to form a printed circuit for device assembly and connection. Compared with the traditional FR-4, with the same thickness and the same line width, the aluminum substrate can carry a higher current. - Insulation Layer
Insulation layer is the core technology of aluminum substrate, mainly plays the function of bonding, insulation and thermal conductivity. Aluminum substrate insulation layer is the largest thermal barrier in the power module structure. The better the thermal conductivity of the insulating layer, the more conducive to the diffusion of heat generated by the device operation, but also the more conducive to lowering the operating temperature of the device, so as to achieve the purpose of improving the module’s power load, reduce the volume, extend the life of the module to improve the power output and so on. - Metal base
The type of metal used for insulating metal substrate depends on the thermal expansion coefficient of the metal substrate, thermal conductivity, strength, hardness, weight, surface condition and cost and other conditions.
Production process:
- Aluminum plate preparation
Aluminum substrate is generally selected as the base material of high-purity aluminum plate with high purity and low alumina content. First of all, it needs to be cut, annealed and other processing, made to meet the equipment and process requirements of the aluminum sheet. At the same time, it is also necessary to grind and polish the surface of the aluminum plate to ensure that the surface finish and flatness.
2.Chemical cleaning
Clean the surface of aluminum plate to remove the oil, rust and oxides, so as not to adversely affect the subsequent processing. This process step is generally used alkaline or acidic cleaning solution to ensure that the surface of the aluminum plate clean and smooth.
- Passivation
Passivation treatment is mainly the use of chemical reactions, the formation of a layer of aluminum oxide protective film on the surface of the aluminum plate, and this film structure is dense, not easy to dissolve, can be very good protection of the surface of the aluminum substrate. At the same time, it is also necessary to passivated aluminum plate polarity test to ensure the quality and reliability of the subsequent printing and coating. - Printed Coating
Printing and coating is the process of printing specific coatings on aluminum substrates to form circuit patterns. This process requires the operation of a printing press stand, which prints the coating on the surface of the aluminum plate in a liquid state to form a metallized pattern, and then dries the coating through baking and other process steps to create the circuit pattern. - Alignment
An alignment is a line formed with conductive material in a circuit board for a specific circuit connection. This is the process of converting the circuit pattern into an actual circuit that can be used, and requires the use of bare copper foil to be pasted onto the printed circuit pattern to form the surrounding circuit pattern. Soldering is required after the alignment is completed to ensure the quality of the circuit connection. - Copper sinking
Copper is the bare copper foil on the aluminum substrate electrochemical plate copper process, the deposition of a layer of copper plating. This process requires attention to control the thickness and uniformity of the copper deposited to ensure that the parasitic capacitance,parasitic inductance and other performance indicators to meet. - Drilling
Drilling is mainly to drill holes in the circuit board to lead out the wires between the circuits.This process generally use machines or lasers to drill holes in the circuit board, but also need to remove the paint at the drill holes to facilitate the subsequent circuit connections. - Plug-in
Plug-in is the electronic components into the aluminum substrate on the link,most of this work link is to use the plug-in machine, the electronic components into the circuit board holes.After the completion of the plug-in needs to be tested to ensure that all electronic components are well connected. - Surface treatment
Surface treatment is the last link,mainly coated with a protective layer to protect the entire circuit board. Usually use spraying or printing to ensure that the surface of the circuit board is clean,smooth and beautiful.
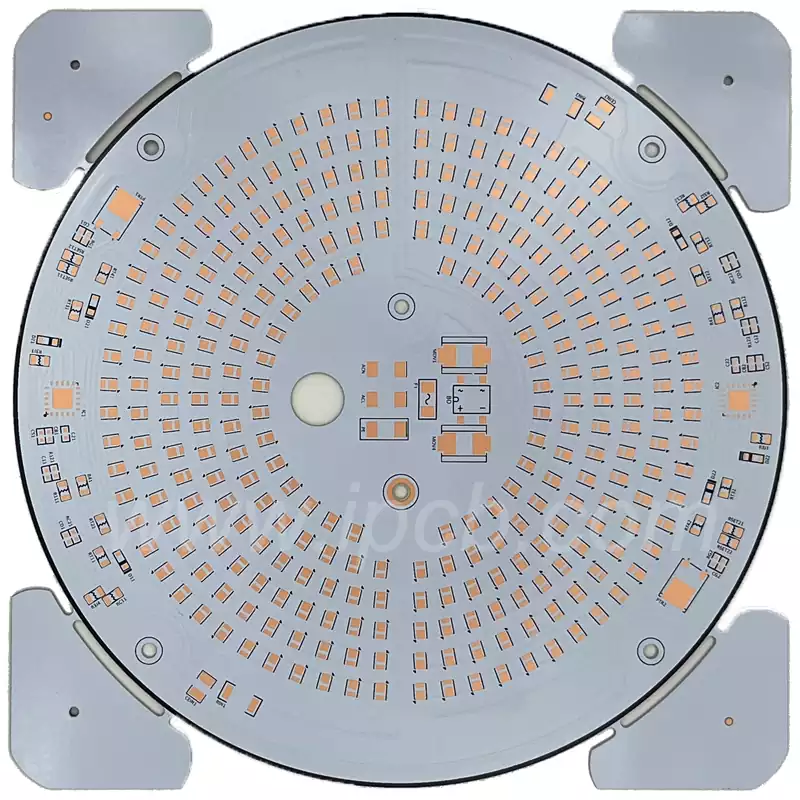
Aluminum substrates can be divided into the following categories:
Single Panel
Single panel is a single-sided treatment of aluminum base material into a substrate,its corrosion resistance is poor, suitable for some occasions that do not require high corrosion resistance requirements.
Double-sided plate
Double-sided plate will be aluminum base material double-sided treatment into the substrate, longer service life, better corrosion resistance, can be applied to some of the higher corrosion resistance requirements of the occasion.
Blind Hole Plate
Blind vias are circuit boards formed by insulating the aluminum base material on the surface, and then coppering, drilling, and laminating, etc. They are suitable for high-density circuit design.
Disadvantages of Aluminum Substrates
1. Higher cost: compared with other commodities, the price of aluminum substrate accounts for more than 30% of the product price.
2. Usually can only do a single panel, do double-sided board process is difficult.
3. Made into products in the electrical strength and pressure resistance is more likely to have problems.
4. Aluminum-based pressure resistance indicators in the board will easily cause substandard.
5. Thermal conductivity test methods and test results of the mismatch.
6. Aluminum substrate material specifications are not unified, the CPCA industry standards, national standards, international standards.
7. The thickness of copper foil is not up to standard, which will lead to burning circuits and so on.
8. More and more substandard products, cutting corners, substituting the best for the best, and stealing the best.
Aluminum printed circuit boards excel in high-temperature and high-pressure environments due to their excellent thermal conductivity and stability. However, high cost, manufacturing difficulties, and material specifications still need to be addressed.