Dip soldering is a welding method, mainly used in the plug-in process and SMT red rubber surface, it will be pre-inserted components of the printed circuit board immersed in the molten state of the solder, so as to complete the circuit board on all the soldering points of the welding.
The method is mainly used for early TV motherboards and other large area of the circuit board welding, as a substitute for high wave machine, reduce the amount of tin slag, and the board surface is heated evenly, the deformation is relatively small.
It can be done manually or automatically by machine. It is also divided into manual dip soldering and mechanical automatic dip soldering two kinds.
Manual dip welding is held by a person clamping the inserted PCB, manually complete the dip tin method, the operation process is as follows:
- heating so that the tin furnace in the tin temperature control in the 250-280 ℃; between;
- On the PCB board coated with a layer (or dip a layer) flux;
- Clamp the PCB with a fixture immersed in the tin furnace, so that the pad surface and PCB board contact, dip the thickness of tin to the PCB thickness of l / 2 ~ 2 / 3 is appropriate, dip the tin time of about 3 to 5 seconds;
- PCB board and tin surface at an angle of 5 to 10 ℃ so that the PCB away from the tin surface, slightly cooled to check the quality of welding. If more solder joints are not welded, to repeat the immersion tin once, only a few bad solder joints on the board, can be used to manually patch welding. Note that often scrape the surface of the tin furnace slag, to maintain a good welding condition, so as not to affect the cleanliness of the PCB due to the generation of slag and cleaning problems.
Manual dip soldering is characterized by: simple equipment, less investment, but low efficiency, welding quality and operator proficiency, easy to leak soldering, soldering with patch PCB board is difficult to achieve good results.
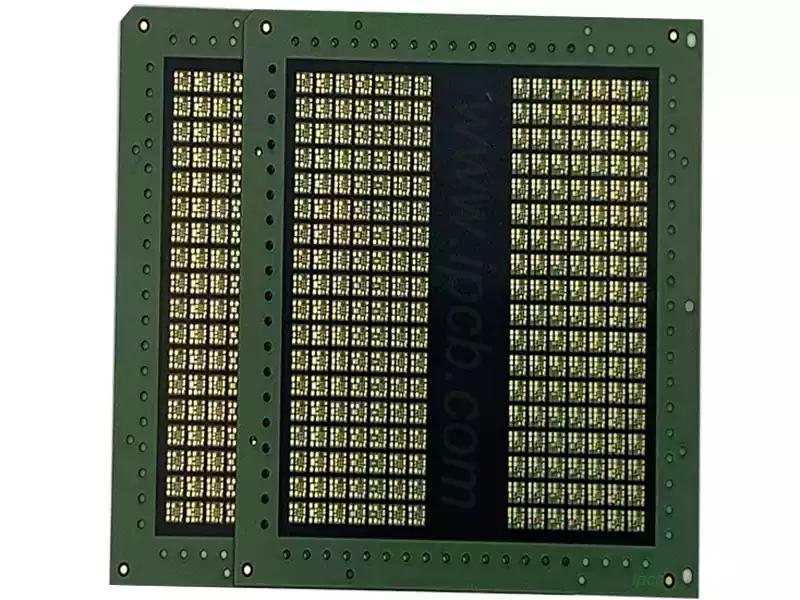
Automatic dip soldering
- Process: automatic dip welding process, the insertion of good components of the printed circuit board with a fixture installed on the conveyor belt.First sprayed with foam to help welding, and then dried with a heater, and then placed in a molten tin pot for welding, to be cooled and solidified tin and then sent to the shearer to cut off excess pins.
- Automatic dip soldering equipment
Ordinary dip soldering machine in the dip welding, the vibration head mounted on the fixture of the printed circuit board, so that the circuit board immersed in the tin pot to stay 2-3 seconds, turn on the vibrator vibration for 2-3 seconds, so that not only vibration off excess solder, but also to make the solder immersed in the interior of the welded joints to reduce welding defects.
Ultrasonic welding machine is through the tin pot radiation ultrasonic waves to enhance the effect of immersion tin, so that the welding is more reliable, suitable for general immersion tin more difficult components immersion tin.Generally consists of ultrasonic generator, transducer, water tank, solder tank, heating equipment and other parts.
Precautions for dip soldering
The correct use of flux: flux activity and concentration directly affect the quality of welding. If the flux activity is too strong or concentration is too high, in the PCB board immersion soldering over the tin, will cause parts of the foot of the solder residue too much, not only waste of flux, but also will cause a waste of solder. If the flux is too thin, it will cause bad tin eating, poor soldering and so on.
When mixing flux, generally the first flux to try the original sample, and then gradually add diluent, until then add diluent welding effect will deteriorate, and then slightly add flux, and then try again until the best results. At this time, the specific gravity meter to measure its specific gravity, and then blend according to this value can be.
In addition, in the work process, because the flux is often closer to the tin furnace, easy to cause the flux in the diluent volatilization, so that the concentration of flux. So you should always measure the specific gravity of the flux, and add diluent blending at the right time.
PCB plate immersed in flux can not be too much, try to avoid PCB plate surface touching the flux. Normal operation should be: flux dip and parts foot 2/3 or so can be. Because of the specific gravity of the flux, compared to the solder is much smaller, so the parts of the foot immersed in the tin, flux will follow the parts of the foot pushed up until the electronic component surface.If immersed in too much flux, will not only cause the flux residue on the tin liquid,affecting the quality of the tin liquid,and will cause the PWB board anyway,there are a large number of flux residue on the surface. If the flux is not enough resistance performance, or in the event of moisture absorption in a humid environment,easy to cause conductive phenomenon, affecting product quality.
The specific gravity of tin and lead is different.Manual type furnace is a static furnace,a long time of liquid static will make the separation of tin and lead, affecting the welding effect. Therefore, it is recommended that in the process of using the tin liquid should be stirred frequently (about every two hours or so stirring can be).This will make the tin-lead alloy fully integrated to ensure the welding effect. In addition, when adding a large number of tin bars,the local temperature of the tin liquid will drop, and work should be suspended. Wait for the temperature of the tin furnace to return to normal and then start working.It is best to have a thermometer to measure the temperature of the tin liquid directly.
The characteristics of dip welding include:
- Good reliability and sealing:As the joints are completely fused, there are no obvious cracks and pores, the joints are of high quality, effectively preventing the outside world, such as water vapor and impurities, from entering the inside of the joints.
- Higher processing and equipment requirements: Dip welding needs to be carried out in the molten state, so the adjustment and control of the welding equipment requires fine, as well as precision processing of the joints.
- Poor environmental protection: the intermediate metals usually used are tin, lead and other hazardous substances, which will produce environmental pollution. Internationally, the use of materials containing lead has been gradually banned.
- Simple structure: the working principle of the dip soldering equipment is to complete the welding by horizontal contact with molten lead and tin solder, by the temperature, time and depth of dip soldering control solder, by the size of the pad and the thickness of the component pins to determine the solderable area and the formation of solder joints.
Dip soldering technology plays a key role in circuit board soldering, but the operation also needs to be careful and cautious. With the improvement of environmental awareness, this technology can continue to innovate and realize a more efficient and environmentally friendly soldering method, contributing to the sustainable development of the electronics manufacturing industry.