Automatic soldering is the process of welding using automated equipment and robots. Automated welding offers significant advantages over manual welding. Due to the precision and stability of automated equipment, automated welding can significantly improve the consistency and quality of welds. This means that consistent quality is maintained in every welded joint, which reduces the likelihood of defects and rework.
Types of automated soldering:
Laser welding
Laser welding is a method of welding that utilizes a high-energy laser beam as a heat source. The laser beam is characterized by high energy density, high speed and high accuracy, enabling fast, high-quality welding. Laser welding is suitable for welding thin sheet metals and precision parts, and is especially widely used in industries such as automotive, electronics and medical devices.
Gas Shielded Welding
Gas shielded welding is also known as inert gas shielded welding, and commonly used inert gases include argon, helium or carbon dioxide. This welding method prevents oxidation and nitriding through the shielding gas used to isolate the welding area,ensuring the quality of the weld. Common gas shielded welding are argon arc welding, argon shielded MIG welding and TIG welding.
Resistance welding
Resistance welding is a method of melting metal and forming welded joints through the resistance heat generated by the current passing through the contact points. Common resistance welding methods include spot welding, seam welding and butt welding. Resistance welding is suitable for mass production, such as automobile manufacturing, household appliances and other industries.
Plasma Arc Welding
Plasma arc welding is a welding method that utilizes a plasma arc as a heat source. In plasma arc welding, the arc is compressed into a fine plasma arc with high temperature and high energy density. This method is suitable for welding of thick plate metals and refractory metals, such as stainless steel and nickel-based alloys.
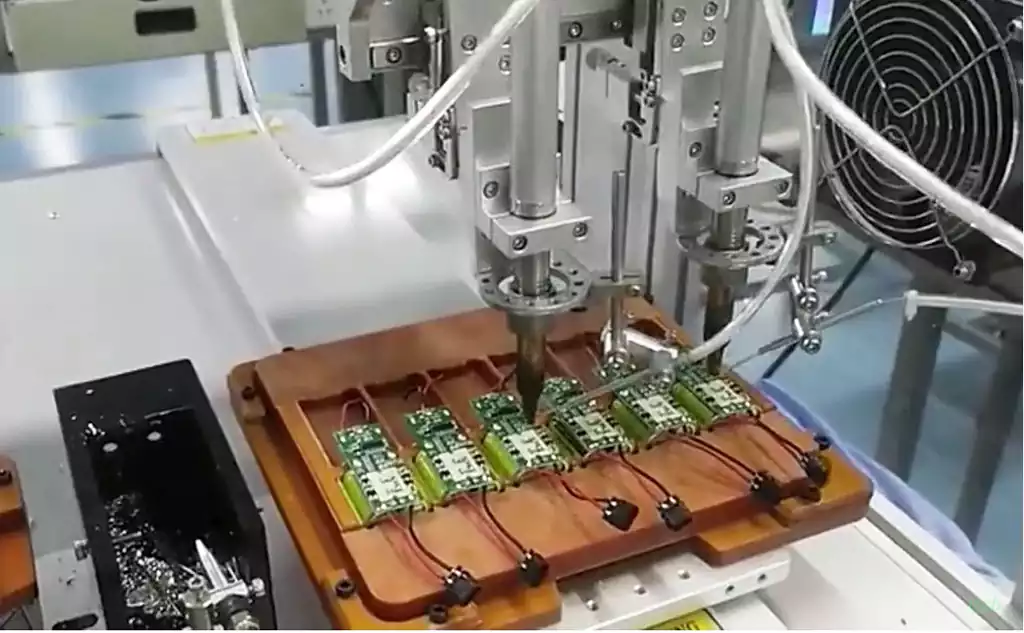
Automated welding equipment in operation should pay attention to what?
- Environment: the environment in which the enterprise carries out welding work is generally in the production workshop, and there will be other large-scale equipment in the production line. In the automatic welding equipment around as far away as possible from large vibration equipment, so as not to affect the welding accuracy, clean up the automatic welding equipment around the oil impurities. Add a fence at the reachable welding range to prevent people from entering in the working process.
- Welding: Before entering mass production, the automatic welding equipment needs to be debugged. Operators according to the quality of the weld to adjust the welding parameters, so that after 2-3 times of fine-tuning, the welding quality of automatic welding equipment to meet the requirements, can be put into mass production. The human factor in the welding process may sometimes be misoperation, in the selection of welding parameters or the operation of the demonstration of the error. At the beginning of the operation of the selection of skilled operators, regular training for operators and technicians to improve the skills related to automatic welding.
Personnel before entering the work, wear a good protective gear, in the beginning of the work need to stand outside of the soldering range with a teaching device. Operation through the demonstrator, when the automatic welding equipment alarm signal, you need to press the emergency stop button to stop welding work, check and adjust the equipment.
Advantages of automatic soldering equipment:
- High efficiency: automatic welding equipment can continuously carry out welding operations, which greatly improves the welding efficiency and shortens the production cycle, thus reducing product costs. In the welding of manufacturing components, automatic welding equipment can greatly improve productivity and product quality.
- High quality: automatic welding equipment adopts advanced control system and mechanical structure, which can ensure the stability and consistency of welding quality. Applicable to shipbuilding, aerospace, automobile manufacturing and other industries.
- Easy to operate: automatic welding equipment usually adopts human-computer interface, easy and convenient operation, which can reduce manual operation errors.
- High reliability: automatic welding equipment adopts excellent materials and components, after strict testing and inspection, with high reliability and stability.
Automatic soldering technology with its high efficiency, high quality, easy to operate and high reliability and other significant advantages, in the manufacturing industry is playing an increasingly important role. However, when operating automatic welding equipment, we also need to pay attention to its working environment, debugging work and personnel safety to ensure that the welding process is carried out smoothly.