Definition of copper corrosion:
It is a phenomenon in which copper reacts with chemicals or gases in the surrounding environment under specific conditions, resulting in oxidation, corrosion or deterioration of the copper surface. This reaction may lead to a reduction in the surface quality of the copper material, a decrease in electrical conductivity, or even an impairment of the functional performance of the board.
Copper is considered a precious metal and is therefore resistant to oxygen attack. Due to a natural protective film, this metal is essentially immune to corrosion copper green is formed on the surface of the metal. If this protective film, usually made of reddish-brown cuprous oxide (Cu2o), is destroyed, the copper will eventually corrode.
Types of corroded copper:
Surface oxidation : The surface of copper reacts with oxygen to produce oxides, forming an oxide layer.This oxide layer may be black, green or brown in color. Common oxides are copper oxide (Cu2O) and copper oxide (CuO). Surface oxidation is usually one of the most common types of corroded copper.
Sulfidation: When copper comes into contact with sulfur-containing compounds, a sulfidation reaction may occur, producing copper sulfide (Cu2S) or other sulfides. Sulfidation usually occurs in environments that contain sulfides, such as groundwater where hydrogen sulfide gas (H2S) is present or during sulfidation processes in the chemical industry.
Oxidative corrosion: Prolonged exposure of copper to humid oxygen environments can lead to oxidative corrosion. This form of corrosion usually involves the formation of a uniform oxide layer on the surface of the copper, which changes its color to dark blue or black.
Dissolution corrosion: Copper undergoes dissolution corrosion in certain acidic or alkaline solutions, in which ions of copper dissolve into the solution and etching occurs on the copper surface. This type of corrosion is usually caused by strong acid or alkaline solutions.
Leaching corrosion: Copper may be subjected to localized leaching of the metal surface in a given environment, forming a localized corrosion phenomenon. This type of corrosion usually occurs in wet environments containing corrosive substances such as chloride ions, such as corroded copper in seawater.
Humidity and climatic conditions: high humidity environment, copper is susceptible to oxidation, accelerating the occurrence of corroded copper. The risk of corroded copper increases when climatic conditions are harsh or when the environment contains corrosive substances.
Chemical substances: Chemical substances present in the environment, such as oxygen, acids, salts, etc., may react with copper and cause corrosion phenomena.
Processing: Chemical treatments, solvents, or process conditions used during PCB manufacturing can cause corroded copper if improperly handled or left on the board surface.
Conditions that promote corroded copper:
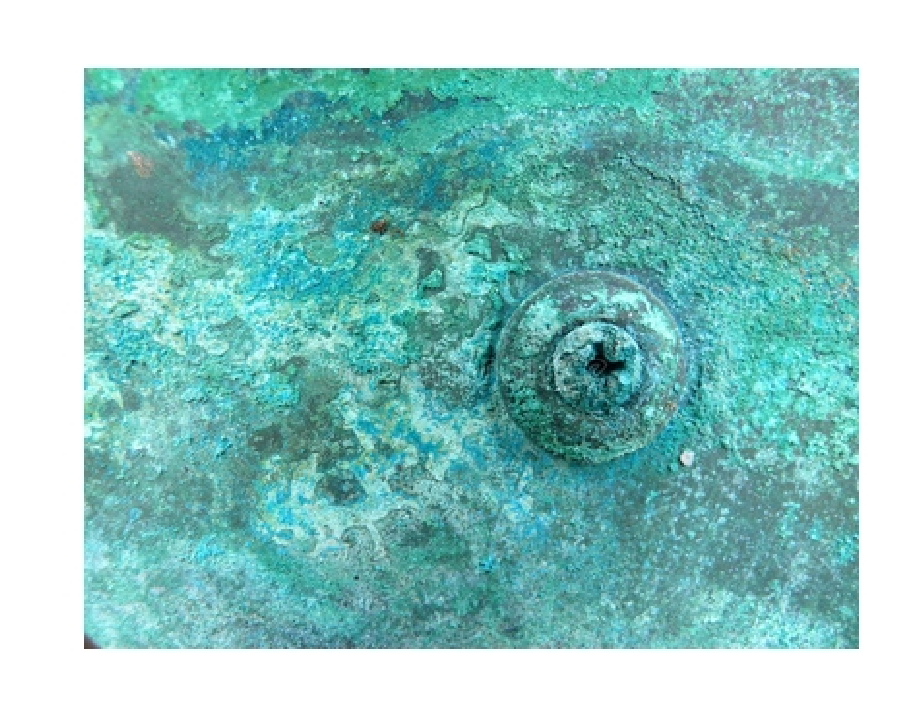
1) Common Conditions
Humidity: High humidity environments accelerate the onset of corroded copper because moisture makes it easier for oxygen and other chemicals to react with the copper surface.
Oxygen: copper and oxygen contact will be oxidized to form copper oxide, so the oxygen in the air is one of the main factors of corroded copper.
Acidic environment: Hydrogen ions (H+) in an acidic environment can accelerate the dissolution of copper and promote the occurrence of corroded copper. Strongly acidic solutions such as sulfuric acid and hydrochloric acid can especially exacerbate corrosion.
Alkaline environment: Hydroxide ions (OH-) in an alkaline environment can also accelerate the dissolution of copper and promote the occurrence of corroded copper.
Salts: Environments containing salts such as chloride ions can also accelerate corroded copper. Chlorides in seawater are one of the common causes of corroded copper.
Sulfides: Environments containing sulfides, such as hydrogen sulfide gas or water containing sulfur compounds, can cause copper to undergo a sulfidation reaction, accelerating the onset of corrosion.
Temperature: High temperature environments usually accelerate the rate of chemical reactions, so corroded copper may occur faster in high temperature environments.
In summary, factors such as humidity, oxygen, pH, salts and sulfides may all contribute to the occurrence of corroded copper. When designing and using PCBs, these factors need to be considered and measures taken to minimize the risk of corroded copper.
2) Other conditions, including:
- Unusually aggressive soils
- Localized and long-linear concentration cells produced by differences in soil composition
- Stray direct current (DC) flowing at ground level
- Poor design and workmanship
- Certain conditions of alternating current (AC) generation
- Thermoelectric effect
- Current action involved Different materials
Airborne contaminants (e.g., H.2 Altering the surface properties of copper can greatly reduce the adhesion produced by solder alloys or conductive resins and pastes. Such changes promote printed circuit board failures in microelectronic devices.
Copper coupled to aluminum or steel can lead to severe galvanic coupling corrosion. Cyanide is also highly corrosive to copper tubing.
The good resistance of seawater copper tube alloys to corrosion depends in part on the metal’s inherent cathodic nobility, but it also depends on copper’s ability to form protective passivation films. High velocity and turbulent flow conditions can remove these films and allow rapid localized corrosion.
Measures to prevent corrosion:
Control environmental conditions: Keep the production and storage environment dry and clean, avoid PCBs being exposed to high humidity or corrosive gases for a long time.
Selection of suitable materials: Select copper materials with good corrosion resistance in PCB design and manufacturing, such as surface-treated copper with better corrosion resistance.
Enhance cleaning and protection: After processing the PCB, clean and treat the PCB surface in time to prevent the residual chemical substances from triggering corrosion reactions. Protect PCBs with anti-corrosion coatings or encapsulation materials to extend their service life.
The above is my sharing on copper corrosion.