Circuit board aging refers to the natural phenomenon of gradual changes in the properties, structure and performance of circuit board materials after long-term use of electronic equipment.
The effects of circuit board aging:
- Lead to deformation of the circuit board
In the process of long-term use, the circuit board will be subject to external environmental factors and the influence of the working temperature of electronic components, and then deformation phenomenon. This deformation will lead to the installation of electronic components or sockets of the docking position of the slightest change, and ultimately lead to the failure of the circuit board. - Damage to the conductive properties of the circuit board
With the growth of the use of circuit board time, the conductive material on the board line will naturally age, making the circuit board conductive properties gradually reduced. When the conductive properties down to a certain extent, electronic equipment will not be able to operate normally, and may even suffer damage. - Induced line power failure or short-circuit failure
Circuit board aging will make the internal circuit line cracks or corrosion, which in turn triggered the line power failure or short-circuit phenomenon. Such failures usually appear in the circuit board on the location of the weld or component pins, these parts of the long-term exposure to electromagnetic waves, electric waves and other light, heat, oxidation and other factors under the interference. - Reduced signal transmission rate
The aging of the circuit board will lead to a slowdown in the transmission of small signals on it, which in turn adversely affects the data processing speed and stability of the equipment.
Preventive measures for circuit board aging
- Selection of high-quality materials and components
Selection of high-quality, highly heat-resistant, highly corrosion-resistant materials and components can effectively reduce the risk of circuit board aging. - Reasonable design and layout
Circuit board design and layout should be reasonable to avoid excessive concentration of circuit boards, thus reducing the risk of circuit board aging. - Regular inspection and maintenance
Regular inspection and maintenance of the circuit board, including cleaning, fastening and checking whether the electronic components are working properly, in order to guarantee the normal operation of the circuit board. - Control the use of the environment
Circuit boards should be used in a suitable environment to avoid high temperature, high humidity, strong electromagnetic interference and other unfavourable factors on the circuit board to extend the life of the circuit board. - Use of anti-aging technology
Anti-aging treatment of circuit boards, such as the use of high-quality protective patches or the use of special protective coatings, etc., can effectively extend the life of the circuit board.
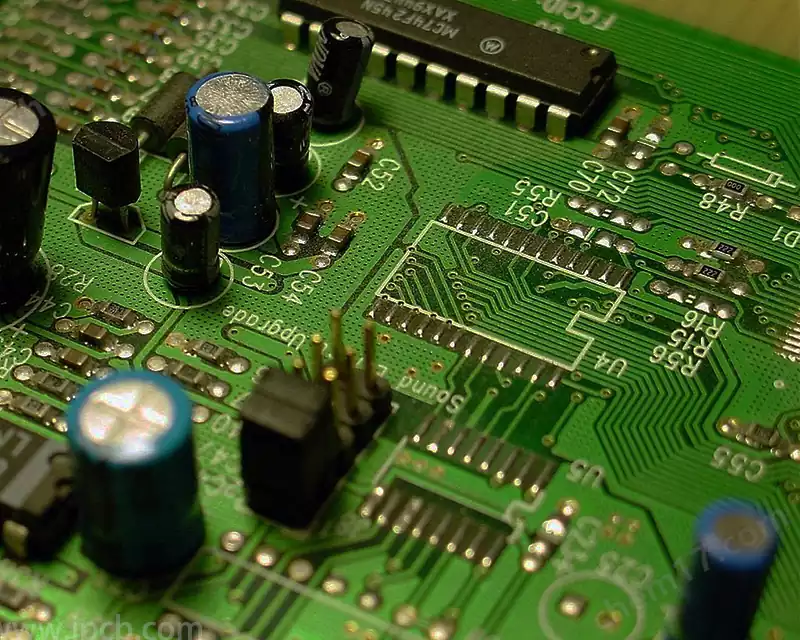
Circuit board aging workflow
Experiment preparation stage
Aging environment construction
Need to plan a dedicated aging test space (aging room), the requirements of stable and controllable environmental parameters, it is recommended that the temperature is set to 60 ℃ ± 2 ℃, the humidity is maintained at 70% ± 5% RH range, and is equipped with forced ventilation system to maintain air circulation.
Equipment selection and calibration
Select aging equipment (such as walk-in aging room or desktop constant temperature and humidity chamber) with PID precise temperature/humidity control function, and the temperature and humidity precision calibration (within ±1℃/±3%RH) should be completed through the third-party metrology institution.
Sample pre-treatment
Prepare a sufficient number of test samples according to the experimental scale, use laser engraving or coding technology to carry out unique identification, and carry out baseline testing of the samples (e.g., measurement of initial electrical performance parameters) to establish a control database.
Aging test execution process
Parameter Configuration and Verification
Set aging parameters according to test specifications (e.g. MIL-STD-883):
Base condition: 48h@60℃/70%RH
Accelerated conditions: 72h@85℃/85%RH (optional)
Use high-precision temperature and humidity recorder (accuracy ±0.3℃/±1.5%RH) to monitor the environment inside the aging chamber in real time, and record the data every 2 hours.
Sample loading and monitoring
Adopt modular tray to load samples, keep the spacing ≥5cm to ensure the uniformity of airflow, real-time monitoring of the sample status through the camera inside the box, triggering sound and light alarms when abnormal.
Process Data Acquisition
An IoT data acquisition system is set up to automatically record temperature and humidity profiles, sample temperature (via patch temperature sensors), equipment operating status and other parameters, generating traceable raw data packages.
Post-processing and Evaluation Stage
Failure mode analysis
Execute a three-level inspection process:
Appearance inspection: using AOI optical inspection system to identify defects such as cracks, corrosion, delamination, etc.
Electrical performance testing: Measure key parameters using an LCR tester (accuracy ±0.05%)
Functional verification: In-situ functional testing of complex circuit boards (e.g. signal integrity analysis)
Data Mining
Failure time analysis using Weibull distribution model, combined with SEM/EDS to analyse failure mechanism, and verification of key influencing factors through DOE experimental design.
Report Generation and Archiving
Generate ISO/IEC 17025 compliant test reports containing:
Summary of test conditions
Graphs of raw data (temperature and humidity curves, electrical performance comparison graphs)
Failure analysis conclusions (e.g. solder joint reliability assessment)
Recommendations for improvement (e.g. process parameter optimisation, material upgrade)
All data should be stored in a blockchain traceability system to ensure that the data cannot be tampered with.
Circuit board aging is inevitable, but through scientific control and technological innovation, we can turn the risk into a quantifiable quality improvement. In the future, with the popularity of data-driven predictive maintenance, aging management will move to a new dimension of greater intelligence and efficiency, ensuring the long-term stable operation of electronic equipment.