Aluminum substrate pcb is a kind of metal-based copper cladding board with good heat dissipation function. Generally, the single panel consists of three layers of structure, which are circuit layer (copper foil), insulation layer and metal base layer. For high-end use, there are also designed for double-sided boards, the structure of the circuit layer, insulation layer, aluminum base, insulation layer, circuit layer. Very few applications for multilayer boards, can be made of ordinary multilayer boards and insulation layer, aluminum base laminated into. LED aluminum substrate is PCB, also means printed circuit board, just the circuit board material is aluminum alloy, before our general circuit board material is fiberglass, but because of the LED heat is larger, so the LED lamps and lanterns with the circuit board is generally an aluminum substrate, able to conduct heat fast, other equipment or electrical appliances with the The circuit board is still glass fiber board!
Single-sided aluminum substrate: that is, there is only one layer of conductive graphics layer and insulating materials plus aluminum plate (substrate).
Double-sided line aluminum substrate: there are two layers of conductive graphics layer and insulating material plus aluminum plate (substrate) stacked together.
Multi-layer printed aluminum-based circuit board: by three or more layers of conductive graphics layer and insulating materials plus aluminum (substrate) alternately laminated and bonded together made of printed circuit boards.
Divided by surface treatment:
Immersion gold plate (chemical thin gold chemical thick gold selective immersion gold)
Electroplate (full-plate electroplate, gold finger, selective electroplate)
Sprayed tin boards, melted tin boards, immersion tin boards, immersion silver boards, electro-silver boards, immersion palladium boards.
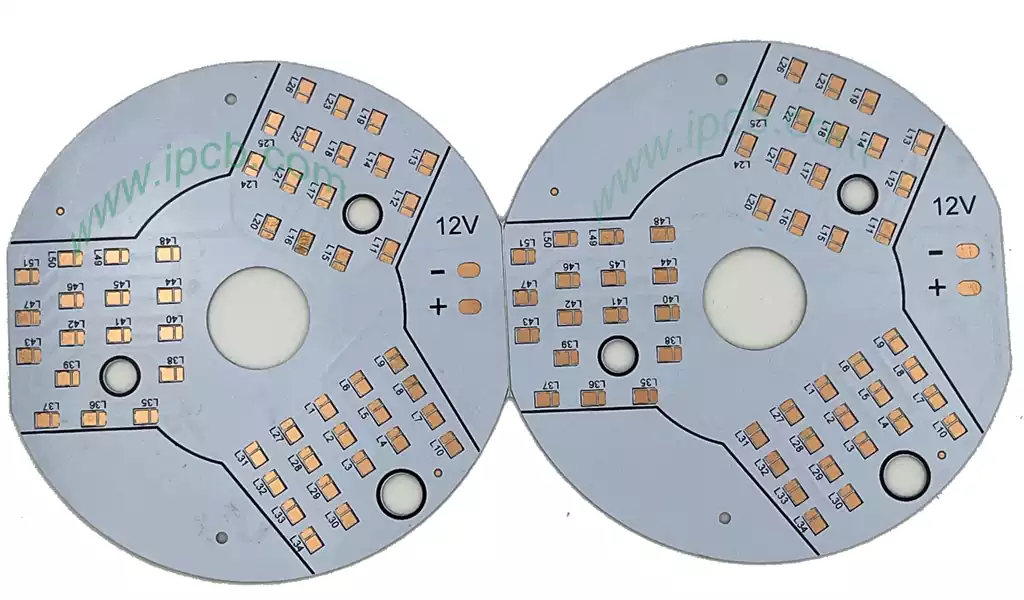
Working Principle
Power devices are surface mounted on the circuit layer. The heat generated during device operation is quickly conducted to the metal base layer through the insulating layer, and then the metal base layer transfers the heat out, thus realizing the heat dissipation of the device.
Compared with the traditional FR-4, aluminum substrate can minimize the thermal resistance, so that the aluminum substrate has excellent thermal conductivity; compared with thick film ceramic circuits, its mechanical properties are extremely good. In addition, aluminum substrates have the following unique advantages: RoHs compliant; more adaptable to the SMT process;
Extremely effective treatment of thermal diffusion in the circuit design scheme, thus reducing the module operating temperature, extending the service life, improving power density and reliability; reduce the assembly of heat sinks and other hardware (including thermal interface materials), reducing the size of the product, reducing the cost of hardware and assembly; the optimal combination of power circuits and control circuits; instead of fragile ceramic substrate, to obtain better mechanical durability.
Aluminum substrate pcb structure composition
- Line layer
The line layer (usually electrolytic copper foil) is etched to form printed circuits, which are used to realize the assembly and connection of devices. Compared with traditional FR-4, with the same thickness and the same line width, aluminum substrate can carry higher current. - Insulation Layer
Insulation layer is the core technology of aluminum substrate, mainly plays the function of bonding, insulation and thermal conductivity. Aluminum substrate insulation layer is the largest thermal barrier in the power module structure. The better the thermal conductivity of the insulating layer, the more conducive to the diffusion of heat generated by the device operation, but also the more conducive to lowering the operating temperature of the device, so as to achieve the purpose of improving the module’s power load, reduce the volume, extend the life of the module to improve the power output and so on. - Metal base
What kind of metal is used for the insulating metal substrate depends on the comprehensive consideration of the coefficient of thermal expansion of the metal substrate, thermal conductivity, strength, hardness, weight, surface condition and cost.
In general, from the cost and technical performance and other conditions to consider, aluminum is the ideal choice. The available aluminum sheets are 6061, 5052, 1060, etc.. If there are higher thermal conductivity, mechanical properties, electrical properties and other special performance requirements, copper, stainless steel, iron and silicon steel plate can also be used.
Points and considerations for design
Material Selection
Aluminum substrate is a kind of plate with high thermal conductivity, which is widely used in LED lighting, power electronics, automotive electronics and other fields. When choosing aluminum substrate materials, you need to consider its thermal conductivity, mechanical strength, corrosion resistance, solderability and other factors. Commonly used aluminum substrate materials include aluminum alloy, pure aluminum and copper substrate.
Selection of plate thickness
Aluminum substrate plate thickness is generally between 0.8mm-3.0mm, the specific selection needs to be determined according to the application scenario and the power of the circuit and other factors. Usually, the higher the power, you need to choose a thicker aluminum substrate to ensure the heat dissipation effect.
Copper laying method
In the design, the copper laying method is also very important, common single-sided copper, double-sided copper and multilayer boards. Single-sided copper is suitable for simple circuit design, double-sided copper is suitable for more complex circuit design, and multilayer board can be used for occasions that require higher line density and more complex circuit design.
Soldermask and Plating
Soldermasking and plating are two important steps in protecting a circuit board and adding aesthetic appeal. Soldermask protects the board from short-circuiting during the soldering process and increases the aesthetics of the board; spray plating increases the board’s corrosion resistance and improves conductivity.
Other considerations
In the aluminum substrate pcb design process, you also need to pay attention to the following points:
- Avoid the use of too many lines, try to use short connecting lines;
- take care to prevent over-concentration of pads, which may result in short circuits between pads;
- when using surface mount components, you need to consider its heat dissipation performance and surface flatness.
Aluminum substrate pcb is widely used in many fields due to their excellent heat dissipation performance and diverse design characteristics. With the continuous development of technology, aluminum substrate will show its unique value in more high-end applications.