What is copper clad laminate?Copper clad laminate board referred to as copper clad laminate, is a class of composite materials prepared by mixing reinforcing materials, resins and other auxiliary materials, and then laminated with copper cladding on one or both sides, and then finally made by hot pressing process.
There are three main types of copper-clad laminates: rigid copper-clad laminates, flexible copper-clad laminates and ceramic copper-clad laminates.
Rigid copper-clad laminate is a printed circuit substrate made of glued substrate and electrolytic copper foil (single-sided or double-sided) laminated and thermoformed. The glue used is phenolic and epoxy two kinds of epoxy copper-clad laminate has high electrical, mechanical and heat resistance. According to the processing performance and have a hot punch type and cold punch type two kinds of heat-resistant good self-extinguishing copper-clad laminate, widely used as electrical and electronic equipment, printed circuit boards.
Flexible copper-clad laminate (film-clad copper-clad laminate) is a flexible printed circuit substrate made of adhesive polyester film, polyimide film and electrolytic copper foil. This board is flexible, electrical, mechanical properties, polyimide film copper foil board heat resistance is high, can be immersed in high-temperature welding conditions.
Ceramic copper-clad laminate (DCB), copper and alumina between the oxide intermediate layer through the formation of chemical bonds to provide sufficient peel strength. The product is characterized by high thermal conductivity, good heat dissipation, operating temperature up to -55 ~ 850 ℃, the conductor cross-section under the same current load can be reduced by 88%; the coefficient of thermal expansion is close to that of silicon wafers, so the chip can be welded directly to the ceramic copper-coated foil laminate, greatly reducing the thermal resistance of the module; good electrical insulation properties. Can be used for various integration degree of the module, high-power modules, electronic circuits in the structure and connectivity materials, solid state relays, etc..
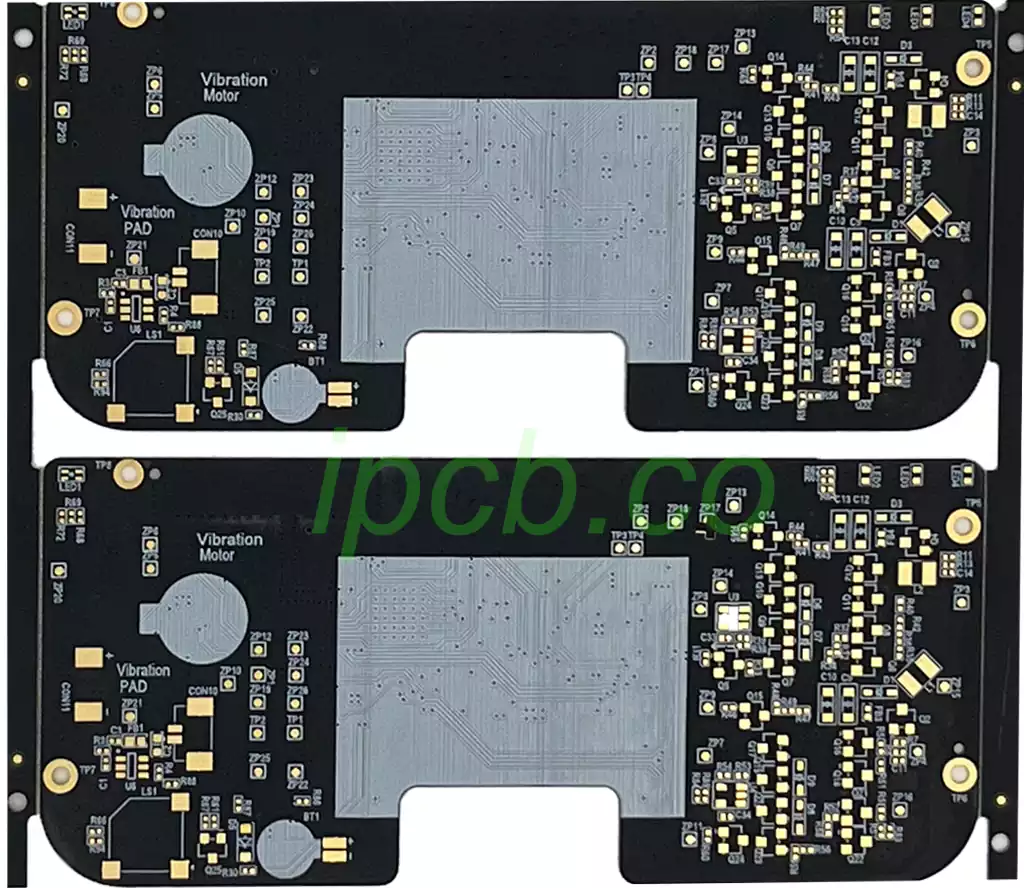
Copper-clad laminate manufacturing method
The main raw materials for manufacturing copper-clad laminates are resin, paper, glass cloth and copper foil.
The manufacturing of copper-clad laminates mainly involves three steps: resin solution preparation, reinforcing material impregnation and press molding.
(1) Resin
Copper-clad laminate resin with phenolic, epoxy, polyester, polyimide and so on. Among them, the largest amount of phenolic resin and epoxy resin.
Phenolic resins are phenols and aldehydes in acidic or alkaline medium condensed into a class of resins. Among them, phenol and formaldehyde polymerization in alkaline medium is the main raw material of paper-based foil board. In the manufacture of paper-based laminates, in order to obtain a variety of excellent performance of the sheet, often need to phenolic resin for a variety of modifications, and strict control of the resin’s free phenol and volatiles content, in order to ensure that the sheet does not delamination, no blistering under thermal shock.
Epoxy resin is the main raw material for glass cloth-based laminating foil sheet, which has excellent bonding properties and electrical and physical properties. The more commonly used ones are E-20, E-44, E-51 and self-extinguishing E-20 and E-25. In order to improve the transparency of the cladding board substrate, in order to check the graphic defects in the production of printed boards, the epoxy resin should have a lighter color.
(2) Impregnated paper
Commonly used impregnated paper are absorbent cotton paper, wood pulp paper and bleached wood pulp paper. Cotton velvet paper is made of cotton fibers with short fibers, which is characterized by better resin penetration, made of sheet punching and electrical properties are also better. Wood pulp paper is mainly made of wood fibers, generally less expensive than absorbent cotton paper, while the mechanical strength is higher, the use of bleached wood pulp paper can improve the appearance of the board.
In order to improve the performance of the sheet, the impregnated paper thickness deviation, standard weight, breaking strength and water absorption and other indicators need to be ensured.
(3) Alkali-free glass cloth
Alkali-free glass cloth is the reinforcing material for glass cloth-based laminated sheets, and for special high-frequency applications, quartz glass cloth can be used.
The alkali content of alkali-free glass cloth (expressed in Na20), IEC standards do not exceed 1%, JIS standard R3413-1978 provides no more than 0.8%, the former Soviet Union TOCT5937-68 standard provides no more than 0.5%, China’s Ministry of Construction and Industry standard JC-170-80 provides no more than 0.5%.
In order to adapt to the needs of general-purpose, thin and multi-layer printed boards, the glass cloth model for foreign foil boards has been serialized. Its thickness ranges from 0.025 to 0.234mm. glass cloth specifically needed and are post-treatment with coupling. In order to improve the mechanical properties of epoxy glass cloth-based cladding foil and reduce the cost of the plate, in recent years and the development of non-woven glass fiber (also known as glass felt).
(4) Copper foil
The foil material of the laminate can be copper, nickel, aluminum and other metal foils. But from the conductivity of the metal foil, weldability, elongation, adhesion to the substrate and price and other factors, in addition to special purposes, the most appropriate to copper foil.
Copper foil can be divided into calendered copper foil and electrolytic copper foil, calendered copper foil is mainly used in flexible printed circuits and some other special applications. Electrolytic copper foil is used in a large number of applications in the production of cladding boards. For the purity of copper, IEC-249-34 and our standards stipulate that it should not be less than 99.8%.
As an indispensable material in the modern electronics industry, copper clad laminates (CCLs) have unique properties and a wide range of applications that make them a key component in the manufacture of electronic substrates. With the continuous development of science and technology, CCL continues to innovate in material properties, manufacturing process and application areas, injecting new vitality into the development of the electronics industry and contributing to the scientific and technological progress of human society.