Copper plating with copper sulfate is an electrochemical process in which a copper sulfate solution is used as a plating bath to deposit a uniform copper layer on the conductive part of a circuit board by electrolysis. The process requires a stable current supply and suitable plating conditions to ensure the quality of the copper layer.
Advantages of copper sulfate plating
- Copper sulfate plating provides luster from high current density areas to constant current density flow areas.
- Copper sulfate plating has rich ductility and excellent leveling effect, and is widely used as a base for decorative plating.
- The current efficiency of copper sulfate plating is almost 100% and can be plated at high current density.
- Plating bath management and drainage treatment are easy.
- The internal stress of copper sulfate plating is small and the coating is soft.
- Excellent electrical conductivity of copper sulfate plating.
Disadvantages of copper sulfate plating
- Copper cyanide touch plating on the base is necessary because it can not be plated directly on the base metal base, such as iron and zinc punch mold.
- When iron is immersed in a copper sulfate plating bath, the following substitution reaction occurs and a copper substitution film with poor adhesion is deposited.
- Fe + Cu2 + → Fe2 + + Cu
Copper sulfate plating for printed circuit boards
- In through-hole plating of printed circuit boards, thick copper plating is required in the holes formed in the laminate.
- Compared with copper sulfate gloss bath, the ratio of sulfuric acid concentration to copper sulfate is increased to improve uniform electrode activity.
- Copper sulfate plating is widely used as through-hole plating for connecting the front and back of circuit boards. In addition, in the manufacture of multilayer wiring boards by the assembly method, the conductivity feature is utilized in the through-hole filling process used to connect the upper and lower layers.
- Copper sulfate plating is widely used in the electronics industry, and is also known as a high-polish copper sulfate bath.
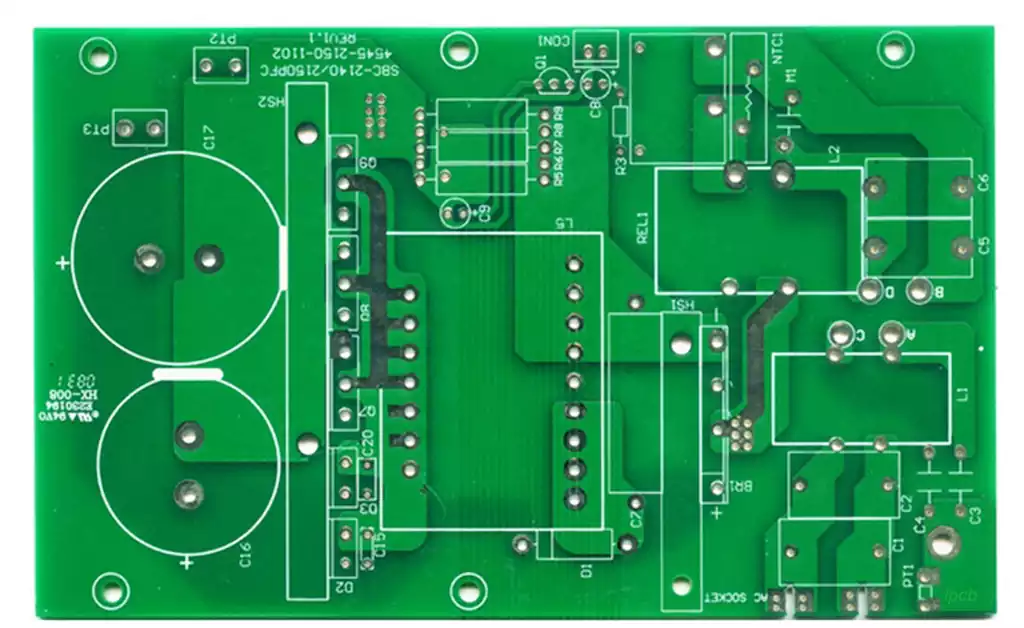
Copper plating process
Acid cleaning (5±1min) – Overflow rinse (90±30sec) – Overflow rinse (90±30sec) – Micro-etching (10±2sec) – Overflow rinse (90±30sec) – Overflow rinse (90±30sec) – Acid leaching (50±10sec) – Copper plating – Rinse (90±30sec) – Drying
Acid cleaning
① Purpose and function: to remove oxides on the line copper surface, ink residual film residue glue, to ensure that the primary copper and graphic plating of copper or nickel between the bonding force
② graphic ink is not alkali resistant, will damage the graphic line, so the graphic plating can only be used before the use of acid degreaser.
③ production only need to control the concentration of degreasing agent and time can be, degreasing agent concentration of about 7%, time to ensure that 5 minutes, a little longer will not have a negative impact; tank liquid replacement is also used in accordance with 15 square meters / liquid, supplemented by adding 100 square meters in accordance with 0.5-0.8L.
Micro-etching
① Purpose and function: clean and roughen the line copper surface, to ensure that the graphic plating of copper and copper between the bonding force
② micro-etching agent mostly sodium persulfate, roughening rate stability and uniformity, good washability, sodium persulfate concentration is generally controlled at 7.5 g / l or so, the time control in about 10 seconds, the drug added according to the 100 square meters 1-2 kg; copper content is controlled in the 20 g / l or less; other maintenance of the cylinder are the same as the sinking copper micro-etching.
Acid leaching
① role and purpose: to remove the plate surface oxides, activate the plate surface, the general concentration of 5%, some kept at 10% or so, mainly to prevent moisture brought in to cause the tank liquid sulfuric acid content is not stable;
② acid immersion time should not be too long to prevent the plate surface passivation; after a period of time, the acid appears turbid or copper content is too high should be replaced in a timely manner to prevent contamination of the plating copper cylinder and plate surface;
③ C.P grade sulfuric acid should be used here;
Copper plating with copper sulfate technology plays a vital role in the printed circuit board process. It not only ensures the conductivity of the board, but also provides a solid foundation for the quality and performance of the entire electronic product.