Copper sulfate electroplating in PCB plating occupies an extremely important position, acid copper plating good or bad directly affect the quality of copper plating layer and related mechanical properties, and the subsequent processing of a certain impact, so how to control the quality of copper sulfate electroplating is an important part of PCB plating.
The role of copper sulfate electroplating mainly includes the following points:
Supply copper ions in the plating solution. This is the most basic role of copper sulfate in electroplating, to ensure that the plating layer contains sufficient copper elements.
Prevent hydrolysis of copper salts. Copper sulfate can prevent the hydrolysis reaction of copper salt in the plating solution, thus maintaining the stability of the plating solution and the effective concentration of copper ions.
Improve the conductivity and cathodic polarization of the plating solution. Copper sulfate improves the electrical conductivity of the plating bath, which is essential to ensure high efficiency of the plating process and the quality of the plated layer.
Provides gloss and leveling effect. Copper sulfate plating is rich in ductility and leveling effects and is often used as a base for decorative plating.
Reduces solution resistance. This helps to reduce power consumption and improve plating efficiency.
Prevents rough or dendritic plating. At high current densities, copper sulfate prevents plating from producing rough or dendritic structures.
Process Flow:
Acid dipping → full-plate copper plating → graphic transfer → acid degreasing → secondary countercurrent rinsing → micro-etching → secondary → acid dipping → tin plating → secondary countercurrent rinsing → countercurrent rinsing → acid dipping → graphic copper plating → secondary countercurrent rinsing → nickel plating → secondary rinsing → citric acid dipping → gold plating → recycling → 2-3 levels of pure water rinsing → drying.
- Acid immersion
The purpose of acid immersion is to remove the plate surface oxides, activate the plate surface,the general concentration of %, some keep at 10% or so, mainly to prevent moisture brought in to cause the tank liquid sulfuric acid content is not stable.In the operation, we should pay attention to the control of acid immersion time, not too long, in order to prevent the board surface oxidation.For the acid, after a period of time, such as acid turbidity or copper content is too high should be replaced in a timely manner to prevent contamination of the plating copper cylinder and copy board board surface. The sulfuric acid used for dipping acid should be CP grade sulfuric acid. - Plating solution preparation
Acid copper sulfate plating solution has the advantages of good dispersing ability and deep plating ability, high current efficiency of board copying, low cost, etc., so that it is widely used in the production of printed circuit boards. Acid sulfate copper plating solution is generally composed of copper sulfate (CuSO ), sulfuric acid (H2SO ), hydrochloric acid (the main role of chloride ion Cl-) and organic additives. Copper sulfate is the main salt, is the main source of Cu2+ ions in the solution, the preparation should pay attention to control the concentration of copper sulfate.
Note
- Plating roughness
General plate corner roughness, most of the plating current bias caused by the current can be adjusted to lower the current and use the card meter to check the current display any abnormalities; full plate roughness, generally does not appear, this is mainly due to the low temperature in winter, the light agent content is insufficient; there are sometimes some rework fading plate plate surface treatment is not clean will also appear in a similar situation. - Electroplating plate copper particles
Caused by the plate surface copper particles produced by a number of factors, from the copper sinking, graphic transfer of the entire process, copper plating itself are possible. Copper particles caused by the copper plating process can be caused by any of the copper plating steps.
Alkaline degreasing in the water hardness is higher, more drilling dust (especially double-sided boards do not remove the slag) poor filtration, will not only cause the board surface roughness, but also cause roughness in the holes; but generally only cause roughness in the holes, the surface of the board can be removed from the minor pitting dirt micro-etching.
Micro-etching there are several situations: the micro-etching agent used in hydrogen peroxide or sulfuric acid quality is too poor or ammonium persulfate (sodium) containing impurities is too high, it is generally recommended that at least should be CP grade, industrial grade in addition to other quality failures; micro-etching tank copper content is too high or low temperatures resulting in the slow precipitation of copper sulfate crystals; tank liquid turbidity, pollution.
Most of the activation fluid is pollution or improper maintenance caused by, such as filter pump leakage, low specific gravity of the tank fluid, high copper content (activation cylinder used for too long, more than 3 years), so that it will produce granular suspensions or impurities colloidal within the tank fluid, adsorbed on the plate surface or the hole wall, which at this time will be accompanied by the generation of roughness in the hole.
Decolloid or accelerate: tank solution used for too long to appear turbid, because most of the decolloid solution is now formulated using fluoroboric acid, so it will attack the glass fibers in the FR-4, resulting in the tank solution of silicate, calcium salts in the elevated.
In addition, the copper content in the bath and the increase in the amount of dissolved tin liquid will cause the generation of copper particles on the surface of the board. Copper sink itself is mainly tank liquid activity is too strong, air mixing with dust, tank liquid in the solid suspended more small particles, etc., can be adjusted through the process parameters, increase or replace the air filter cartridge, the whole tank filtration, etc. to effectively solve.
After copper sinking, temporarily store the copper plate in the dilute acid tank, the tank liquid should be kept clean, and should be replaced in time when the tank liquid is turbid. Sinking copper plate storage time should not be too long, otherwise the plate surface is easy to oxidize, even in the acidic solution will be oxidized, and oxidation of the oxide film after oxidation is more difficult to deal with, so that the plate surface will also produce copper particles.
The above mentioned copper sinking process to create a sunken plate copper particles, in addition to the plate surface caused by oxidation, generally more uniform distribution on the plate surface, the regularity is stronger, and the pollution generated here regardless of whether the conductive or not, will result in the generation of copper plating copper particles on the surface of the plate, the treatment of a number of small test panels can be used step by step to deal with the control judgement, for the failure of the board on the scene can be resolved with a soft brush brush can be resolved;; and the development of a graphic transfer process: the development of the plate has a copper grain.
Graphics transfer process: developing residual glue (very thin residual film plating can also be plated and covered), or after the development of cleaning is not clean, or the board in the graphics transfer after placing the time is too long, resulting in varying degrees of oxidation of the board surface, especially when the board surface is poorly cleaned or stored in the workshop when the air pollution is heavier.
The solution is also to strengthen the water washing, strengthen the plan to arrange a good schedule, strengthen the strength of acid degreasing.
Copper cylinder caused by copper particles on the surface of the reasons are probably summarized in several aspects: tank liquid parameters maintenance, production operations, materials and process maintenance.
Tank liquid parameter maintenance, including sulfuric acid content is too high, the copper content is too low, the tank liquid temperature is low or too high, especially no temperature control cooling system of the plant, this will cause the tank liquid current density range down, according to the normal operation of the production process, may produce copper powder in the tank liquid, mixed into the tank liquid.
Production operations mainly when playing too much current, clamping bad, empty clamping point, the slot drop plate dissolved against the anode, etc. will also cause part of the plate current is too large, resulting in copper powder, fall into the tank liquid, gradually produce copper particles failure;
Material is mainly phosphorus copper angle phosphorus content and phosphorus distribution uniformity of the problem; production and maintenance is mainly large processing, copper angle added when dropped into the tank, mainly large processing, anode cleaning and anode bag cleaning, many factories are not well dealt with, there are a number of hidden dangers.
Copper ball big processing is should be cleaned the surface, and with hydrogen peroxide micro-etching out of the fresh copper surface, anode bag should be successively soaked with sulfuric acid hydrogen peroxide and lye, clean, especially the anode bag should be used 5μm ~ 10μm gap semi-cured sheet filter bag. As for the copper sulfate plating tank itself, its pretreatment generally does not cause copper particles on the board, because non-conductive particles at most cause the board leakage plating or pits.
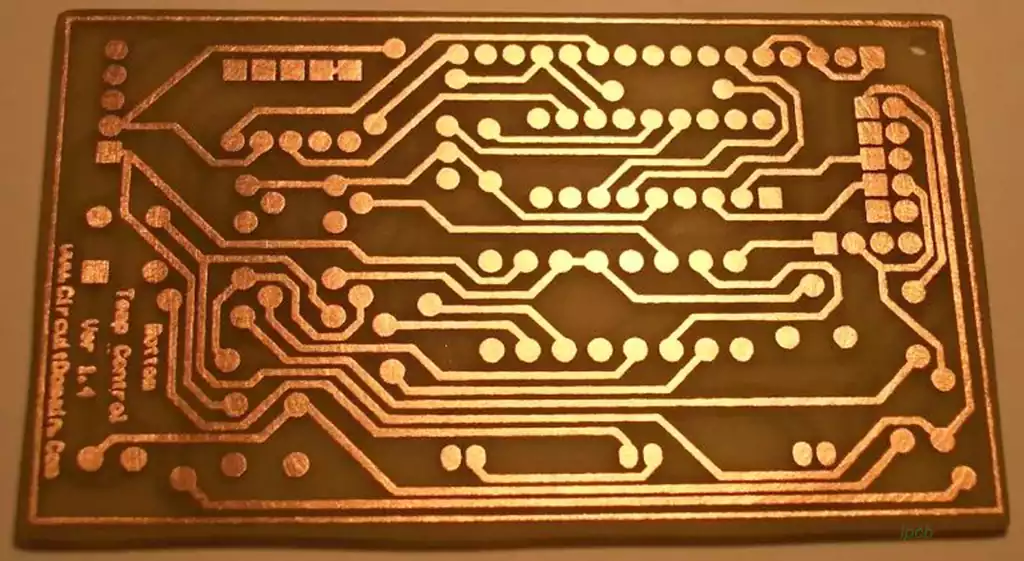
- Plating Crater
This defect is caused by more processes, from copper sinking, graphic transfer, to electroplating pre-treatment, copper plating and tin plating.
Copper caused by the main copper baskets for a long time poor cleaning, in the micro-etching containing palladium and copper pollution solution will drip from the basket on the board, the formation of pollution in the immersion of copper plate after the electrode caused by the leakage of the plating of the point that is, the crater.
Graphics transfer process is mainly caused by poor equipment maintenance and development and cleaning, due to a number of reasons: brush the board machine brush roll suction stick contamination glue stains, blow-drying drying section of the wind knife fan dirty, oil dust, etc., the board surface of the film or printing before the dust removal is not appropriate, the developer developer is not clean, poor washing after development, silicone-containing defoamer contamination of the board surface, and so on.
Plating pretreatment, because both acidic degreaser, micro-etching, pre-impregnation, the main component of the tank solution have sulfuric acid, so the water hardness is high, there will be turbidity, contamination of the board surface; in addition, some companies hanging tools poor adhesive coating, a long time will be found to wrap the adhesive coating in the tank night in the dissolution of the diffusion of contamination of the tank solution; these non-conductive particles adsorbed in the surface of the plate, the subsequent plating may cause varying degrees of plating pits.
Copper sulfate plating tank itself may be the following aspects:
(1) The air blower tube is deviated from its original position and the air is not stirred evenly;.
(2) Filter pump leakage or liquid inlet near the blower tube to inhale air, resulting in fine air bubbles, adsorbed on the plate surface or line edge, especially lateral line edges, line corners;;.
(3) There may be another point is the use of low-quality cotton core, processing is not complete, cotton core manufacturing process used in the anti-static treatment agent contamination of the tank liquid, resulting in leakage plating, this case can increase the drum, the liquid surface foam cleaned up in a timely manner, the cotton core with acid and alkali soaking and other processing.
- Board color white or uneven color
This is mainly a light agent or maintenance issues, and sometimes may also be acidic degreasing after cleaning and micro-etching problems.
Copper polish disorder, serious organic pollution, tank liquid temperature is too high can be caused.
Acid degreasing generally do not have cleaning problems, but if the water pH value is acidic and more organic matter, especially recycled recycled water washing, it may cause poor cleaning, micro-etching uneven phenomenon; micro-etching is mainly considered micro-etching agent content is too low, micro-etching liquid copper content is high, the trough liquid temperature is low, etc., will also cause uneven micro-etching of the plate surface;
In addition, the poor quality of cleaning water, washing time is a little long or pre-impregnated with acid pollution, the surface of the plate may be slightly oxidized after treatment, in the copper tank plating, due to acidic oxidation and the plate is charged into the tank, the oxides are difficult to remove, but also cause the plate surface color is not uniform; in addition to the plate surface in contact with the anode bag, anode conductivity is not uniform, the anode passivation and so on will also cause such defects.