Adhesives play a critical role in the manufacturing and assembly of printed circuit boards (PCBs). Their primary functions include bonding components to the board, providing electrical insulation, and ensuring mechanical stability. With the ongoing miniaturization and complexity of electronic devices, the demand for high-performance adhesives has significantly increased. This article explores various types of adhesives used in PCB manufacturing, their applications, benefits, and the key considerations for selecting the right adhesive.
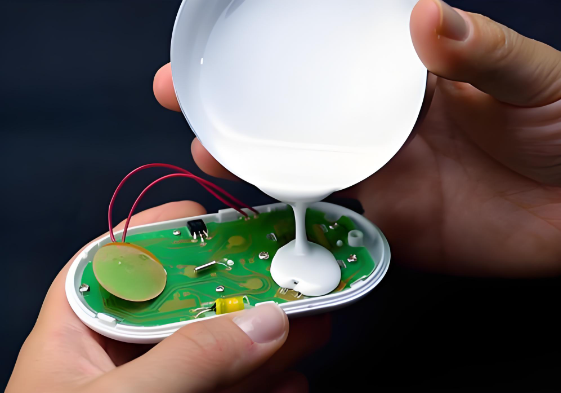
Types of Adhesives for PCB
Epoxy Adhesives
Epoxy adhesives are among the most commonly used adhesives in PCB manufacturing. They offer excellent mechanical strength, electrical insulation, and thermal resistance. Epoxies can be either one-part or two-part systems. One-part epoxies are pre-mixed and cure at elevated temperatures, while two-part epoxies require mixing before application and can cure at room temperature or with heat. Their versatility makes them suitable for a wide range of applications, from bonding components to encapsulating entire assemblies.
Acrylic Adhesives
Acrylic adhesives are known for their fast curing times and strong bond strength. They are particularly useful in applications where rapid assembly is required. Acrylics provide good adhesion to various substrates, including metals, plastics, and ceramics. They also offer excellent resistance to environmental factors such as moisture, chemicals, and UV light. These properties make them ideal for use in harsh operating conditions and for outdoor electronic applications.
Silicone Adhesives
Silicone adhesives are valued for their flexibility, thermal stability, and resistance to extreme temperatures. They are often used in applications where thermal cycling and mechanical stress are concerns. Silicones provide excellent adhesion to a variety of substrates and maintain their properties over a wide temperature range. They are commonly used for potting and encapsulating components, providing protection against moisture, dust, and vibration.
Polyurethane Adhesives
Polyurethane adhesives offer a good balance of flexibility and strength. They are suitable for applications that require a durable bond with some degree of flexibility to accommodate thermal expansion and contraction. Polyurethanes provide excellent resistance to impact, abrasion, and chemicals. They are often used in automotive and industrial electronics where components are exposed to harsh conditions and mechanical stress.
Cyanoacrylate Adhesives
Cyanoacrylate adhesives, also known as superglues, are known for their rapid curing and strong bond strength. They are ideal for quick fixes and small-scale bonding applications. Cyanoacrylates bond well to a variety of substrates, including metals, plastics, and ceramics. However, they may not be suitable for applications requiring high thermal or chemical resistance, as their performance can degrade under such conditions.
Applications of Adhesives in PCB Manufacturing
Component Bonding
One of the primary applications of adhesives in PCB manufacturing is bonding components to the board. Adhesives provide mechanical stability and ensure that components remain securely attached during operation. This is especially important for surface-mount technology (SMT) components, which are smaller and more delicate than through-hole components. Adhesives used for component bonding must offer high bond strength, good thermal stability, and compatibility with soldering processes.
Wire Tacking
Adhesives are used to secure wires and cables to the PCB, preventing movement and reducing the risk of mechanical damage or electrical shorts. Wire tacking adhesives need to be flexible enough to accommodate thermal expansion and contraction while providing a strong bond. They should also offer good resistance to environmental factors such as moisture and chemicals.
Encapsulation and Potting
Encapsulation and potting involve covering components or entire assemblies with a protective layer of adhesive material. This provides protection against moisture, dust, vibration, and mechanical shock. Encapsulation and potting adhesives must offer excellent electrical insulation, thermal stability, and resistance to environmental factors. Epoxy and silicone adhesives are commonly used for these applications due to their excellent properties.
Conformal Coating
Conformal coatings are thin layers of adhesive material applied to the surface of the PCB to protect against moisture, dust, and chemicals. These coatings provide electrical insulation and enhance the reliability and lifespan of the board. Common materials used for conformal coatings include acrylics, silicones, and polyurethanes. The choice of material depends on the specific environmental conditions and performance requirements of the application.
Die Attach Adhesives
In semiconductor packaging, die attach adhesives are used to bond the silicon die to the substrate or package. These adhesives need to provide excellent thermal conductivity to dissipate heat generated by the die and maintain mechanical stability. Epoxy and silver-filled adhesives are commonly used for die attach applications due to their high thermal and electrical conductivity.
Thermal Interface Materials
Thermal interface materials (TIMs) are used to enhance heat transfer between components and heat sinks or other cooling devices. TIMs can be in the form of adhesive tapes, gels, or pads, and they help to minimize thermal resistance at the interface. These materials are critical in high-power electronic applications where efficient thermal management is essential to maintain performance and reliability.
Benefits of Using Adhesives in PCB Manufacturing
Enhanced Mechanical Stability
Adhesives provide additional mechanical support to components, reducing the risk of damage due to vibration, shock, or mechanical stress. This is particularly important in applications where the PCB is subject to harsh conditions, such as automotive or industrial electronics. By securing components firmly in place, adhesives help to ensure the long-term reliability and performance of the board.
Improved Electrical Insulation
Many adhesives used in PCB manufacturing offer excellent electrical insulation properties. This helps to prevent short circuits and electrical interference between components. By providing a barrier between conductive elements, adhesives enhance the overall electrical performance of the board. This is especially important in high-frequency and high-voltage applications where electrical isolation is critical.
Enhanced Thermal Management
Adhesives with good thermal conductivity can help to dissipate heat generated by components, improving the thermal management of the PCB. This is essential for maintaining the performance and reliability of electronic devices, especially those with high power densities. Thermal adhesives are often used in applications where effective heat dissipation is required, such as in power electronics and LED assemblies.
Environmental Protection
Adhesives provide a protective barrier against environmental factors such as moisture, dust, chemicals, and UV light. This helps to enhance the durability and lifespan of the PCB, especially in harsh operating conditions. By protecting components and connections from corrosion and degradation, adhesives contribute to the long-term reliability of the board.
Versatility and Ease of Application
Adhesives are available in various forms, including liquids, pastes, films, and tapes, offering flexibility in application methods. They can be applied using automated dispensing systems, screen printing, or manual techniques, depending on the specific requirements of the manufacturing process. This versatility makes adhesives suitable for a wide range of PCB applications, from small-scale prototyping to large-scale production.
Cost-Effectiveness
Using adhesives can be a cost-effective solution for PCB assembly and manufacturing. They can reduce the need for mechanical fasteners, which can add weight and complexity to the assembly. Additionally, adhesives can simplify the manufacturing process and reduce labor costs by enabling automated application methods. This can result in significant cost savings, especially in high-volume production environments.
Weight Reduction
Adhesives can contribute to weight reduction in electronic assemblies by eliminating the need for mechanical fasteners and connectors. This is particularly important in applications where weight is a critical factor, such as in aerospace, automotive, and portable electronics. By reducing the weight of the assembly, adhesives can help to improve performance, fuel efficiency, and portability.
Key Considerations for Selecting PCB Adhesives
Compatibility with Substrates
The adhesive must be compatible with the materials used in the PCB and its components. This ensures a strong bond and prevents issues such as delamination or corrosion. Manufacturers should consider the chemical properties of both the adhesive and the substrates to ensure compatibility. Testing and validation are often required to confirm that the adhesive will perform as expected under the specific conditions of the application.
Thermal and Mechanical Properties
The adhesive should have the necessary thermal and mechanical properties to withstand the operating conditions of the PCB. This includes factors such as temperature resistance, thermal conductivity, flexibility, and mechanical strength. The choice of adhesive should be based on the specific requirements of the application and the expected operating environment. For example, high-temperature applications may require adhesives with excellent thermal stability, while applications subject to mechanical stress may require adhesives with high flexibility and impact resistance.
Cure Time and Process
The curing process and time required for the adhesive to reach its full strength are important considerations. Fast-curing adhesives can increase production efficiency, but they may require specific curing conditions such as elevated temperatures or UV light. Manufacturers should evaluate the curing requirements of the adhesive and ensure that they are compatible with the overall manufacturing process. Additionally, the adhesive’s pot life, or the time it remains workable after mixing, should be considered for two-part systems.
Electrical Properties
The adhesive must provide the necessary electrical insulation and conductivity properties for the specific application. This includes factors such as dielectric strength, volume resistivity, and surface resistivity. The choice of adhesive should be based on the electrical performance requirements of the PCB and its components. For high-frequency applications, low dielectric constant and low dissipation factor may be important considerations.
Environmental Resistance
The adhesive should offer resistance to environmental factors such as moisture, chemicals, UV light, and temperature variations. This ensures the long-term reliability and performance of the PCB, especially in harsh operating conditions. Manufacturers should consider the specific environmental conditions in which the PCB will operate and select an adhesive that meets these requirements. Accelerated aging tests and environmental simulations can help to evaluate the adhesive’s performance under various conditions.
Application Method
The method of application is an important consideration when selecting an adhesive. Automated dispensing systems can increase production efficiency and ensure consistent application, but they may require specific adhesive properties such as viscosity and thixotropy. Manufacturers should evaluate the application method and select an adhesive that is compatible with their manufacturing process. Additionally, the adhesive’s open time, or the time it remains tacky and bondable after application, should be considered for manual assembly processes.
Health and Safety
The health and safety of workers handling the adhesives should be considered. Some pcb adhesives may contain volatile organic compounds (VOCs) or other hazardous chemicals that require proper ventilation and protective equipment. Manufacturers should review the safety data sheets (SDS) for each adhesive and ensure that appropriate safety measures are in place to protect workers during handling and application. Additionally, low-VOC and environmentally friendly adhesives are available for applications where health and safety are a primary concern.
Conclusion
Adhesives are essential components in the manufacturing and assembly of printed circuit boards, providing mechanical stability, electrical insulation, thermal management, and environmental protection. The selection of the right adhesive is critical to ensuring the reliability and performance of the PCB. By understanding the different types of adhesives, their applications, benefits, and key considerations, manufacturers can make informed decisions and optimize their PCB manufacturing processes.
In the evolving landscape of electronics, the importance of adhesives will continue to grow, driven by the demands for miniaturization, higher performance, and reliability. As new adhesive technologies emerge, staying informed about the latest developments and trends will be crucial for manufacturers to maintain a competitive edge.