In the manufacturing process of electronic products, flux, as an important soldering auxiliary material, plays a key role in connecting electronic components with circuit boards. However, while flux brings convenience, its residue problem has also become a challenge that cannot be ignored. Excessive flux residue not only affects the appearance and quality of the product, but can also lead to a series of potential performance and safety risks.
Excessive flux residue can cause a variety of adverse effects,mainly including:
Affecting solder joint appearance and product quality.Residual flux will lead to the appearance of the solder joint is not beautiful, the surface of the useless residue, and may even form a solidified residue around the solder joint,which not only affects the product aesthetics,but also may have an adverse effect on the impedance value of the product and conduction performance.
Leads to short circuits and circuit board corrosion.Excessive flux may make the parts around the solder joints unclean,leading to short circuits, or cause corrosion of the circuit board surface,impairing the reliability of the circuit.
Affects soldering speed and component reliability.Flux residue reduces soldering speed, increases cleaning costs,and may damage SMD components,leading to component failure.
Affect the stability and reliability of electronic products.Flux residue may penetrate into the soldered interface of electronic components,resulting in short circuits or poor electrical connections.
May cause fire. Flux residues may generate heat or cause explosions in high temperature environments.
Harmful to the environment and human health. The chemical components in the flux may pollute the environment,and the smoke and harmful gases generated during the soldering process may also be hazardous to human health.
Impact on signal transmission.In communication systems,flux residue may affect the absorption and transmission of signals,cause signal alteration and termination, and may even affect other electrical appliances in the vicinity.
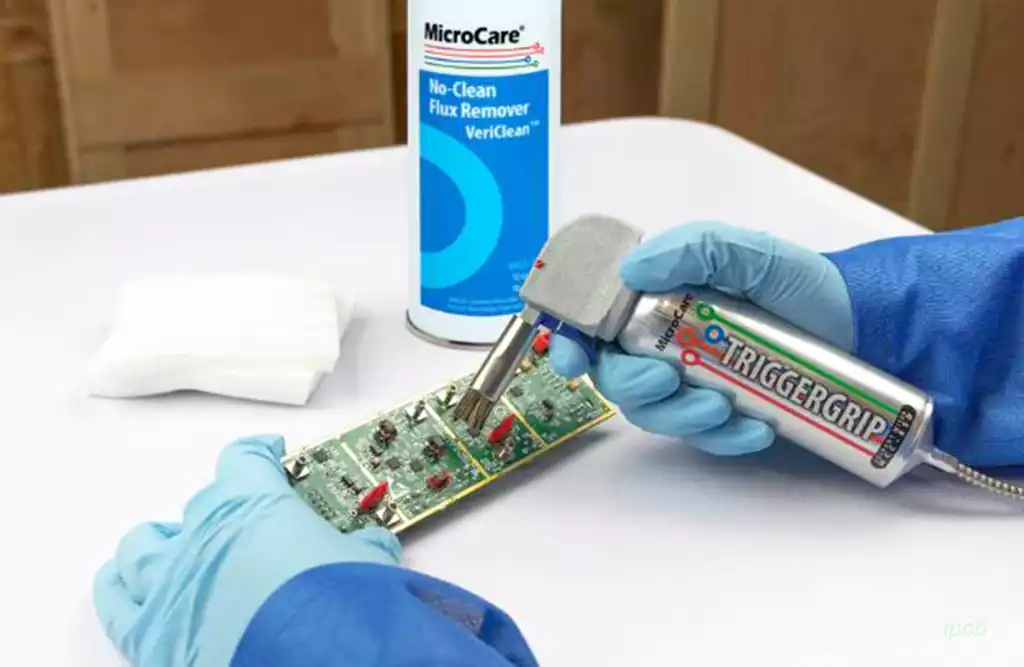
How to clean flux residue(clean flux off circuit board)
- Water washing method
Water washing is the most common cleaning method. It uses pure water or deionized water to clean off the flux. This method is simple, easy to implement, and relatively low cost.However,water washing may cause damage to some PCBs and components, such as moisture can accumulate on the pads and pins of components,resulting in short circuits or corrosion. - Solvent cleaning
Solvent cleaning is a highly efficient cleaning method.It uses a chemical solvent to dissolve the flux, and then washed off by rinsing or spraying. This way can quickly and effectively clean flux,but the cost of solvents is high,and the use of special attention to safety. - Ion cleaning
Ion cleaning is a high-tech cleaning methods, it uses ion beam cleaning PCB surface.Ion beam has high energy and high speed, can remove the PCB surface dirt and flux. This method has excellent cleaning results and does not cause damage to the PCB or components.However,ion cleaning equipment is expensive and requires specialized equipment and technical support. - Oxidation cleaning
Oxidation cleaning is a physical cleaning method. It uses an oxidizing agent to oxidize the flux into a substance that is easy to clean,and then remove it by rinsing. This method is suitable for some PCB board and components that are not suitable for water or solvent cleaning.However, the cost of the oxidizer is high and requires special attention to safety. - Semi-aqueous cleaning
Semi-aqueous cleaning is a combination of aqueous cleaning and solvent cleaning cleaning method. In semi-aqueous cleaning, the use of water and appropriate cleaning agents to clean the circuit board, and then use organic solvents to clean the residue. Semi-Aqueous Cleaning cleans oil and residues from circuit boards and electronic components and is more environmentally friendly and safer than aqueous and solvent cleaning. For more stubborn residues can be cleaned with dry ice selective removal. - Ultrasonic cleaning
The use of ultrasound in the cleaning solution to produce tiny bubbles in the cleaning method. These bubbles can penetrate the small space between the electronic components and circuit boards, thus cleaning. Ultrasonic cleaning for cleaning small electronic components and circuit boards are very effective. The disadvantage is that the investment is large, more processes, the burden on small and medium-sized PCBA circuit board manufacturing enterprises is not small.
The solution to the flux residue problem is an important part of the electronic manufacturing process. By choosing the appropriate cleaning method, companies can ensure the stability and enhancement of product quality, while reducing production costs and improving production efficiency. With the continuous progress of technology, more efficient and environmentally friendly cleaning technology will emerge in the future, injecting new momentum into the development of the electronics manufacturing industry.