FR4 is a commonly used PCB substrate materials, it is “flame retardant” (Flame Retardant) level 4 of the glass fiber reinforced epoxy resin material abbreviation.
Flame Retardant (Flame Retardant): Flame Retardant refers to the ability of a material to slow down the propagation of flame or self-extinguish when subjected to flame, thus reducing the risk of fire. Materials used in electronic equipment, especially PCB substrates, need to have good flame retardant properties to ensure that the equipment will not cause more serious problems due to fire under abnormal conditions.
FR-4 Grade 4: FR-4 is categorized into different grades, with Grade 4 representing a material with high flame retardancy. According to the International Electrotechnical Commission (IEC) standard, FR-4 grade 4 means that the vertical burning rate of the material is less than or equal to 30 mm/min. FR-4 grade 4 materials are more reliable in terms of flame retardancy and are widely used in the manufacture of electronic equipment.
Therefore, the term FR4 is an abbreviation for a class of glass fiber reinforced epoxy resin materials, which is a common, reliable, good flame retardant PCB substrate materials. Due to its stable performance and relatively low production costs, FR-4 materials are widely used in the manufacture of most general-purpose electronic equipment.
FR4 plate is a glass fiber reinforced epoxy resin that is widely used in the manufacture of printed circuit boards. The following are the reasons why FR4 has become the mainstream material for PCB board.
- Good electrical properties: FR4 has good dielectric properties and insulating properties, can effectively isolate different electrical signals on the circuit board to prevent signal interference and crosstalk.
- High strength and rigidity: FR4 material has high strength and rigidity, can withstand high pressure, high temperature and mechanical stress and other requirements for use in different environments.
- Ease of processing: FR4 material is easy to process, can be drilled, etched, paste glue and other processing, to meet different PCB design requirements.
- Low cost: relative to other materials, FR4 material cost is low, to meet the needs of large-scale PCB production.
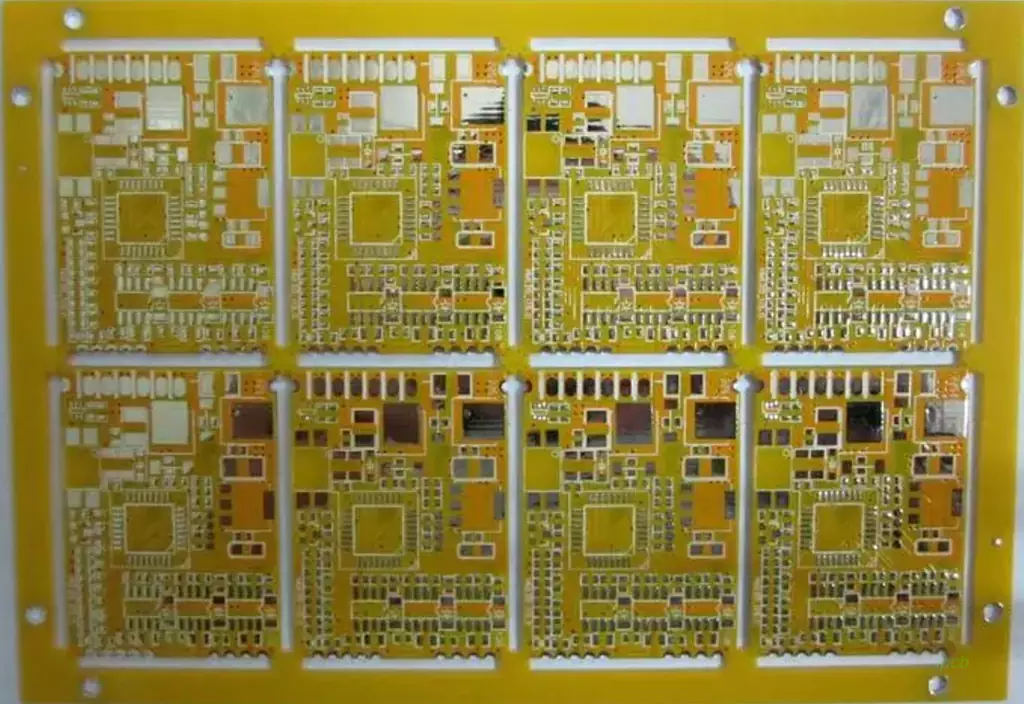
FR4 production process generally includes the following steps.
- Glass fiber preparation: glass fiber mixed with some chemicals, made of a certain length and diameter of the fiber.
- Resin preparation: epoxy resin mixed with some additives, modulation into a certain proportion of resin.
- Glass fiber and resin mixing: the prepared glass fiber and resin mixing, the formation of FR4 sheet substrate.
- Pressing: The mixed FR4 substrate is put into the pressing machine and pressed under high pressure and high temperature, so that the FR4 sheet forms a fixed shape and thickness.
- Cutting: The pressed FR4 sheet is cut into the required size and shape.
- Surface treatment: The surface treatment of FR4 sheet, including copper plating, tin plating, etching, etc., to form a PCB board.
After the above steps, FR4 material can become the main material of the PCB board, used in a variety of electronic products.
FR4 plate epoxy board storage 4 major points
FR4 insulation board should not be placed in direct sunlight. Some friends because of long-term storage in one place, so want to take out the sun, so may be placed in direct sunlight, the performance characteristics of the epoxy board is harmful, should be in the shade to dry.
Pay attention to the storage environment of fr4 epoxy board. Many friends put the insulating board in the warehouse for a long time without paying attention to the air dryness and environmental humidity. Generally, the suitable environmental conditions are air humidity not more than 70%, the temperature is about 25℃.
Pay attention to the use limit of fr4 epoxy board. Generally the temperature exceeds 160 degrees may be deformed, use must pay attention to the temperature.
Pay attention to the maintenance. Maintenance, literally means protection and maintenance, so maintenance is also very important.
FR4,as a cornerstone material in the electronics field,occupies a pivotal position in PCB manufacturing due to its excellent electrical properties,high strength and rigidity,ease of processing and relatively low cost.Its production process is rigorous and delicate,ensuring that each board meets strict quality standards.With the continuous development of electronic technology,this material will continue to play its important role in the field of electronics,for the stability and reliability of electronic equipment to provide a solid guarantee.