Furnace control board, also called furnace PCB board, is an important components used in a variety of heating appliances and are responsible for controlling the furnace’s operating status, temperature regulation and safety monitoring functions. These control boards usually integrate microprocessors, sensors and power controllers to accurately regulate the heating process by receiving commands from the user inputs to ensure the stability and safety of the heating effect.
When designing a furnace control board, it is critical to select the right material to ensure that the board will function properly and remain stable in high temperature environments. Different PCB materials have different temperature resistance levels for different application requirements.
FR-4 is a commonly used material for printed circuit boards, and its temperature resistance usually ranges from 130°C to 180°C. In cases where high temperature resistance is required for applications, a high TG (glass transition temperature) version of FR-4 material can be selected, which is suitable for long periods of time in high-temperature environments, as it can withstand temperatures from 170°C to 180°C.
High-temperature FR-4 materials have a high Tg value and are capable of operating at temperatures up to 260°C for short periods of time. Typically used in high-end electronic devices, this material provides better mechanical strength and heat resistance, making it adaptable to high-temperature applications.
For higher operating temperatures, polyimide materials are an excellent choice, with temperature resistance typically exceeding 200°C and even reaching 500°C in some cases. The advantage of polyimide materials is that they have excellent thermal stability and insulating properties, making them suitable for high-temperature and high-reliability applications.
In addition to the above materials, there are also PCB materials specifically designed for extreme high temperature environments, such as certain models of ceramic substrates and metal-based materials. These materials are typically used in specialized applications that can withstand higher temperatures and provide excellent thermal conductivity.
Furnace circuit boards contain several core components such as pads, vias, wires, components, connectors, etc. Together, these components form the complete electrical connection and support structure of the circuit board.
- Power Module
The power supply module is one of the key components of the furnace control board, responsible for converting alternating current into stable direct current to provide the required power supply for the circuit. The main components of this module include rectifiers, filters and voltage regulators to ensure the stability and reliability of the power supply. - Control unit
The control unit can be regarded as the “brain” of the furnace pcb board, responsible for processing user input and monitoring the heating process. It usually consists of a microprocessor and some peripheral circuits, which can generate control signals and regulate the power output according to the conditions of temperature and time set by the user. - Induction Coil
The induction coil is the key component in generating the electromagnetic field, which is installed under the surface of the stove. When an electric current passes through the induction coil, it creates an alternating magnetic field on the surface of the stove, which heats up the pots and pans. The design and layout of this part directly affects the heating efficiency and uniformity. - Protection Circuit
The protection circuit is an important part to ensure the safe operation of the stove, including the functions of over-current protection, over-temperature protection and short-circuit protection. When the furnace is abnormal, the protection circuit can automatically cut off the power supply, so as to avoid equipment damage or safety hazards.
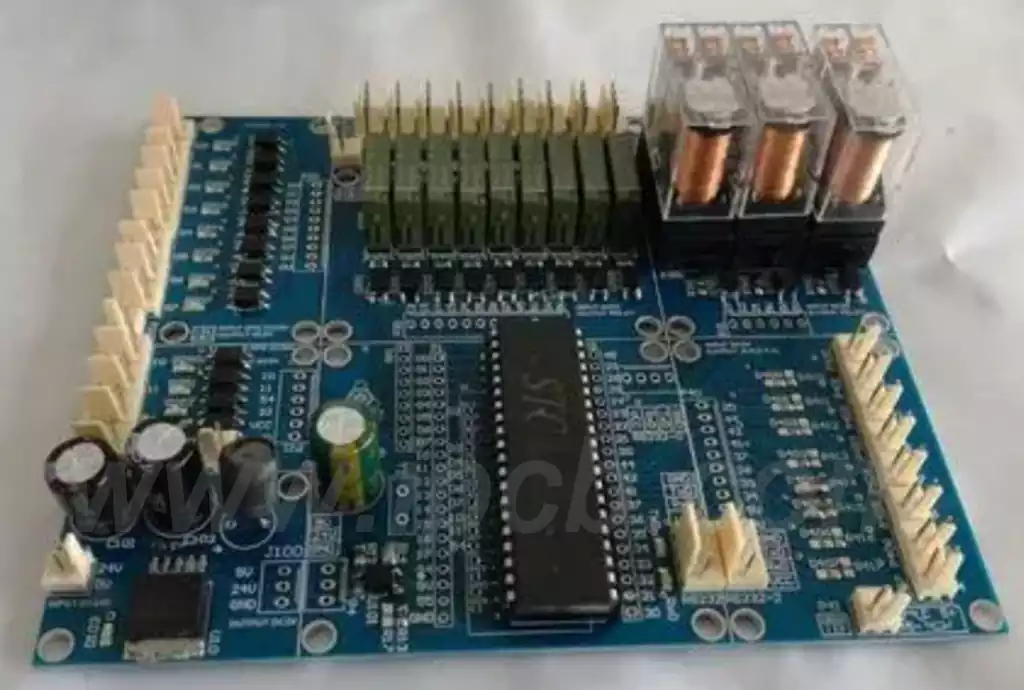
The main functions of the furnace control board
- Temperature control
One of the main functions of the furnace pcb board is temperature control. It monitors the temperature of the furnace surface in real time and adjusts the working status of the heating elements to ensure that the heating effect matches the temperature requirements set by the user. This function effectively prevents overheating and protects the safety of the equipment as well as prolonging its service life. - User Input Processing
The control circuit board needs to process inputs from the user, such as temperature settings, heating times, etc. Based on these inputs, the control circuit board will process the user inputs. Based on these inputs, the control circuit board generates the appropriate control signals to actually adjust the heating power and operating mode to achieve the desired cooking effect. - Safety Protection Function
Safety protection is an important part of the furnace control circuit board. It is equipped with over-temperature, over-current and short-circuit protection and other functions, when anomalies occur, it can automatically cut off the power supply, to prevent equipment damage or lead to potential safety hazards. - Command execution and control
The control circuit board acts as the “brain” of the furnace, which is not only responsible for converting user commands into control signals, but also actively monitors and controls the operation of several electronic components such as ignition, valve opening and fan starting. This multi-signal processing capability ensures that the furnace operates well under different operating conditions. - Fault Detection and Diagnosis
The furnace pcb board also has the ability to detect and diagnose faults. When the equipment is not working properly, the system can recognize the problem through the built-in algorithm and notify the user in advance for maintenance. This not only improves the reliability of the equipment, but also reduces maintenance costs.
Application areas of furnace control board
1.Home heating equipment
Furnace control circuit boards are widely used in home heating equipment such as gas stoves,electric ovens and electric water heaters. These boards are responsible for managing the heating process of the equipment, ensuring that a stable temperature is provided and energy consumption is effectively controlled.
2.Industrial heating equipment
In the industrial sector, furnace control board is used in medium frequency furnaces, induction heating machines and other heating equipment. The control boards for these devices are able to monitor and regulate the temperature in real time, ensuring uniformity and stability of heating through precise control.
3.Food Processing Industry
In the food processing industry, furnace control board is used to control equipment such as ovens and grills. These boards are able to set multiple cooking modes and monitor the cooking process of the food to ensure the quality and efficiency of the cooking.
4.Medical Equipment
Some medical devices, such as drying sterilizers and temperature control devices,also use oven control circuit boards. These boards effectively monitor and regulate the temperature of the equipment to guarantee proper handling and sterilization of medical devices.
5.Smart Home Systems
With the popularity of smart homes, furnace control board is also being integrated into smart heating systems. These systems can control the heating equipment through mobile apps or voice assistants, providing users with a more convenient experience.
Furnace control board plays a pivotal role in a number of fields, from household appliances to industrial equipment, and even medical equipment, are inseparable from its accurate temperature control and safety monitoring functions. With the continuous progress of science and technology, the future of the furnace control circuit board will be more intelligent, to achieve a higher degree of automation and remote control, to further enhance the user experience and equipment efficiency. By combining advanced microprocessors and intelligent algorithms, these control boards have the potential to meet the growing market demand and lead heating technology into a new era.