Cutting printed circuit board is the process of dividing a whole or linked circuit board into two or several pieces according to a reasonable line. This step is carried out without affecting the effectiveness of the circuit board, which is conducive to the secondary processing and recycling of circuit boards for remanufacturing.
Mechanical cutting of printed circuit boards
Cutting is a key step in the initial mechanical processing of printed circuit boards, which shapes the initial profile of the board. This basic cutting method is applicable to all types of substrates, especially for substrates up to 2mm thick. However, when working with substrates thicker than 2mm, the cut edges may appear rough and irregular, and therefore this method is not commonly used. The shearing operation may be done manually or electrically powered machinery, but in either case, the operating characteristics are similar.
Shears are usually equipped with a set of adjustable blades, which are rectangular in shape, with an adjustable angle of about 7° at the bottom edge, and are capable of cutting lengths of up to 1,000 mm. the longitudinal angle between the two blades is usually chosen to be between 1° and 1.5° to ensure accurate cutting, with a maximum angle of up to 4° when using epoxy glass substrates. In addition, the gap between the cutting edges of the two blades must be less than 0.25mm.
The choice of angle between the blades needs to be determined by the thickness of the material to be cut. The thicker the material, the greater the angle required. If the shear angle is too large or the gap between the blades is too wide, cracking may occur when cutting paper substrates. In the case of epoxy glass substrates, this may lead to deformation of the board, even though it has a certain bending strength and will not crack. To keep the edges of the substrate neat, the material can be heated in the temperature range of 30-100°C.
To ensure a neat cut, the plate must be held firmly in place by means of a spring-loaded device that prevents unwanted shifting during the shearing process. In addition, visual errors can lead to tolerances of 0.3-0.5mm, which should be minimized, and the use of corner markers can be effective in improving cutting accuracy.
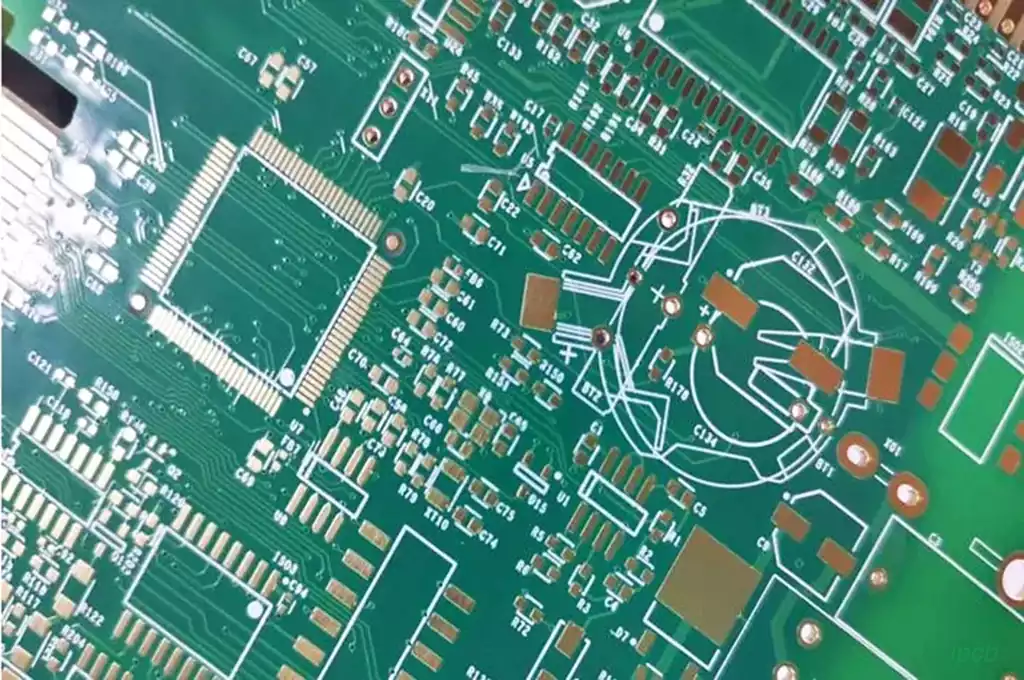
Shears are capable of handling a wide range of substrate sizes and provide accurate repeat dimensions. Larger machines are capable of cutting hundreds of kilograms of substrate per hour.
Sawing is another method of cutting circuit board. Although its dimensional tolerances are similar to shearing (0.3-0.5 mm), sawing yields smoother and neater edges and is therefore preferable.
In the electronic manufacturing industry, circular sawing machines are favored for their movable table. The speed of the saw blade can be adjusted in the range of 2000-6000r/min. However, once the cutting speed is set, it cannot be changed. This speed is achieved by means of a heavy pulley with more than one V-belt. The high-speed steel blade has a diameter of about 3000mm and cuts paper sound material at a rate of 2000-3000r/min with about 1.2-1.5 teeth per 1cm circumference.
For epoxy glass substrates, a blade with a tungsten carbide edge is recommended. Diamond wheels provide better cutting results and, despite the initial investment, are very beneficial for subsequent work due to their long service life and improved edge cutting. When the design of a printed circuit board contains shapes or irregular contours in addition to rectangles, the use of punch and cut dies is a fast and economical method. The basic punching and cutting operation can be accomplished with a punch that cuts neat edges with better results than a saw or shear. Sometimes punching and punching can even be done simultaneously. However, when good edge results or small tolerances are required, punching may not fulfill the requirements.
In the printed circuit board industry, punching is mainly used for cutting paper substrates and rarely for cutting epoxy glass substrates. Punching enables printed circuit boards to be cut to tolerances within ± (0.1-0.2mm). Punching of paper substrates Because paper substrates are softer than epoxy glass substrates, they are more suitable for cutting by punching.
When using a punching tool to cut paper substrates, it is necessary to consider the resilience or curvature of the material. Since paper substrates often rebound, the size of the punched portion is usually slightly larger than the size of the die. Therefore, when selecting the size of the tool, it needs to be based on the tolerance and thickness of the substrate to ensure that the size of the tool is slightly smaller than the expected size of the printed circuit board to compensate for the oversize due to springback. As has been noted, when punching, the die size should be slightly larger than the hole size, and when punching, the die size should be slightly smaller than normal.
For circuit boards with complex shapes, it is best to use a step-through tool that cuts strip by strip. This means that the shape of the material gradually changes as the tool punches through the material strip by strip. The holes are punched through in an initial step or two, and eventually the rest of the punch is completed. Heating before punching and dicing improves the cutting of printed circuit boards. For example, heating the slat to 50-70°C before punching and cutting. However, the heating temperature must be carefully controlled so that overheating does not result in reduced stretchability upon cooling. In addition, attention should be paid to the thermal expansion properties of the paper-based benzene sound material, as it exhibits different expansion characteristics in the Z-direction and Y-direction.
Punching of epoxy glass substrate
When shearing or sawing does not meet the requirements of the desired shape of the epoxy glass substrate, a special punching method can be used for punching. Although this method is not commonly used, it can still be used when the requirements for cut edges or dimensions are not too stringent. While functionally acceptable, the cut edges may not look neat enough. Since epoxy glass substrates have less resilient properties compared to paper substrates, the tools used to punch and cut epoxy glass substrates need to have a tight fit between the punch die and the punch press.
Cutting printed circuit board is an important part of the electronics manufacturing process. Choosing the proper cutting method and operating techniques can improve productivity and product quality, as well as contribute to environmental protection and resource utilization.