ICT Test (In-Circuit Test) is a widely used in-line testing method in the electronics manufacturing industry, designed to identify defects and bad components in the production process by testing the electrical properties and electrical connections of electronic components on circuit boards. The test can quickly and accurately identify faults on circuit boards, such as poor soldering and incorrect component mounting.
ICT test utilizes test fixtures and test pins to make physical contact with electronic components on a circuit board, applying voltages and signals to evaluate the performance of the assembly. By inputting a series of predetermined signals and measuring responses, the test system can determine if the component is functioning properly and if it is connected correctly.
Characteristics of ICT test:
- Simplicity of operation
ICT testing is designed to be easy to operate so that the user can quickly master the use of the equipment. The test process is usually realized through program control, reducing the dependence on the operator’s professional knowledge and making the test process more efficient. - Accurate fault localization
ICT testing is able to directly locate the specific cause of failure in connectors,solder joints,etc.This highly accurate troubleshooting capability makes the testing process more efficient.This high-precision fault diagnosis capability makes the repair process more efficient, can quickly identify the problem and take appropriate repair measures. - Fast test speed
The test method has the advantage of rapid detection,the test time of a single board is usually between a few seconds to tens of seconds. This greatly improves production efficiency and is suitable for mass production. - Wide range of applications
ICT testing is applicable to the detection of a wide range of electronic components and circuit networks,including resistors, capacitors, diodes and so on. It can assess the performance of components and circuits through quantitative testing to ensure product yield and reliability.
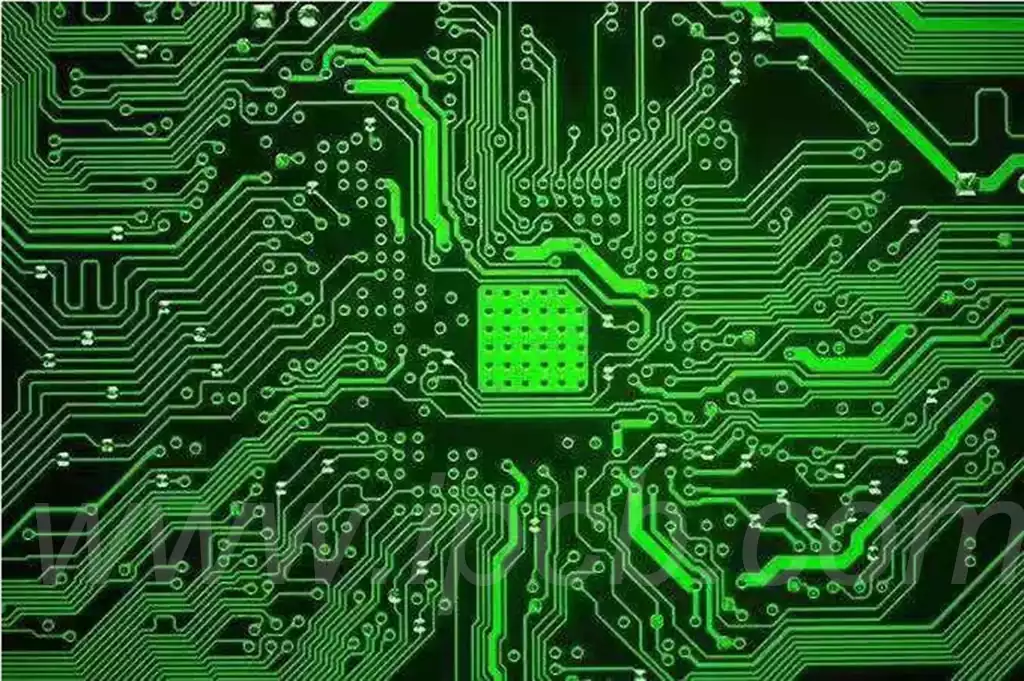
ICT (In-Circuit Testing) is a test method widely used in the electronics manufacturing industry,and its main applications cover a wide range of fields such as electronics manufacturing, automotive, communications, and medical devices.This kind of test can effectively detect the performance of electronic components and circuits on the PCB to ensure that they work properly according to the design specifications.
1.Electronics Manufacturing
In the field of electronics manufacturing, ICT testing is widely used to check whether the electronic components on PCBs (printed circuit boards) are installed and connected correctly. This process checks the electrical performance of each component, as well as common defects such as open or short circuits, to ensure that the basic circuit performance of the product is qualified.
- Automotive Electronics
In the field of automotive electronics, ICT testing focuses on monitoring the integrated circuit chips used in automotive control systems to ensure their function and performance. This improves the safety and reliability of automobiles, detects potential circuit problems in time, and ensures the overall quality of automobiles. - Communication Equipment
Communication equipment such as switches, routers and base stations also require ICT testing. The test can ensure that the circuit connections of these devices are normal, thus avoiding communication failures caused by circuit problems. Therefore, ICT testing plays an important role in the production of communication equipment. - Medical equipment
It is also indispensable in medical equipment. It is mainly used to test the electrical performance of medical equipment to ensure the reliability and safety of the equipment. This is essential to ensure patient safety and improve the quality of medical devices. - Industrial Controls
It is also used in industrial control systems to monitor and test the electrical performance of various industrial equipment. Such testing can detect potential faults in equipment in a timely manner, helping to maintain the normal operation of the equipment and improve productivity and safety. - Quality Control
It plays an important role in quality control by reflecting problems in production in a timely manner. Manufacturers can utilize this testing method to monitor defects in the manufacturing process, thereby reducing the defect rate and improving product quality.
The basic process of ICT testing:
Design test fixture: design a suitable test fixture according to the layout of the board and the location of the components to ensure that the test pins are connected to the board.
Development of test programs: write programs for testing, define the pins to be tested and the corresponding test methods, including the application of voltage, signal, etc. .
Execute Test: Place the PCB board into the test fixture, execute the predefined test program, record the test results and compare them with the expected values.
Analyze the results: Judge the function of the electronic components according to the test data. If faulty components are found, they can be labeled and processed.
Role.
Quality control: detect the electronic components on the PCB and its connection is normal or not,so as to improve product quality and reliability.
Manufacturing process control: monitoring the manufacturing process at different stages of production,timely detection and resolution of problems to reduce the defect rate .
Troubleshooting: Help identify and locate faulty components,shorten repair time and reduce maintenance costs.
Traceability: Record test results and related information to establish a product traceability mechanism.
ICT test, as an important testing tool in the electronics manufacturing industry, plays an important role in ensuring the quality and performance of circuit boards by virtue of its high efficiency and accuracy. By detecting the connectivity and electrical performance of electronic components, it can detect and solve potential problems in the production process in a timely manner, and effectively improve the reliability of products. It is widely used in many fields such as electronics manufacturing, automotive electronics, communication equipment, medical equipment and industrial control, and continues to provide support for enterprises to improve product quality and manufacturing efficiency.