SMT prototype board is circuit board manufactured using surface mount technology (SMT), which covers the process of integrating and soldering electronic components by means of this modern technology.SMT technology is the technique of mounting leadless or short-lead surface-mounted components (SMDs) directly onto the surface of printed circuit boards (PCBs), which allows for components to be laid out in a more compact manner, improving the integration and performance of the circuit board. .
Fabricating an SMT prototype board typically involves the following steps:
Design:The circuit board layout is designed using computer-aided design (CAD) software to ensure accurate component placement and connections.
Printing:Printing the circuit pattern on the copper foil of the PCB, followed by etching to form the circuit connection paths.
Soldering:A layer of solder is applied to the surface of the printed circuit board for subsequent component placement.
Component placement:Using automatic placement machines to accurately place various electronic components on the pads, this process requires strict mechanical control to ensure placement accuracy.
Soldering:Through reflow soldering or manual soldering, the components are permanently connected to the PCB and the quality of the soldering is ensured.
Inspection and Testing:The finished board is visually inspected, dimensionally inspected and electrically functionally tested to ensure that each component is soldered correctly and is functioning properly.
Factors to consider when designing and manufacturing SMT prototype board
1.PCB Design
PCB design is the basis of SMT prototyping, good design can significantly improve the performance and reliability of the smt prototype board.The design process should focus on the following aspects:
Pad size: pad size should be matched with the components used to ensure a smooth soldering process.
Component spacing: reasonable component spacing is not only convenient for component welding,but also reduces signal interference and heat buildup.
Wiring rules: Wiring should follow certain rules,such as avoiding sharp turns, keep the signal alignment of the short path, etc., to improve signal integrity.
An accurate and professional PCB design can directly affect the component placement effect and the overall performance of the circuit.
2.Material Selection
Choosing the right PCB material is critical to improving circuit board performance.Common PCB materials include FR4 and aluminum substrate,etc.Different materials have different electrical and thermal properties. Specific selection, the following factors should be considered:
Electrical properties: The appropriate dielectric constant and resistivity need to be selected according to project requirements.
Thermal performance: Special attention should be paid to the thermal conductivity of the material to ensure effective heat dissipation in high power applications.
Appropriate material selection not only optimizes product performance, but also ensures the stability of the circuit in different operating environments.
3.Production process
SMT prototype board process mainly includes the following links:
Solder Paste Printing: This is a key link to ensure the quality of soldering. Accurate solder paste printing can ensure the quality and quantity of solder joints.
Component mounting: In this section, need to ensure that all components are accurately mounted in place.
Reflow Soldering: The reflow soldering process requires temperature and time control to avoid overheating of components or poor solder joints.
Inspection and Testing: After completion, a full functional and cosmetic inspection is required to ensure that the circuit meets the design requirements.
Each step of the process requires strict process control to ensure that production is carried out in accordance with predetermined standards.
4.Environmental Control
Environmental conditions have a significant impact on the quality of SMT prototype board processing. Maintaining a proper operating environment can significantly improve the quality of soldering and the reliability of the final product. Focus should be placed on controlling the following points:
Humidity and temperature: should be maintained within the appropriate range, excessive humidity may lead to defective solder joints.
Cleanliness: Keep the production environment clean to minimize the impact of dust and impurities on weld quality.
Operation standardization: Direct hand contact with the component surface should be avoided during the welding process to prevent grease from affecting the welding.
5.Quality Inspection
Quality inspection is to ensure that SMT processing products meet the quality standards of the key links. Common tests include:
Appearance inspection: to confirm the appearance of components and solder joints are good.
Dimensional inspection: to ensure that the location and size of each component is consistent with the design standards.
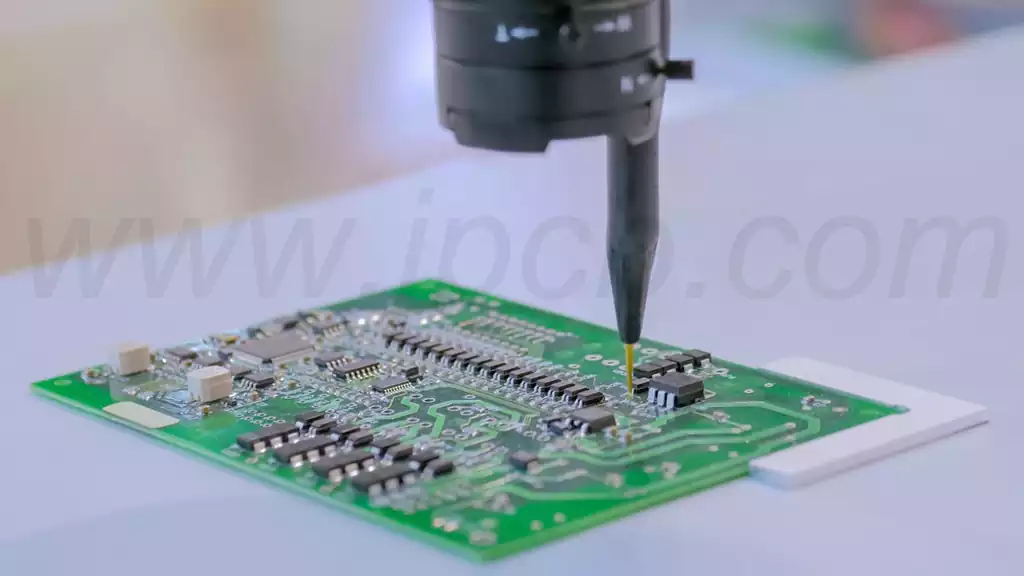
Common Challenges in SMT Prototype Board Fabrication
- Material Selection and Preparation
Selecting the right materials is critical in the SMT (Surface Mount Technology) prototyping process. Quality printed circuit board materials, solder paste that meets specifications, and components are all essential foundations. Improper material selection can lead to poor soldering or board damage. In addition, improper PCB surface treatment will also have a negative impact on the subsequent soldering process. - Solder paste printing accuracy
Solder paste printing is one of the key steps in the SMT process.The size and position of the solder paste must be accurate, otherwise it will lead to component placement instability or soldering defects. Printing process,the amount of solder paste is too much or too little will have a direct impact on the welding effect of the components, which may cause short-circuit or virtual welding and other problems. - Component placement and alignment
When picking and placing components, alignment accuracy is especially critical.Failure to accurately fit the components to the pads will result in poor soldering connections and even loss of functionality of the board.Common problems include the nozzle failing to pick up the component correctly or the component failing to be placed on the PCB.Therefore,the calibration of the machine and the skill level of the operator are both critical. - Reflow process control
As an important part of the SMT process,reflow soldering is a difficult process to control.Preheating,holding and soldering stages of the temperature settings must be accurate to prevent thermal shock on the PCB damage.Too high or too low a temperature will affect the quality of the solder joint.Therefore, strict monitoring of the equipment and temperature regulation is crucial. - Quality Inspection and Troubleshooting
After completing the SMT prototype board, quality inspection is an indispensable part of the process.However,recognizing defects is often a challenge, especially for components with small dimensions and multiple solder joint types, where defect detection can be more complex. In addition, depending on the soldering technique and design requirements, various types of defects may be encountered, making troubleshooting even more difficult. - Cost Control and Time Management
SMT prototyping often faces the double pressure of cost and time. In order to achieve efficient production,engineers need to ensure quality under the premise of cost control, which usually requires the purchase of materials, equipment selection and process flow to make informed decisions. In addition, time management is extremely important, as any delays can lead to longer development cycles, which in turn affects time-to-market.
In modern electronics development, the production of SMT prototype board is of paramount importance.It directly affects product functionality, performance, productivity and market competitiveness. The quality of SMT circuit boards can be significantly improved through rational design, material selection, production process control, environmental management and quality inspection. The development of such circuit boards is a delicate and systematic project. Only by striving for excellence in all aspects can we ensure the success and stability of the final product.
Solder joint inspection: Confirm the quality of solder joints through methods such as X-ray or automatic optical inspection.
Systematic quality inspection can effectively find and solve potential problems, thus improving product reliability.