LED stands for Light Emitting Diode, or Semiconductor Diode.LEDs are soldered to a printed circuit board with a chip that produces light through an electrical connection. A heat sink and a ceramic base are used to connect the chip. There is no doubt that the LED lamp board is the core of LED lighting. An LED lamp board tends to generate a lot of heat, but it is difficult to cool it with conventional methods. Metal core PCBs are widely used in LED applications because of their heat dissipation ability, especially aluminum is often used in PCB fabrication for LED lights. Usually,aluminum PCB contains a thin layer of thermally conductive dielectric material that can transfer and dissipate heat much more efficiently than traditional rigid PCBs.
Where can LED lamp board be used?
LED lamp boards offer excellent energy efficiency, low cost and maximum design flexibility so it can be incorporated into many lighting applications.
Telecom:LED indicators and displays are always used in telecom equipment due to the surrounding machinery and they have a high heat transfer capacity. Therefore, aluminum based LED lamp board plays an important role in their applications.
Automotive:Aluminum pcb led is also used in cars for indicator lights, brake lights and headlights,among other applications. There are some factors that make aluminum pcb ideal in the automotive industry such as durability and competitive pricing.
Computers:LED displays and indicators are becoming increasingly popular in computer applications. Due to the heat sensitive nature of computer machinery, aluminum pcb led is an ideal solution. In addition to LED applications, aluminum pcb’s are also used in computer components such as power supply units and CPU boards because of their ability to dissipate and transfer heat.
Medical:Lighting tools used in surgical procedures and medical examinations often use high-power LED lights,and these LED lights often use aluminum PCBs, largely due to the durability and heat transfer capabilities of aluminum PCB LEDs this ensures that the medical equipment operates correctly regardless of the number of patients circulating in the infirmary.In addition to lighting tools,medical scanning technology often uses aluminum PCBs.
LED lamp board works primarily by providing electrical connections and heat dissipation to support the efficient operation of LED chips. The following is a detailed explanation of the main working principles of LED PCBs:
- Principle of Current Passage
Light emitting diodes (LEDs) in LED bulbs are made of semiconductor materials. when current passes through an LED, the electrons and holes within it combine to release energy and emit it as light. the LED PCB provides a stable current distribution through its metal or copper conductors to ensure that the LEDs can work properly. - Circuit Connections
The LED lamp board is designed with circuits to connect multiple LEDs and their driver circuits together. The circuit design includes pads, alignments, and connectors, which are all critical pieces of information that ensure the smooth flow of current between LEDs. If the circuitry is not properly designed, it may result in uneven current flow, which can affect the brightness and efficiency of the LEDs. - Thermal Management
During use,LEDs generate heat,which,if not dissipated in time, may cause the LED chip to overheat, thus affecting its life and light output.LED PCBs are usually designed with aluminum-based materials or additional heat sinks to effectively manage and disperse heat. Good heat dissipation performance ensures that LEDs operate at safe temperatures, thus extending their life. - Functionality of structural design
The structural design of LED lamp board involves not only circuit connections, but also wiring, geometry and soldering positions. A proper structural design ensures a good connection between the LED and the PCB, allowing for an even distribution of current, while also helping to rapidly dissipate heat. A poorly designed PCB may result in poor contact with LED particles, affecting overall performance. - Driver circuit
LED lamp boards are usually used in conjunction with a driver circuit to provide the required constant current. The driver circuit converts the voltage of the power supply into a current suitable for LED operation. This constant current source effectively prevents LED burnout caused by voltage fluctuations. By precisely controlling the current, the driver circuit guarantees that the LEDs will work at a stable brightness.
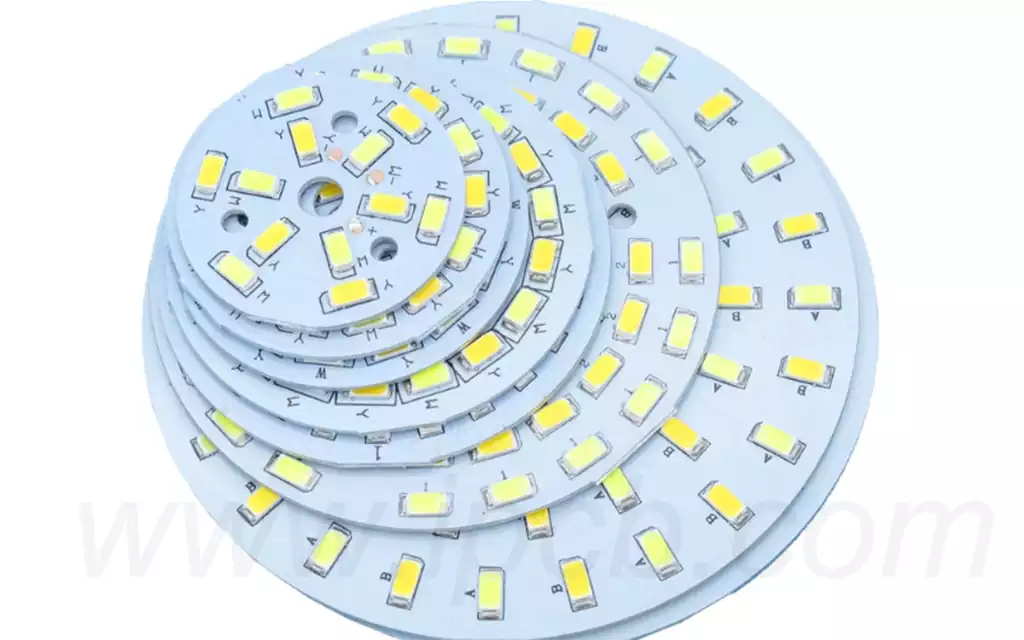
How to make an LED lamp board
- Determine the required functionality
First, determine your led lamp board requirements. Include specifications such as: size and weight limitations,power ratings (voltage and current), heat dissipation capabilities, environmental protection (IP rating), quantity and type of LEDs, etc.
Depending on your manufacturing method and equipment application, choose whether you need through-hole,surface mount,or chip-on-board LEDs.
Through-hole diodes are easy to assemble but take up more space
Surface mount LEDs save space,but can be challenging to install manually
COB lamps are more compact. However,their placement can complicate the manufacturing process.
- Design Creation
Design the board with PCB software such as Altium or KiCad.This part of the LED PCB fabrication process involves creating its schematic (or digital representation), including traces and electronic components.A good design program should help you do this without difficulty. - Material Selection
Choose the best material based on desired thermal performance, board size, weight or cost. Your choices are aluminum, copper alloys, CEM 1, CEM 3, ceramics, and one of the most common options, FR4.
FR4 is versatile, inexpensive, and offers excellent electrical insulation and durability.Metal cores,on the other hand, have good thermal conductivity and ability to dissipate heat, but are more expensive.
Ceramics are also expensive, but are a good choice if you want high dielectric strength and good heat resistance. If you are building flexible LED strip PCB boards, you need a lightweight material that can be bent without breaking.So choose the product that fits your application requirements.
- Board Layout
Create a physical representation of the led lamp board in your design program.Place all components in place, including the LED chips, and route them.
Do this keeping in mind the following factors: part spacing, thermal management (LEDs generate a lot of heat),EMI mitigation and crosstalk prevention.
Include vias and mounting or test holes in the layout. Simulate board operation to check for errors. After the layout phase, generate Gerber files for use in the fabrication phase.
- Board Fabrication
The led lamp board is now ready for fabrication.With your Gerber file in hand, find a company that specializes in manufacturing your board. Various LED PCB board manufacturers offer manufacturing services – all you need to do is provide your design files.
You can also choose to fabricate it yourself. This option is suitable if the PCB substrate is a simple circuit with through-hole diodes or if you only need a few pieces. On the other hand, if you are working with complex PCBs (e.g. multilayer types) or if you are producing them in series,we recommend leaving it to the experts.
Your manufacturer may only manufacture the boards and leave the assembly of the components to you or manufacture and assemble them at the same time. If you want to DIY fabrication and assembly, follow these steps:
Select a suitable substrate or core
Copy the design onto the board using photo paper
Using chemicals, etch out copper in the desired locations
Clean the board to remove chemicals and other residues
Drill holes and create vias as needed
Solder components, including LEDs, to the board
Power up the assembled board and test its functionality
- Testing
Check to make sure the finished LED board works as expected and fulfills the functions you specified. This step allows you and the manufacturer to confirm all requirements and avoid potential losses from design and manufacturing errors.
The manufacturer will also perform a series of tests on the board to assess its performance and reliability as well as other quality requirements. The inspection process may involve manual or automated steps and includes the following test methods:
Electrical testing
Visual and automated optical inspection
Vibration or shock testing
When selecting a led lamp board, the key factors to ensure its performance, reliability and adaptability to the application requirements are:.
- Heat dissipation performance
Heat dissipation is one of the primary considerations in selecting LED light PCBs. Aluminum PCB is favored for its excellent thermal conductivity, which helps to dissipate heat effectively and prevent LED chips from being damaged due to overheating. As the LED will generate a lot of heat when working, the use of PCB materials with effective heat dissipation capabilities is essential. - Substrate materials
LED lamp PCBs are commonly used in different substrate materials,including metal core, epoxy resin and FR-4 materials. Metal core PCBs, especially aluminum-based PCBs, are preferred for many LED applications due to their superior thermal conductivity. Choosing the right substrate material will directly affect the durability and performance of the PCB. - Structural design
The structural design of LED light PCB is also very important. The design needs to consider the LED layout, pad size and alignment path to ensure the best electrical connection and thermal management.Chip-on-board (COB) and SMD (SMD) technology for different applications have different design requirements, which should also be considered in the selection. - Current and voltage requirements
LED lamp PCB design and materials must be able to withstand the current and voltage requirements of the device.PCB design needs to prevent current overload to ensure stable operation of the LED and avoid undesired changes in light output due to voltage fluctuations.Understanding the required operating voltage range and current characteristics is critical to selecting the right PCB. - Cost and Recyclability
Finally, cost and material recyclability are also important factors to consider when selecting PCBs for LED lights.Aluminum-based PCBs are less expensive to produce and more environmentally friendly, so they are becoming popular in modern applications.Choosing a material and design that balances production costs and environmental impact ensures an economical and sustainable solution.
When choosing LED lamp board, attention needs to be paid to key factors such as thermal performance, substrate materials, structural design, current and voltage requirements, as well as cost and environmental friendliness. These considerations will ensure the performance and reliability of the LED luminaire, enhance usage efficiency and extend product life.