The lead melting points is generally 183°C-190°C, depending on the ratio of lead to tin. Lead solder is a type of solder commonly used to connect electronic components, and its components are mainly lead and tin. In practice, in order to improve the strength and heat resistance of the solder joints, sometimes also add other ingredients, such as silver, copper and nickel, etc., the addition of these ingredients will make the melting point change.
A variety of elements combine to contribute to the melting temperature of lead solder. One of the most critical elements is the ratio of lead to tin. An increase in the proportion of lead results in a corresponding decrease in the melting point; conversely, an increase in the proportion of tin results in an increase in the melting point. In addition, the ambient temperature, the size and shape of the solder joint, and the heating rate are also factors that cannot be ignored. Generally speaking, the melting point will increase when the size of the solder joint increases;while the melting point tends to decrease when the heating rate is accelerated.
The significant difference in melting point between lead free and leaded solder is rooted in their unique composition. Leaded wire contains the element lead (Pb), while lead-free wire discards lead in favour of other metal alloys.
The lower melting points of leaded solder is due to the low lead melting points,which is about 327 degrees Celsius.Common leaded solder compositions include tin (Sn) and lead (Pb) in proportions that may be 60% tin and 40% lead (Sn60Pb40),or more commonly 63% tin and 37% lead (Sn63Pb37).These ratios have a melting point of about 183 degrees Celsius to 190 degrees Celsius,allowing for a smoother soldering process with less thermal impact on the electronic components.
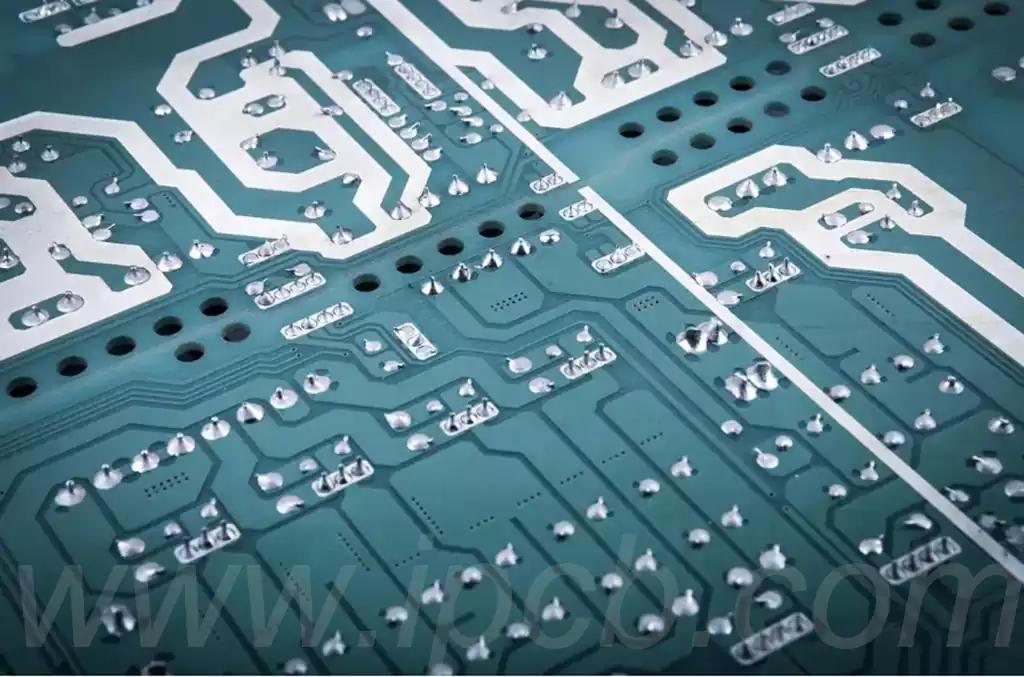
In contrast, lead free solder has a higher melting point because they do not contain lead. They are usually composed of metal alloys of tin, silver (Ag), and copper (Cu) in proportions such as Sn96.5Ag3.0Cu0.5, Sn99.3Cu0.7, or Sn95.5Ag3.0Cu1.5. The lead melting point of these alloys is typically between 217 degrees Celsius and 227 degrees Celsius, which is about 30 to 40 degrees Celsius higher than leaded solder wire. As a result, lead-free soldering requires higher temperatures, which may cause greater thermal stress on electronic components.
In addition,lead free solder may not be as wetted as leaded solder during the soldering process.Wettability is the ability of the solder to come into contact with the surface of the material being soldered and form an even coverage. Due to the higher melting point of lead free solder,they may not flow and cover easily during soldering, thus affecting solder quality and reliability.
However,lead free solder is used for environmental and health reasons. Lead is a toxic heavy metal, and long term exposure may cause serious harm to human health.Therefore,many countries and regions have banned or restricted the use of lead in electronic products, promoting the widespread application and development of lead-free soldering technology.
In the electronics manufacturing industry, the choice of lead solder and lead free solder is not only related to product performance and quality, but also closely related to environmental protection and health. Leaded solder and lead free wire have their own advantages and disadvantages, the choice of which solder depends on the specific application scenarios and needs.In the pursuit of high performance and reliability at the same time, we should pay more attention to environmental protection and health issues, and actively promote the development and application of lead-free soldering technology, in order to build a greener, healthier electronics manufacturing industry to contribute.