A metal core PCB, also known as an MCPCB, insulated metal substrate (IMS), or heat sink PCB, is a type of printed circuit board that has a metal core layer integrated inside. This type of circuit board usually consists of a metal substrate, an insulating layer, and a conductive layer. Unlike conventional FR-4 PCBs, the metal layer of a metal core PCB not only provides mechanical support, but also has excellent thermal conductivity. This structure allows metal core PCBs to excel in high-power, high-heat-generating electronic devices, especially in areas such as LED lighting, power modules and automotive electronics.
The basic components of an metal core PCB:
Solderproof layer
Conductive circuit layer
Copper foil layer
Insulation layer
Metal substrate layer
and heat sinks
The base material used for these metal core PCBs is metal, rather than the traditional FR4 or CEM3 materials.Aluminium, steel alloys and copper are the most common metal materials.Aluminium is popular because of its low price and excellent heat dissipation and conduction properties.Copper is superior to aluminium and stainless steel in terms of heat dissipation and conduction efficiency,but its cost is relatively high.Stainless steel is known for its higher hardness and lower thermal conductivity than copper and aluminium.
Therefore, the choice of metal substrate needs to be based on specific application scenarios.
Metal core PCB stands out in many industrial applications due to the following advantages:
Excellent thermal conductivity: Compared with traditional PCBs made of FR4 and CEM3 materials, the weak interlayer insulation and low thermal conductivity may lead to an increase in internal temperature, threatening the safety of components. Aluminium metal PCBs ensure the safe operation of internal components due to their excellent thermal conductivity.
Outstanding dimensional stability:Compared to FR4 or CEM3 PCBs,metal core PCB has better dimensional stability.When the temperature of the aluminium PCB rises from 30 degrees Celsius to 140 to 150 degrees Celsius, the dimensional change ranges from only 2.5% to 3%.
Higher Thermal Expansion:The coefficient of thermal expansion (CTE) is a measure of how much a substance expands or contracts in response to temperature changes. Aluminium and copper have a higher CTE than common FR4 materials and have thermal conductivity between 0.8 and 3.0 W/mK.
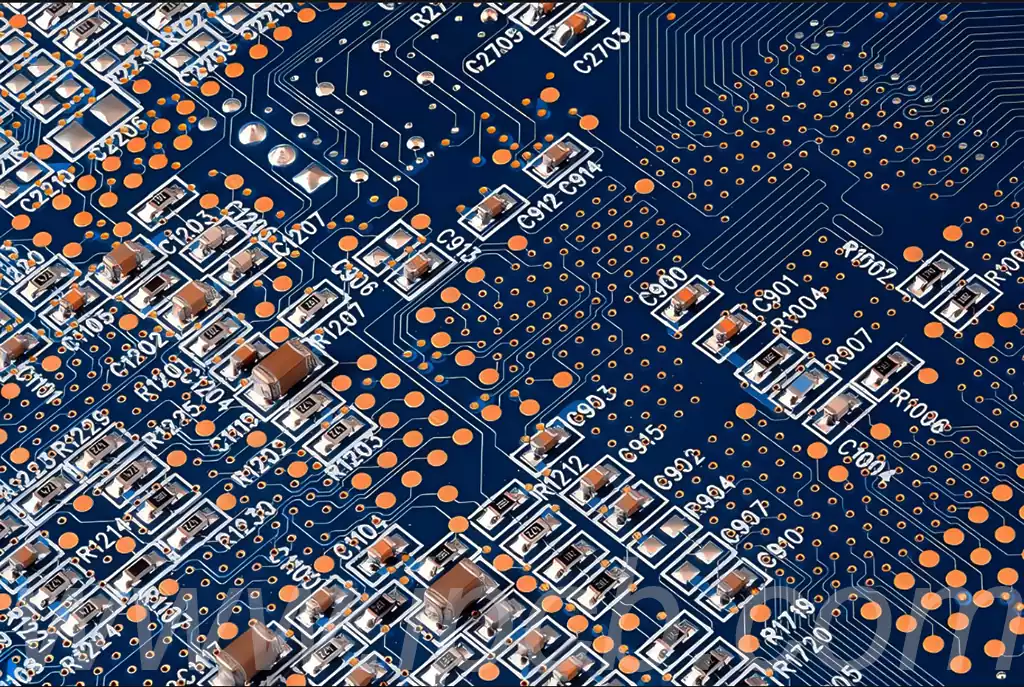
Process ways to improve the thermal conductivity of metal core pcb:
Selected metal core material: the material of the metal core has a direct impact on the thermal conductivity. Commonly used metal core materials include aluminium, copper and iron-nickel alloys.Copper is known for its excellent thermal conductivity, but at a higher cost; Aluminium has a cost advantage and is lighter in weight, even though its thermal conductivity is slightly lower than that of copper; and Iron-nickel alloys are excellent in matching the coefficient of thermal expansion, which makes them suitable for specific application scenarios.
Optimise core size: The thickness and size of the core has an impact on its thermal conductivity.
Increasing the thickness of the core can improve thermal conductivity, but it also increases cost and weight.Therefore, it is necessary to find a balance between thickness and cost according to actual usage requirements.
Strengthening the bond between the metal core and the substrate: The stronger the bond between the metal core and the substrate, the better the thermal conductivity.The bonding strength can be enhanced by improving the adhesive formulation or adopting more advanced bonding processes.
Application of thermally conductive filler media: The use of thermally conductive filler media, such as thermally conductive adhesive, thermally conductive spacers, or thermally conductive silicone grease, in specific areas of the PCB can further enhance the efficiency of thermal conduction.
Proper design of wiring and layout: The wiring and layout of the PCB will affect the distribution of heat. By optimising the wiring and layout, the heat will be distributed more evenly on the PCB, which will help to improve the overall thermal conductivity.
Selection of high performance substrate materials: the thermal conductivity of the substrate material has an impact on the overall thermal conductivity of the metal core pcb.Selection of substrate materials with high thermal conductivity can improve the thermal conductivity of MCPCB.
Surface treatment optimisation: The use of appropriate surface treatment processes, such as gold immersion, tin immersion or OSP (organic protective film), etc., can reduce the surface resistance and thus improve the thermal conductivity.
Integration of heat pipes or vapour chambers: Integrating heat pipes or vapour chambers into metal core pcb, especially in high power applications, can significantly improve heat transfer efficiency.
Thermal simulation and analysis applications: Thermal analysis using thermal simulation software during the design phase can help predict and optimise the thermal performance of MCPCBs.
Enhanced quality control and testing: Strict quality control and thermal performance testing can ensure that the thermal conductivity of metal core pcb meets design requirements.
As a key component in modern electronic devices, metal core PCB (MCPCB) has demonstrated significant advantages in high-power, high-heat-generating application scenarios thanks to their excellent performance. In the future, with the continuous progress of electronic technology and the research and development of new heat dissipation materials, the performance of MCPCB will be further improved and the application areas will be more extensive.As an important part of thermal management of electronic devices, metal core pcb will continue to move forward on the road of high power density and efficient heat dissipation, contributing to the construction of smarter, more reliable and efficient electronic products.